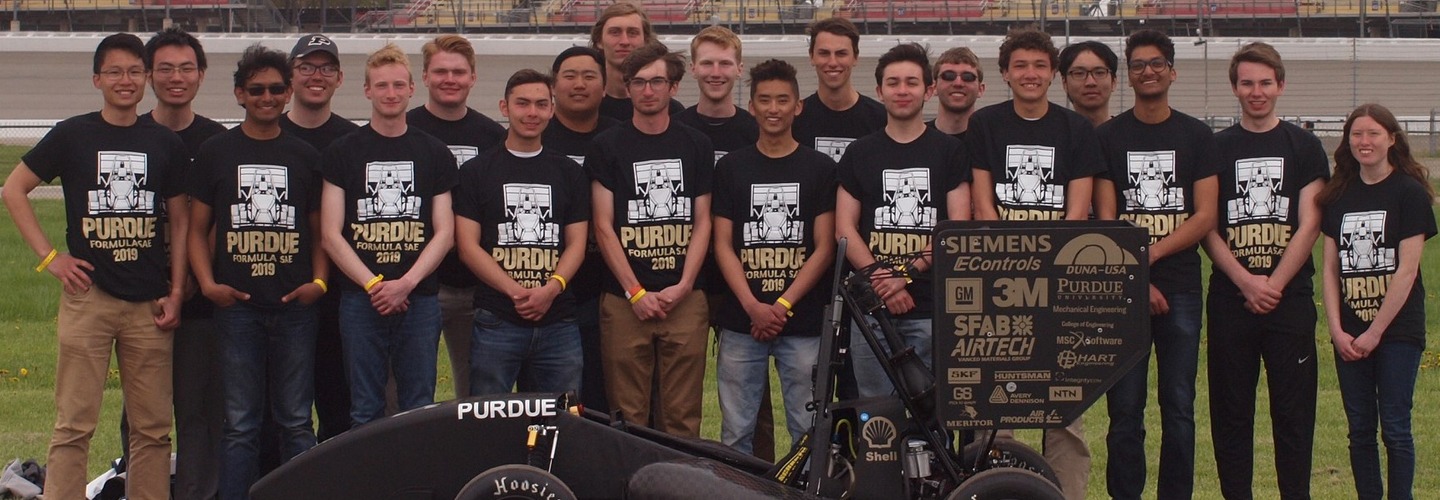
Purdue University Formula SAE Team Finds Ways to Win
Every year, the Purdue FSAE team designs and builds a prototype formula-style race car that will compete against others built by collegiate teams around the world. The only CAD/CAM software they trust to get the job done is Mastercam.
Quick Facts
- Product Used: Mill, Lathe, Dynamic Motion
- Industry: Education
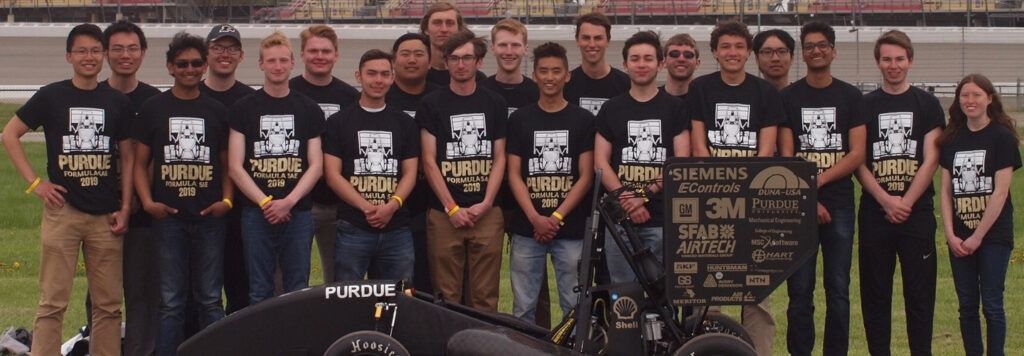
Project Details
- The Challenge: Designing and prototyping a small open wheel, open cockpit race car that has to excel in acceleration, maneuverability, and endurance while remaining safe and durable.
- The Solution: Free Mastercam for Formula SAE teams.
- Benefits:
- Verify and Backplot features highlight possible machining errors before they occur.
- Verify allows the customization of parts with specific tolerances, modeling of the finished part, and comparisons between the preview and the external STL model.
- Contour toolpaths use sophisticated calculations to remove material at high speeds.
- Dynamic OptiRough toolpaths quickly remove material without sacrificing precision or safety.
SAE International (formerly the Society of Automotive Engineers) has been challenging undergraduate college students to design and build small race cars since its first Formula SAE competition in 1981. The competition has grown over its almost 40 years of existence, and in North America alone there are three Formula SAE events a year—in Michigan, California, and Ontario, Canada—and there are over 20 competitions internationally.
