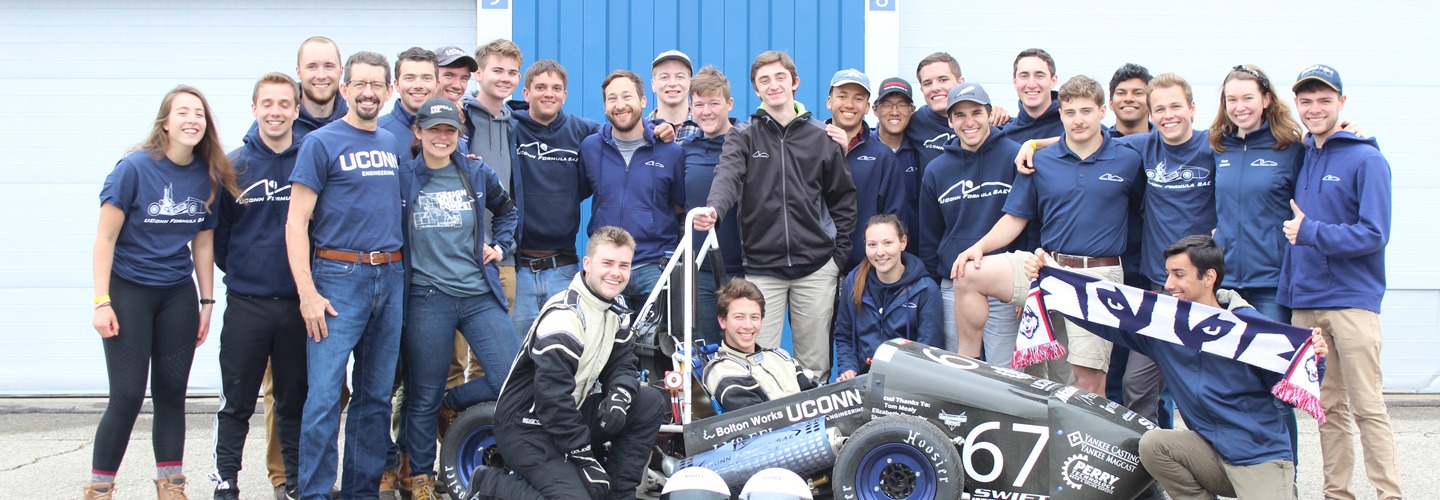
CAD/CAM Software Keeps Racecar Design and Production on Track
Students at the University of Connecticut School of Engineering in Storrs, Connecticut, enjoy a host of extracurricular opportunities. Few measure up to the hands-on experience provided by the UConn Formula SAE project. Organized by SAE International (formerly Society of Automotive Engineers), the Formula SAE (FSAE) series design competition challenges teams of university undergraduate and graduate students to design, build, and test a Formula-style racecar for the non-professional weekend autocross racer.
Quick Facts
- Product Used: Mastercam for SOLIDWORKS, Mill
- Industry: Education, Automotive
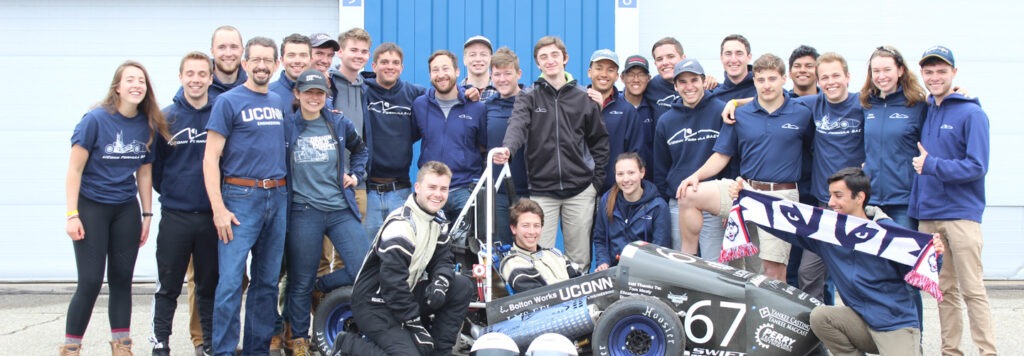
Project Details
- The Challenge: Design, produce and test a Formula-style racecar for the Formula SAE series design competition.
- The Solution: Mastercam, the most widely used CNC software for CAD/CAM operations.
- Benefits:
- Students program parts in Mastercam for SOLIDWORKS then access the machining tree for quick access to any point in the machining process.
- Fully associative toolpaths permit changes without slowdowns.
- Stock Modeling, Toolpath Verification, and Simulation feature to ensure user confidence.
- Tool Manager function provides an efficient way to create and organize tooling assemblies.
