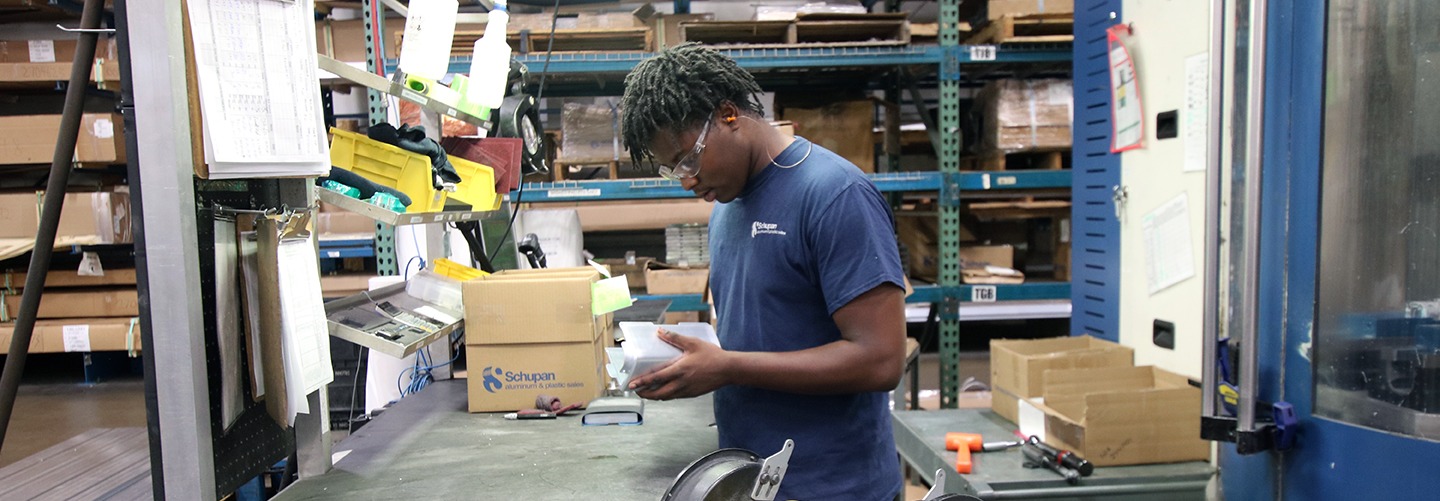
Schupan Relies on Multiaxis to Cut Cycle Times
When the experts at Schupan & Sons, Inc. Metal Service Center analyzed possible ways to optimize their machining operation, they decided that reducing cycle time was the best way to become more efficient. By using Mastercam’s Multiaxis and Dynamic Motion toolpaths, Schupan not only decreased cycle times but increased accuracy.
Quick Facts:
- Product Used: Multiaxis
- Industry: Job Shop, Aerospace
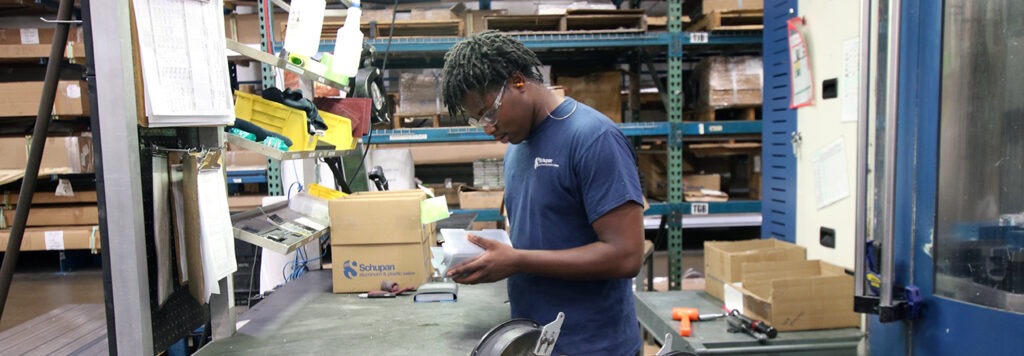
Project Details
- The Challenge: Reducing cycle times on parts that required multiple operations to machine.
- The Solution: Mastercam, the most widely used CAD/CAM software for machining applications.
- Benefits:
- Network of knowledgeable, experienced Resellers who can introduce and explain new techniques and functions.
- Powerful Multiaxis toolpaths to reduce operations and expand a shop’s capabilities.
- Tool Manager for importing tool libraries from tool manufacturers.
- Advanced simulation tools like Verify and Backplot to highlight errors before they occur.
- Dynamic Motion technology that reduces cycle times without sacrificing tool life or stock material safety.
Schupan & Sons, Inc., has been a community staple for decades, ever since its founding in 1968 as a metal recycling company. The family-owned company has exploded into an international powerhouse that operates scrapyards, distributes aluminum and plastic mill products, and processes and brokers used beverage containers. As Schupan grew, it became clear that reducing cycle times was the best way to make production more efficient.