While the design restrictions on the open wheel, open cockpit prototypes are relatively lenient, the overall goal is rigid: to create a high-performance race car that is durable enough to complete all the competition events and can be profitably marketed and easily reproduced. At the competition, the cars are put through various trials: acceleration over 75 meters, making continuous figure eights with 25 foot circle radius circles, braking and maneuvering around cones, and driving a 13.66 mile heat to test endurance and fuel economy.
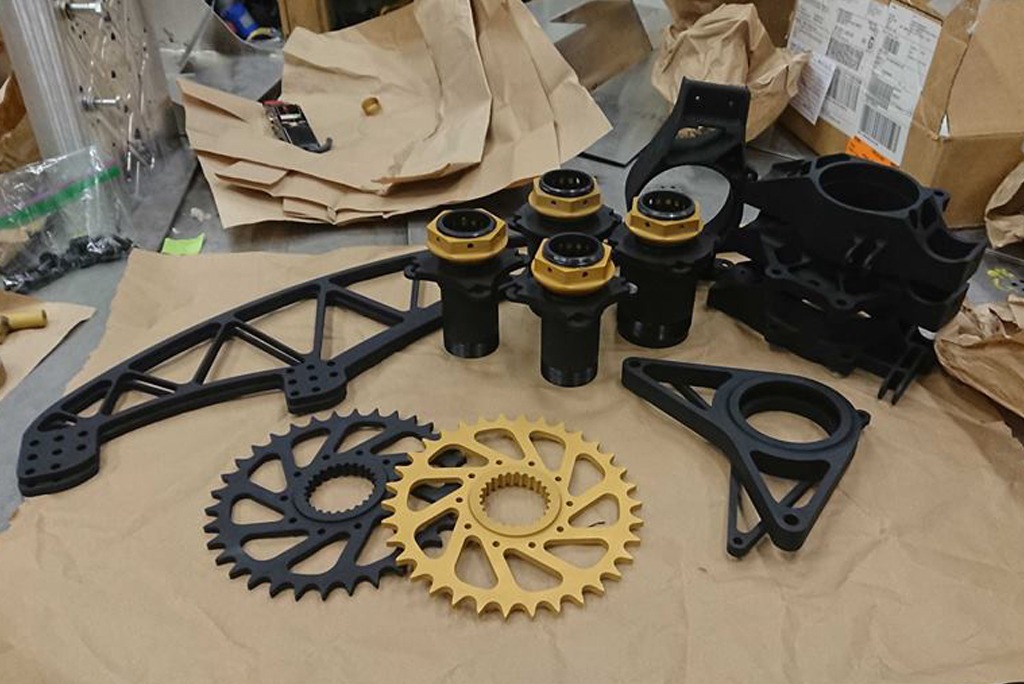
Purdue University’s Formula SAE team has been entering these competitions almost since the program commenced. Like every collegiate team, it is made up entirely of undergraduate students and relies solely on its members abilities, rather than depending on adults. ““We will basically make the entire car,” said Adam Dewey, Drivetrain Team Leader. “There are a few things that we don’t make, like the engine, the shocks, and the tires. Other than that we essentially make everything in-house.” Each sub-team, like the Drivetrain Team, has its own student leader.
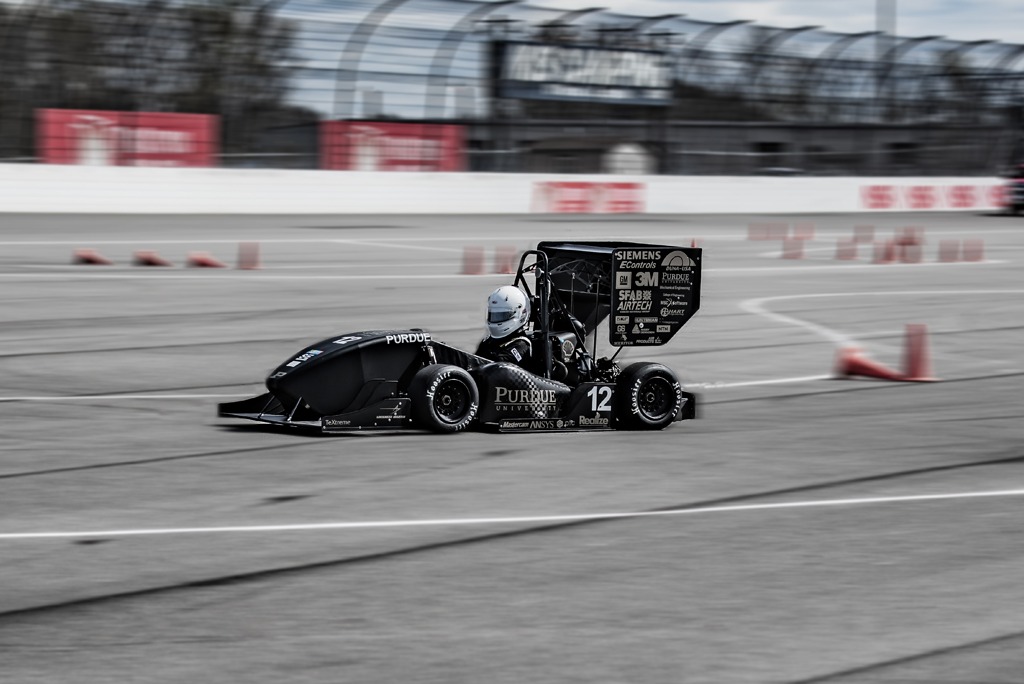
To stay competitive among other international teams with some of the brightest young engineers in the world, Purdue’s team must be sure of the precision and durability of all their car’s parts. The team uses Mastercam to make almost every machined component and model that their car requires.
