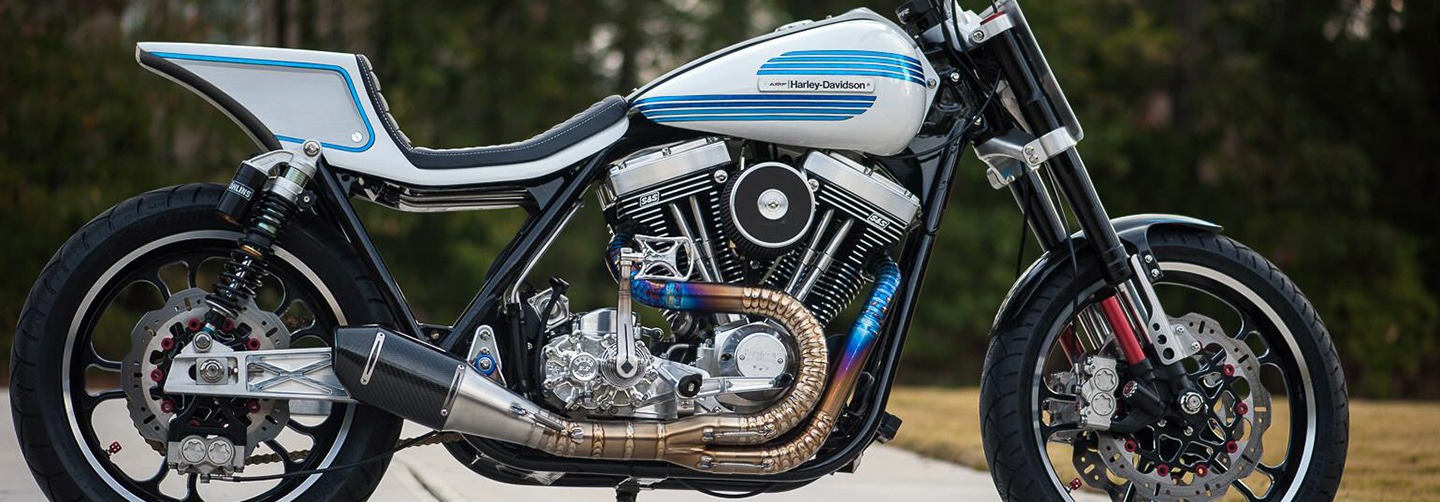
Revolution Speed’s High Productivity Keeps Them Ready for Any Design Challenge
Michael Kamalian started out like any other motorcycle enthusiast. But when his love of bikes turned into a growing business, he started gaining attention from major motorcycle designers, magazines, and even television shows. Revolution Speed, located in Marietta GA, can create anything from a dream bike to simply customizing a daily driver. The company likes to state: “If you can think it, we can make it.”
Quick Facts:
- Product Used: Mastercam Lathe
- Industry: Motorcycle (Transportation), Consumer
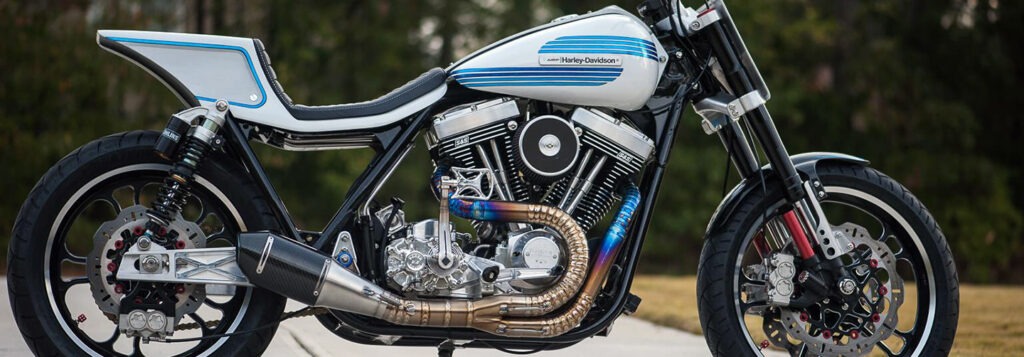
Project Details:
- The Challenge: Revolution Speed is a small shop that fits a big niche – high-end parts for motorcycles. Multiple customers order the company’s switch arms, among other parts, requiring the shop floor to be equipped to manufacture these components to exact specifications in a short amount of time.