For many years, the UConn FSAE team has traveled to Michigan International Speedway in Brooklyn, Michigan, to compete in the annual international Formula SAE competition. Mastercam has been the team’s title sponsor for the past several years. In 2019, the event was held on May 8 – 11.
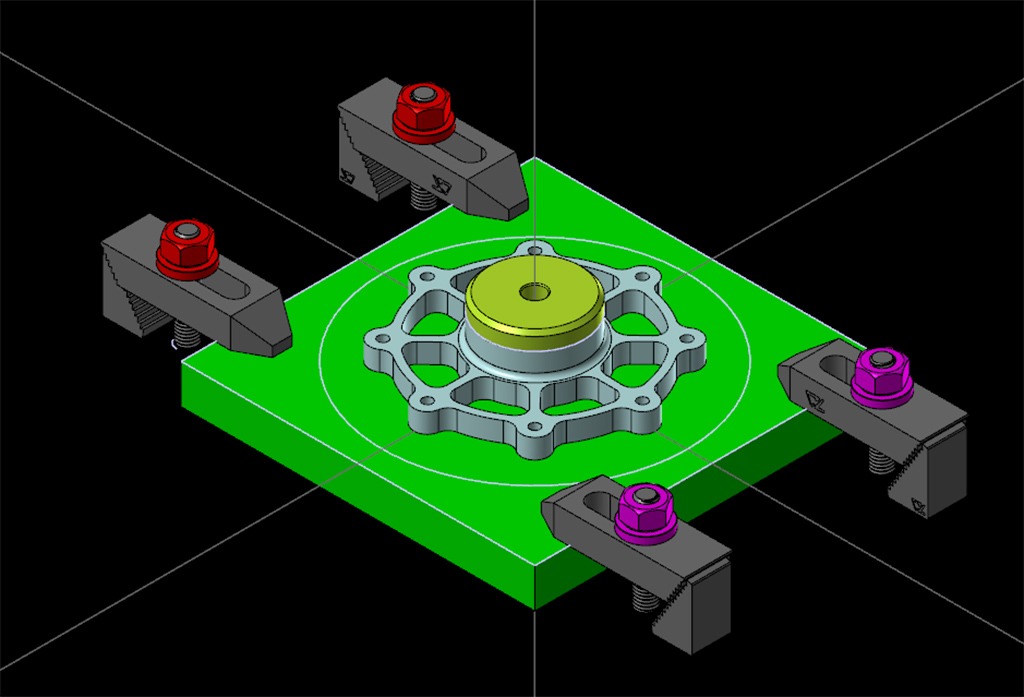
“Every year, we’re standing on the shoulders of giants,” said Dylan Palin, a mechanical engineering student and president of the University of Connecticut FSAE team. “There’s a long history of brilliant members who made a lot of headway with difficult design, studies, and testing.”
The starting point for the UConn racecar is the development of the chassis, which requires finalizing frame and suspension designs. The team chose 4130 chrome alloy steel for the construction of the frame. For the wheels, it runs cast magnesium uprights for optimized weight reduction; 6061 aluminum and 4130 steel tubing are used for the suspension. Additional magnesium parts include the rods for differential mounts and the engine oil pan. In-house manufacturing is performed on CNC machining centers and manual mills and lathes. Team members use Mastercam to design their parts and run machine tools.
“This is a huge help for us because writing G-code is an acquired skill,” said Palin. “Mastercam makes it accessible for all of us. We do all of our design work in SOLIDWORKS.”
Users can program parts directly in Mastercam for SOLIDWORKS then access the Mastercam machining tree for quick access to any point in the machining process. Fully associative toolpaths permit changes without slowdowns, and Stock Modeling, Toolpath Verification, and Simulation feature to ensure user confidence on every project. The Tool Manager function provides an efficient way to create and organize tooling assemblies. Once a part is programmed, job elements can be modified, and toolpaths are immediately updated.
“Mastercam is used in-house during the manufacturing phase to machine our steering rack mounts, differential pillow blocks, bell cranks, and other small parts,” said Kenneth Brown, UConn FSAE chief engineer. “The Applications Team at Mastercam handles some of our more complex parts, including our combination hub spindle and sprocket adapter.”