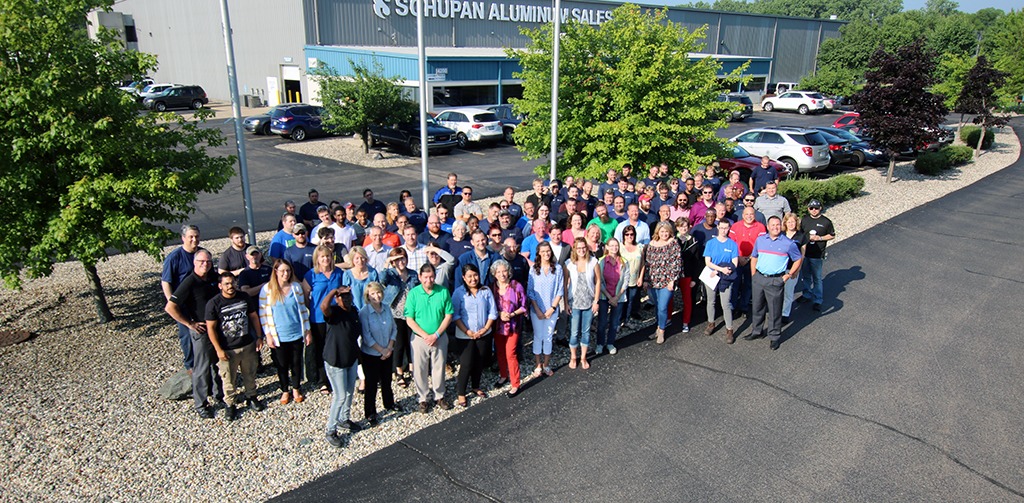
“Fixturing, historically, has been a huge problem for us. We had a lot of parts that would certainly be three or four operations, and we had to design custom solutions to make those in one operation,” said Lead Manufacturing Engineer Joseph Proxmire. In response to this issue, Schupan started using 4- and 5-axis machining to load multiple parts and cut multiple sides at once. To ensure fast, clean machining, they trust Mastercam. The software’s multiaxis toolpaths give users complete control over cut pattern, tool axis control, and collision avoidance. “I’ve used many different CAM software packages and this one is my favorite. It’s always been my go-to, the easiest to work with, the fastest to make cutter paths on,” said Proxmire. His was a deciding voice in which software Schupan chose to use to expand their capabilities. “It’s constantly being updated, and the developers are always advancing the software. Other CAM software that we’ve used before don’t have enough data to stay updated.”
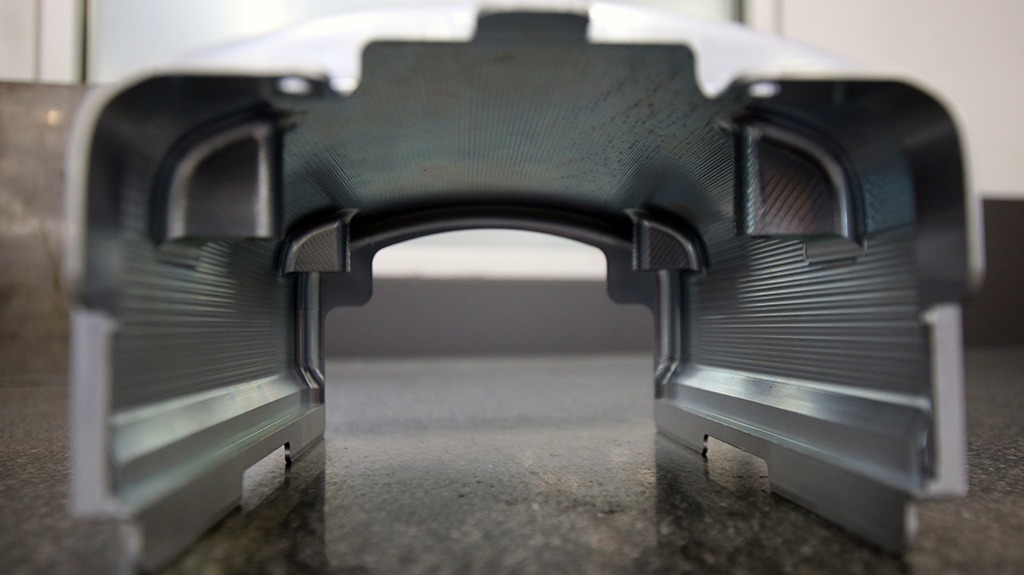
One of Schupan’s more challenging projects was to produce a couple different complex aluminum shrouds. These are one of the interior furniture components for an airplane and, at first, held some daunting geometries. “We needed those advanced 5-axis capabilities for deep pocketing, small-tool holding, and extended tool holder use. We ended up with very good finishes because of these toolpaths,” said Proxmire. “We used the Multiaxis Flow and Multiaxis Curve toolpaths to machine features that would’ve been much more difficult to machine with 3- or 4-axis machining. We ended up with surface finishes that were much better than anything we could’ve achieved with the traditional 3-axis toolpaths.” The complicated tool positioning was hardly a challenge with Mastercam’s 5-axis features, whereas the part might have taken many times as long without it. During the project, Schupan reached out to their certified Reseller, Axsys CAD/CAM Solutions, Inc. (Wixom, MI) for help with post processing. Instead of simply walking the Schupan team through the post, account representative Mike Stevens developed the entire code for them. Between the support from Axsys and the advanced multiaxis functions, the stress and difficulty surrounding the shroud project was all but eliminated.