- The Solution: Mastercam Lathe
- Benefits:
- Dynamic Motion toolpath strategies reduce cycle times for faster throughput.
- Eliminates the need to incrementally reduce step speeds.
- Provides older machines with new functionality.
Revolution Speed’s 3,500 square-foot machine shop is prepared to handle any project, from designing and constructing front-running custom motorcycles to creating aftermarket parts from the ground up. Kamalian decided to start making his own motorcycle parts, hiring lead machinist Justin Lowe, and purchasing his first CNC machine. Soon, he developed a part line for Harley-Davidson.
“We also started making a lot of custom parts for our own bikes around this time, which means we were making everything imaginable on a motorcycle,” said Lowe.
More manufacturers approached the company to make part lines for their brands. “We started making these parts over the years and became a Tier 1 manufacturer for Polaris making parts for Victory Motorcycles,” Lowe said. “Everything from floorboards, foot pegs, grips, and cosmetic covers all out of machined aluminum.”
Lowe’s experience with Mastercam CAD/CAM software made him a valuable asset. The shop has one seat of Mastercam Lathe and three CNC machines—two vertical mills, one with a 4th-axis rotary. They also have a twin-spindle Y-axis bar fed lathe.
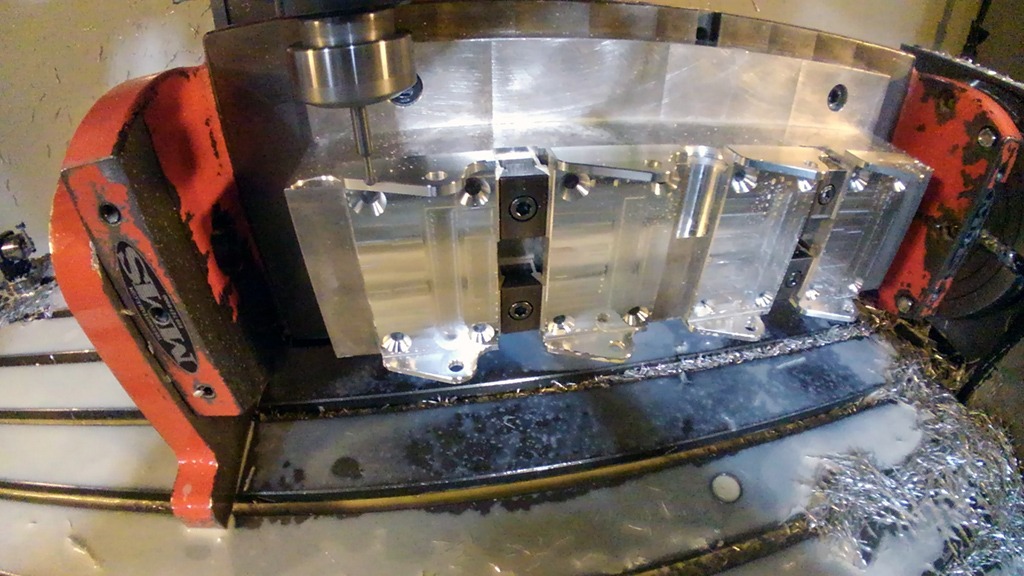
Lowe keeps things moving by running both mills at the same time to move the parts out faster and start the next project. High productivity is critical. In order to maximize time, machines are run at 12,000 to 15,000 RPM to achieve 200 to 500 in/min in aluminum with a 20 to 40 percent stepover.
Lowe pushes one of his vertical machining centers to its fullest potential by implementing Dynamic Motion technology. Dynamic Motion, or Dynamic Milling, uses proprietary algorithms programmed into the software to keep the tool constantly engaged with the material, allowing it to cut intricate geometries at higher speeds. “As we started doing the Dynamic toolpaths, the smaller vertical mill started catching up to the bigger machine a bit,” recalled Lowe. “We’ve been able to do a lot more jobs on this machine because I can get the cycle times down to where I need them to be.” According to Lowe, the machine peels off much more material, eliminating the need to step speeds down incrementally. “It’s helped make a machine that had almost become obsolete for us come back into being useful.”