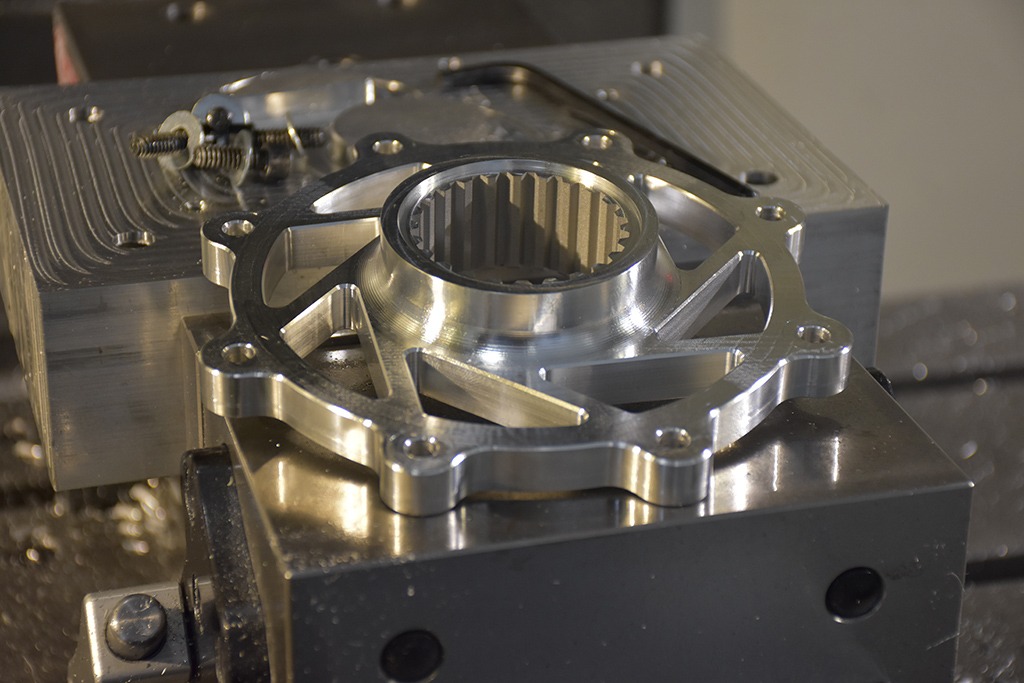
For parts machined in-house, UConn engineering team members use mainly 2D contour toolpaths because their racecar part geometries are not highly complex; 2D contour is a straightforward toolpath that is easy to learn and use. Brown adds that the team relies on Verify, a Mastercam feature, to check for gouges and view the finished shapes of parts in the Verify simulation screen. Productivity increases and problems are addressed before parts are ever cut. Programmers can verify on a separate thread while continuing to program, saving valuable production time.
“We really enjoy using Mastercam’s Verify feature when machining parts for the racecar, because it allows us to check for tool collisions and make sure the selected toolpath and parameters machine the desired features,” said Brown.
One challenge that the team faced involved standard machining and tolerancing of the frontal brackets and pillow blocks for the differential. In this case, running standard toolpaths for the sprocket adapter was not an option. The design has a standard bolt pattern but issues concerning tolerancing and blade speed arose. For parts that require machining beyond the university’s shop capabilities, the team looks to the experts at Mastercam.
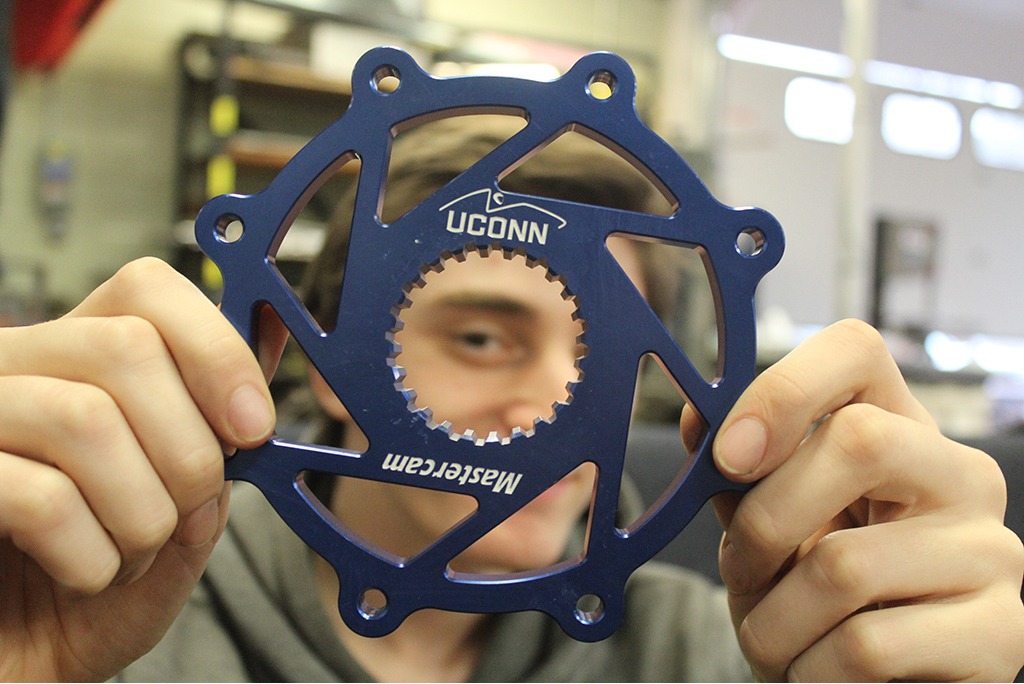
“Mastercam has done a lot of machining for us, especially on special design components like the sprocket adapter, one of our more unique designs,” said Palin.