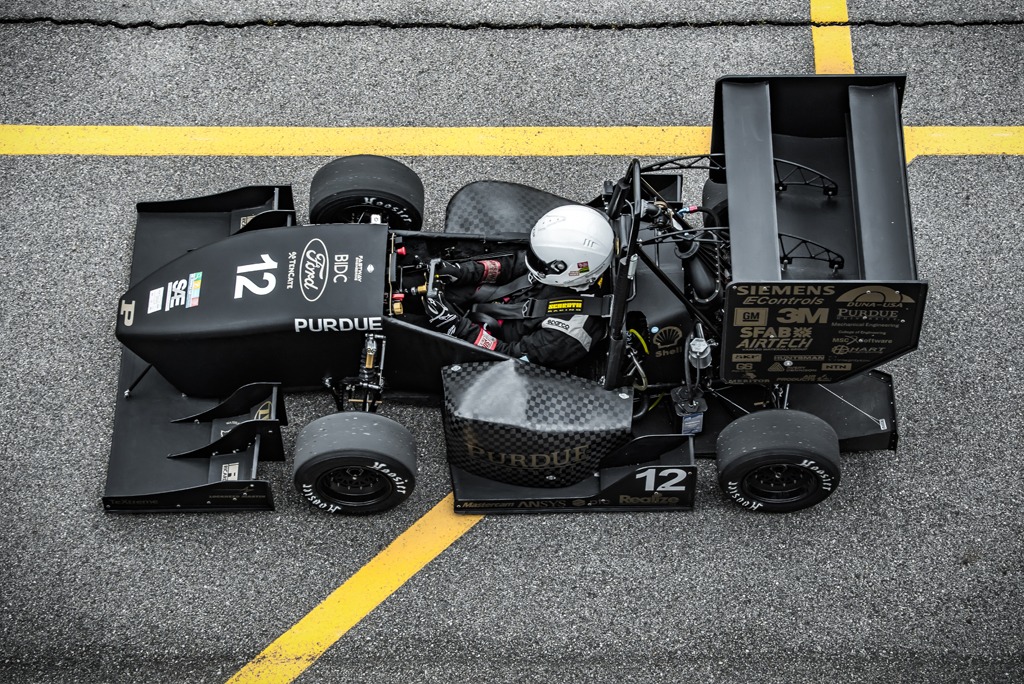
“I think the feature we find most beneficial is the simulation,” said Dewey, “We can model the toolpaths to see if there’s going to be any unexpected failures due to the tool maybe not being long enough or running into the tool holder. It also helps us estimate time and figure out what would be the best way to simplify the toolpath and maybe save some time on the machining.” The students run Verify to simulate the machining process and to check for possible collisions. Any problems that they find can be fixed quickly and easily from within the software.
Alex Roberts, Suspension Team Leader, agreed that the simulation abilities were vital to the machining of certain parts: “The drivetrain and suspension components, this was a tricky piece of geometry. The uprights connect a lot of different points of the suspension together, and they have to be perfect so we can fasten as much of the other components on the race car as possible.”
When the students do have questions, they can call up their local Mastercam Reseller ShopWare to have an experienced programmer troubleshoot their problem.
While every team member wants Purdue’s car to win at the Formula SAE Michigan event, each knows that they benefit from the experience whether or not they take home a trophy. After graduation, students from the team have no problems finding a career in manufacturing or in obtaining admittance to prestigious postgraduate programs around the world.
Chief Engineer Adam Christopherson shared, “I still would maintain that FSAE is the best program because of the experience that you get working with other students. The leadership that goes into it, the cooperation; there’s definitely a lot of non-technical things that are really crucial for success in any path that you want to take in the future. It teaches you how to go beyond the standard stuff in the classroom.”
Customer Quote
“I think the feature we find most beneficial is the simulation. We can model the toolpaths to see if there’s going to be any unexpected failures due to the tool maybe not being long enough or running into the tool holder. It also helps us estimate time and figure out what would be the best way to simplify the toolpath and maybe save some time on the machining.”
– Adam Dewey, Drivetrain Team Lead, Purdue University Formula SAE Team