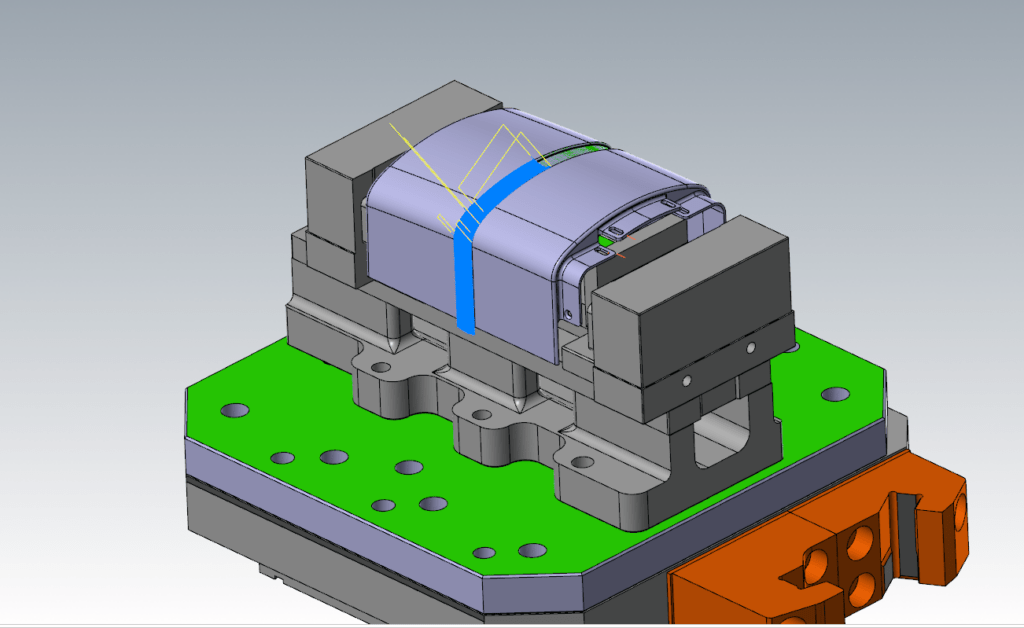
Proxmire and his programmers can call Axsys whenever they have questions or need help troubleshooting or optimizing their machining process. “Whenever we have a problem, Mike Stevens is our go-to. I’ve got his personal cell phone number. I can always get ahold of him and he always gets me the information I need right away. He’s local too, so if we have a problem he can’t fix over the phone, he is here right away to take care of it,” he said. Axsys offers continued training for users of the software in their area, and they frequently reach out to companies like Schupan to go over the software’s ever-expanding features.
One such feature is the software’s extensive Tool Manager. Users can import tool libraries from respected tool manufacturers like Sandvik Coromant, optimize the paths for each tool, and then extrapolate the information. “The ability to create one cutter path and transfer it to multiple locations is huge. I use that for programming one part and then transforming it down the line for 10 different parts. This software is very good with that as far as approaches and clearance planes and fine tuning the cutter path to make it as fast as it can be. We have old tool libraries and tool holder libraries for all of our shrink fit and CAT 40 tool holders. It makes it a lot easier for simulation.”
When Proxmire simulates his parts, he uses the Verify and Backplot functions within the software. Many CAD/CAM software suites require expensive additional simulation software, but Proxmire is confident in his setup. Verify and Backplot both display onscreen any and all portions of the machining process, which users have the ability to record if they need to. Because collisions and errors are detected before the parent material ever touches the machine, operators can work through projects much faster and with greater confidence.
After simulating each part to check for any problems, Proxmire’s focus is once again on reducing cycle times. Dynamic Motion technology is a sophisticated program within the software that continuously monitors the material during machining and changes tool motion in response. This accommodation for material movement means that operators can run machines at their highest rates without endangering their material or cutting tools. “The tool lasts quite a while longer now, especially when we’re machining harder materials like tool steel. We found that Dynamic Milling gives us better tool life and definitely higher metal removal rates,” said Proxmire. He estimates that when machining steel, cycle times are now up to three times shorter from just Dynamic alone.
Customer Quote
“I’ve used many different CAM software packages and this one is my favorite. It’s always been my go-to, the easiest to work with, the fastest to make cutter paths on. It’s constantly being updated, and the developers are always advancing the software. Other CAM software that we’ve used before don’t have enough data to stay updated.”
– Joseph Proxmire, Lead Manufacturing Engineer