The ongoing collaboration between University of Connecticut engineering students and Mastercam has a proven track record. In the previous season, the UConn team produced the fastest non-aerodynamic car without an aerodynamic package and was one of the only teams to complete the endurance requirement, arguably the most difficult leg of the FSAE competition.
“We run a pull-rod suspension, which very few teams do,” Palin said. “We don’t have a million-dollar budget. We take pride in the fact that we make do with what we have in the shop.”
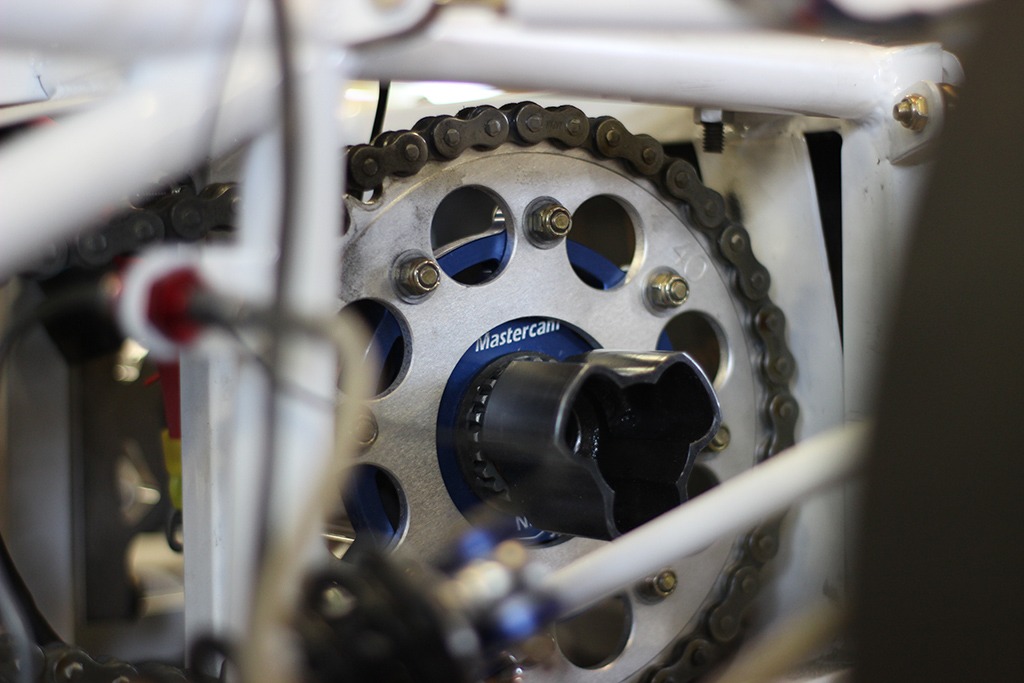
The 16-kilometer endurance competition tests the durability and longevity of each car. According to Palin, this is where teams stand to lose the most points due to fatigue. Factors including weight, manufacturability, cost, and structural capabilities must be considered in the car design. The 2018 UConn car demonstrated speed and stamina, accelerating from 0 to 60 miles per hour in less than 3 seconds. The estimated top speed was 80-plus miles per hour.
The long-standing relationship between UConn FSAE and Mastercam provides ongoing benefits to engineering students long after graduation. Several FSAE team members have interned with CNC Software, the developers of Mastercam, and gained valuable industry know-how.
Mastercam will continue to partner with the University of Connecticut and other educational institutions to help pave the way for aspiring engineers. Hands-on experiences, like the Formula SAE project, are key to applying classroom knowledge in a future workplace environment.
“You can learn the theoretical math behind engineering design, but when it comes to critical thinking, problem solving, and working with others, sometimes math and models do not represent reality,” said Palin. “Physically holding something that you have done the math on, analyzed, and designed, gives you a grip on what engineering can be in the real world.”
Customer Quote
“This is a huge help for us because writing G-code is an acquired skill. Mastercam makes it accessible for all of us.”
—Dylan Palin, Mechanical Engineering Student and President of Formula SAE Team, University of Connecticut, Storrs, Connecticut