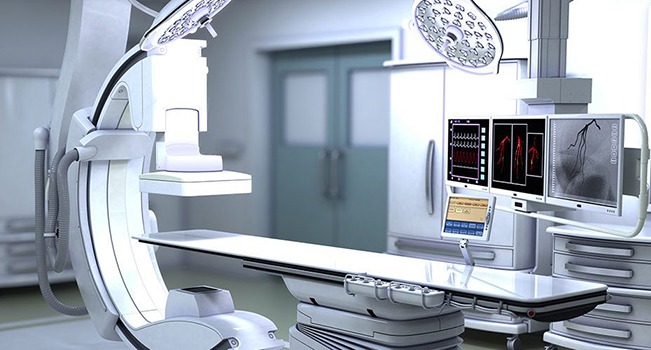
The medical manufacturing industry faced a war on multiple fronts during the pandemic. Just as demand for medical supplies like masks and respirators was at its highest – and unexpectedly, too – employment dropped and supply chains were broken. Manufacturers were expected to continue to produce high-quality, high-precision medical products even as they struggled to acquire materials, staff their shops, and even ship the finished parts.
Experts predict that this supply chain disruption could persist into 2024, leaving medical manufacturers struggling not only to turn a profit but to aid the health industry. CNC machining, the process by which machinists use code to automatically run a machine like a mill, router, or lathe, can help these manufacturers produce parts faster and more efficiently. In turn, hospitals, hospices, and other clinics receive the supplies they need in time.
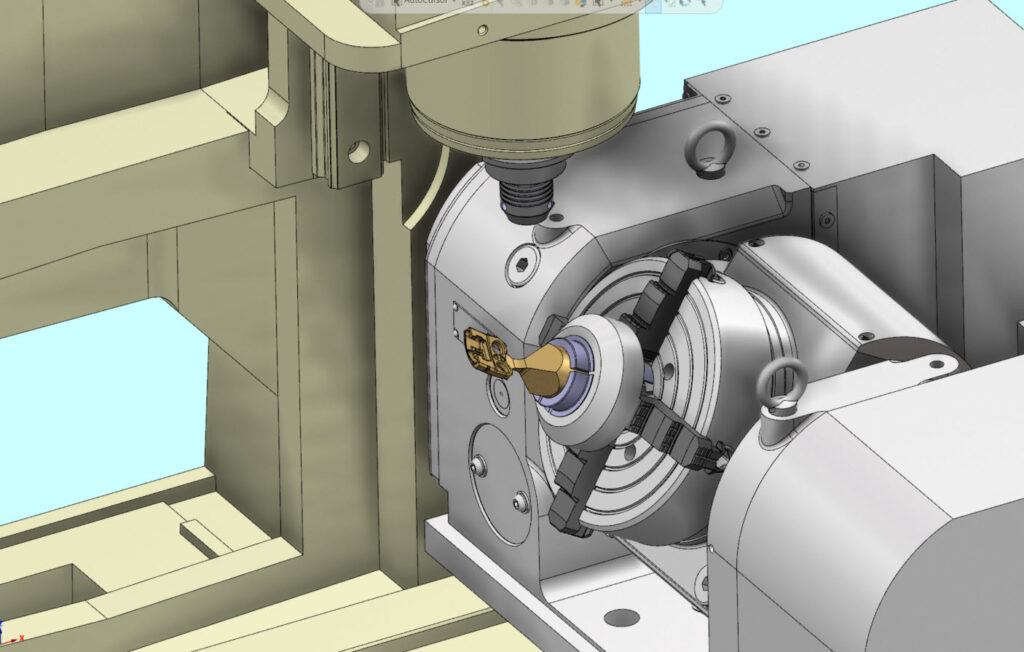
Why is CNC machining used for the medical industry?
Many medical supplies, like plastic face shields, are made with injection molding. To create the best molds for consistent and repeatable injection, CNC machining is used. CNC machines are fundamentally more accurate and faster than their manual counterparts. This makes their machined products more accurate as well. For machined products with even tighter tolerances, like prosthetics and medical machinery, this becomes incredibly important.
What are the applications for CNC machining for the medical industry?
CNC machining can produce high-grade surgical instruments, components for medical machines like pacemakers, and even devices that are surgically implanted into patients. For example, bone screws are the perfect part to make with a Swiss CNC machine.