The software has proven successful when programming certain parts. Multiple customers have asked for a swing arm, the rear suspension piece on a motorcycle machined from two or three pieces where everything bolts together like a puzzle with pins and bolts. The machining for this part entails multiple angles, different pockets, pockets on angles and radiused edges, which all must be smooth.
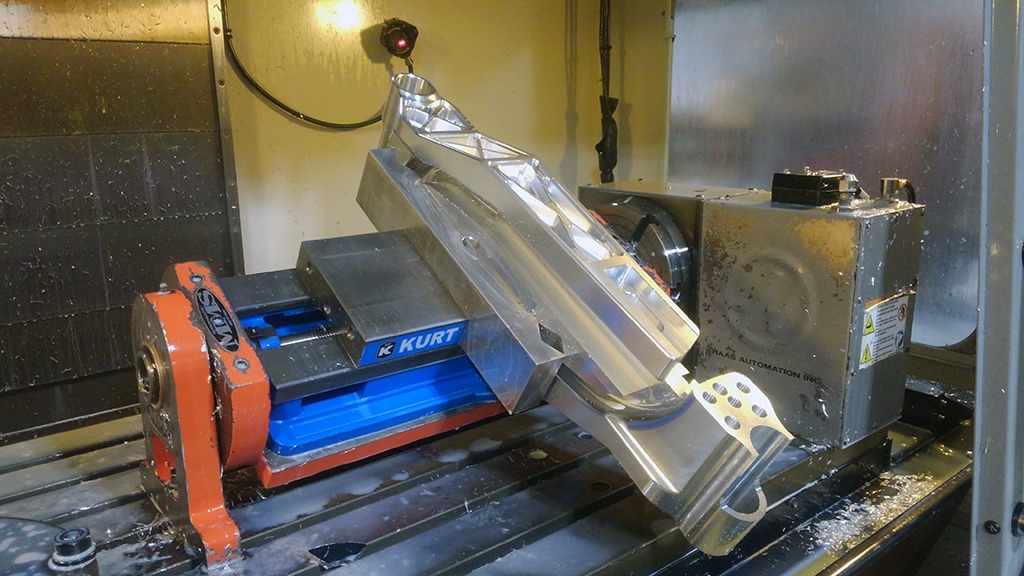
“For this 6061-aluminum piece, I use the Parallel toolpath to get a nice cosmetic surface,” Lowe said. “I have about nine operations where we’re doing different angles and I’ll nest the two halves together and machine them out and then cut them apart on the band saw once they are almost finished. I use both Flowline and Parallel toolpaths for these operations. I’ve also used a lot of the high-speed Dynamic toolpaths for roughing.”
They started with a 70 lb. block of aluminum, whittling it down to about 11 lbs. “With these parts, I used to program a ramp toolpath and have a chunk of aluminum to pull it out, leaving a portion of it solid so I wasn’t turning it all into chips. Now, I’ve gotten to where I use the high-speed toolpaths to turn it all into chips so I don’t have to stop and pull the tool out or worry about it getting caught in the chip auger.”
When he does need any assistance, Lowe reaches out to Brian Kadow, Senior Application Engineer, at Mastercam Reseller CAD/CAM Solutions, Inc. (Snellville, GA). Lowe has taken advantage of everything from their training classes to their tech support. “I’ll email Brian and he will get right on it and get me sorted out. I’ve known them for a very long time and have a personal relationship as well as professional relationship, which is great. They are always very helpful with whatever we need.”
Lowe is confident that using Mastercam has helped the productivity of their business over the years. He said, “I don’t know what I would do if I didn’t have good software to get these parts pushed out in a reasonable time.”
Lowe knows he can run his machines faster than many other shops, so he is already starting out with an advantage over competitors. By adding the software to the operation, he can optimize the entire project. He emphasized the importance of having the best equipment and software. “As far as the software, it’s really the cornerstone of being able to be productive.”
Customer Quote
“As far as the software, it’s really the cornerstone of being able to be productive. I could probably do more with good software and lesser machines.”
– Justin Lowe, Lead Machinist, Revolution Speed, on Mastercam
Reseller Quote
“I’ll email Brian Kadow and he will get right on it and get me sorted out. I’ve known them for a very long time and have a personal relationship as well as professional relationship, which is great. They are always very helpful with whatever we need.”
– Justin Lowe, Lead Machinist, Revolution Speed, on Mastercam Reseller CAD/CAM Solutions, Inc.