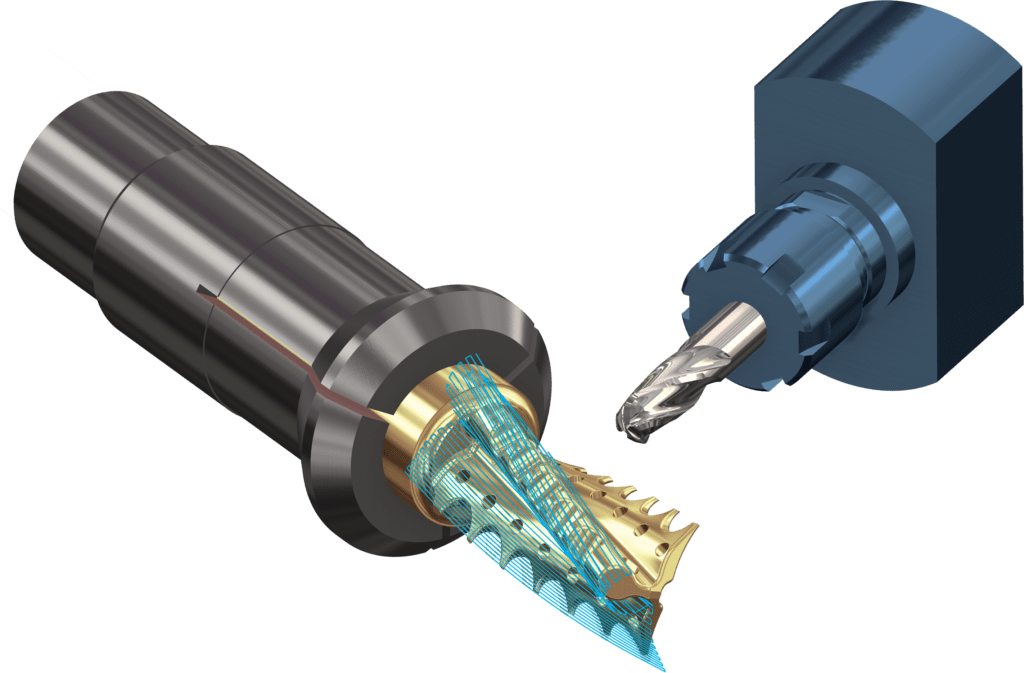
These screws can be as little as one millimeter in one direction, have alarmingly tight tolerances, and require flawless finishes to eliminate patient discomfort and even part failure. They cannot be cut with fluids because of contamination concerns, so the only way to make them is with CNC machining. And the best way to cut a part with a large length-to-width ratio is with Swiss machining.
What materials are used?
Any medical part must be designed with either sterilization or disposal in mind, in addition to having specific tension and malleability requirements. The usable materials for the industry reflect this. Approximately four out of five medical devices are made from stainless steel because of its resistance to oxidation and its ease of machining. Titanium alloys are quickly becoming more popular, however, because titanium’s elasticity more closely resembles a bone’s than stainless steel does. Some ceramics, polymers, and composites are also used. More materials research is being done every day.
Mastercam CNC machining capabilities for the medical industry
With the added complications inherent with medical machining – machining tough titanium, having to cut without coolant while still maintaining safe heat levels, and meeting tight tolerances – cutting without a powerful CAD/CAM suite is next to impossible.
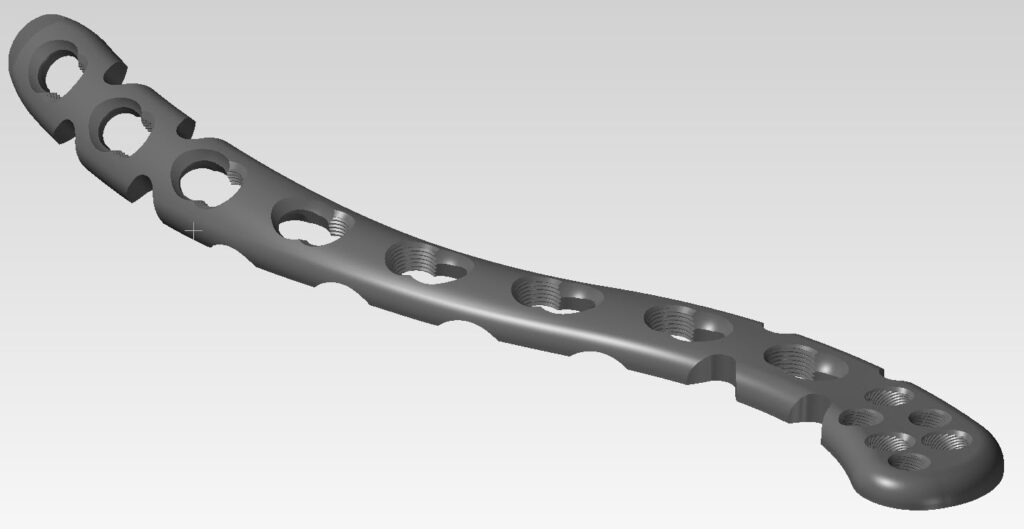
Mastercam software offers the support that can make even the smallest medical manufacturing shop compete at the same level as an international supplier. In medical manufacturing, speed is nothing without precision and reliability. Mastercam provides CAD/CAM software solutions to meet the rigorous demands of industry in this field, including:
- Ability to import, create, or cut virtually any CAD model.
- Wide range of CAM tools for solving complex machining issues.
- Dynamic Motion™ adjusts feeds, speeds, entry points, and dwell for faster cutting with less tool wear.
- High-precision toolpaths for cutting extremely small parts.
- Streamlined 5-axis cutting, trimming, and drilling.
- Trimming is a fast tool for eliminating burrs on critical medical parts.
- Simulation verifies in-spec material removal and detects interferences.
Explore Mastercam Solutions for the medical industry to learn more.