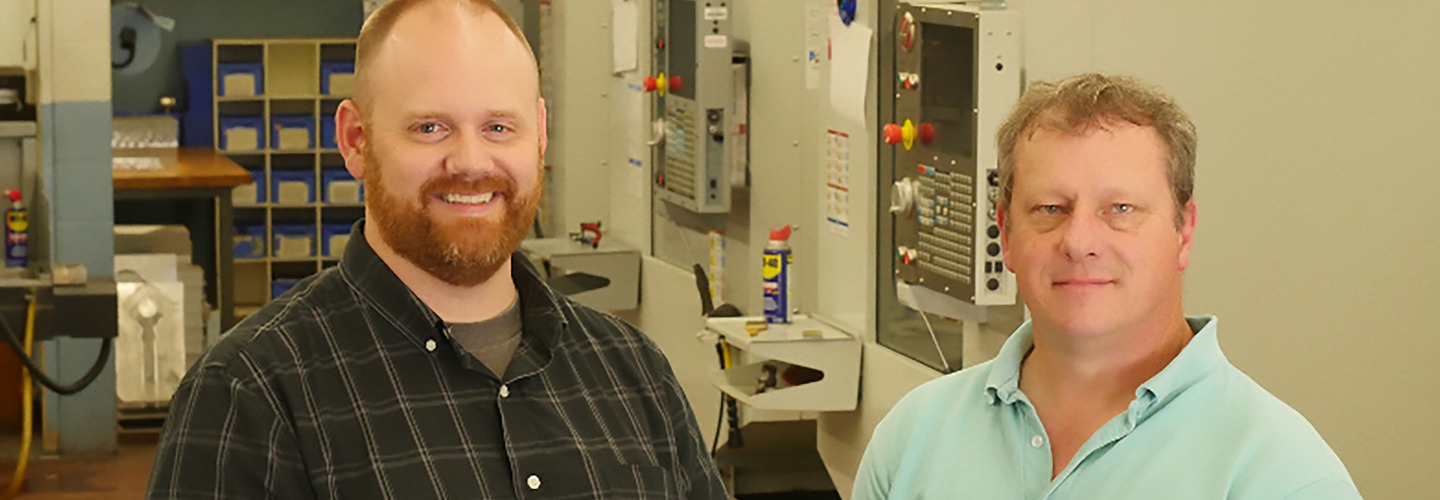
Reaching for the Sky at Platt Tech
America’s high school metalworking shop classes have been turning out some pretty impressive projects using CAD/CAM software and CNC machine tools, but when it comes to ‘out of this world’ impressions, few can measure up to the ‘heights’ reached by the students at Platt Technical High School in Milford, CT. Those ‘heights’ include the International Space Station, where some of Platt Tech’s work is helping several astronauts store their own projects.
Quick Facts
- Products Used: Mastercam
- Industry: Education, Aerospace
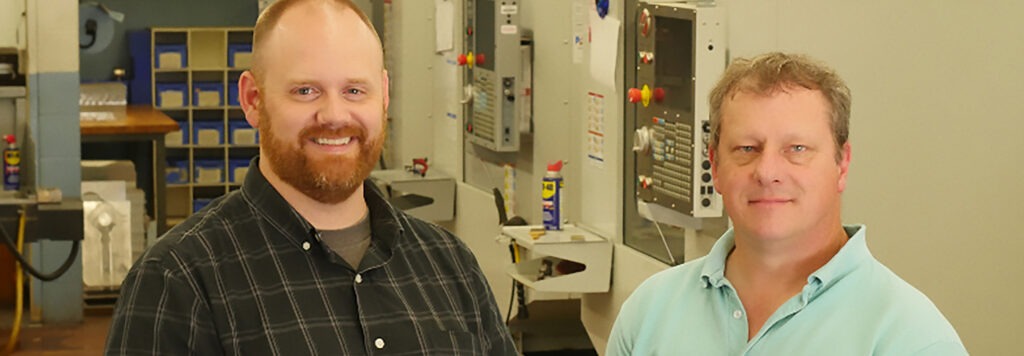
Project Details
- The Challenge: Bring students up to a proficiency level in automated machining where they can effectively produce precision components for industries ranging from medical to aerospace.
- The Solution: Mastercam CAD/CAM software
- Benefits:
- Easy for students to grasp
- Simplifies input of design work
- Stepped in complexity from 2D to 5-axis work
- Results in precise toolpaths for CNC machining
Department head David Tuttle and his fellow instructor, Greg Amende, have made the Precision Machining Technology program challenging and rewarding for over 90 students each year at Milford, Connecticut’s Platt Tech, who have chosen to become proficient in many facets of advanced manufacturing. These students have extensive facilities at their disposal, including a large machine shop with nearly forty milling machines and lathes, as well as hand tools, measuring equipment, and a generous CAD/CAM lab with over 30 seats of Mastercam software programming the work for more than a dozen CNC machines, and SOLIDWORKS® for doing the design work.
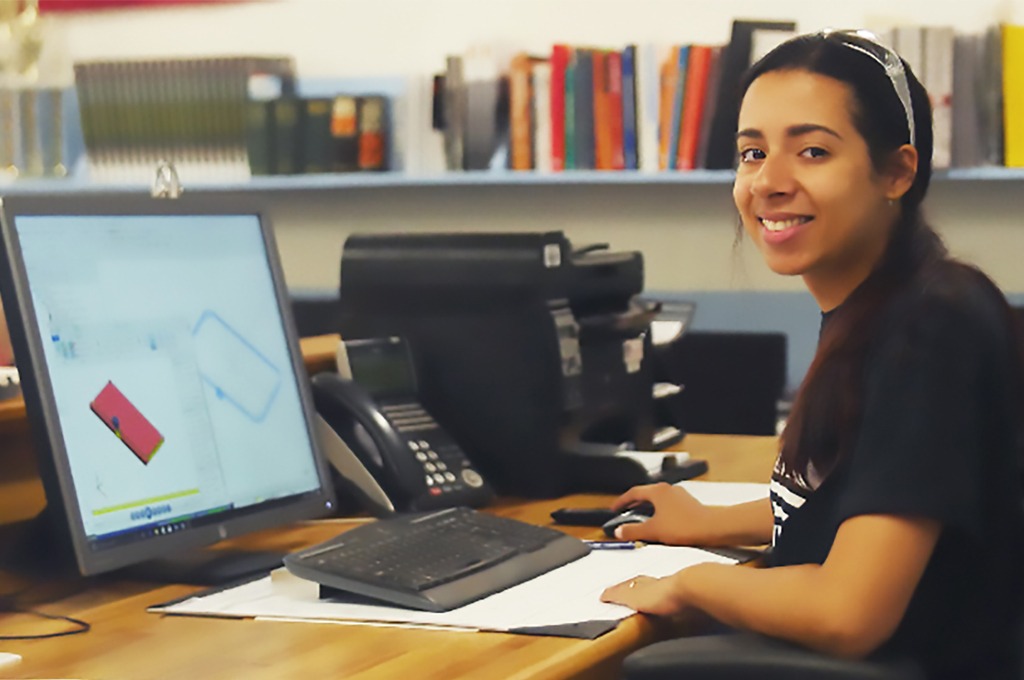
“Most of the industries in our region concentrate on defense, aerospace, medical, and tooling,” says Tuttle. “They all call for automated, high precision manufacturing capabilities and these are the companies that will be looking to hire our graduates. Over the past few years, we have been concentrating less on manual operations and more on CNC machining. Our curriculum has advanced to the point where we have introduced 5-axis machining and, as far as I know, we are one of the few high schools in the area that has a 5-axis machining center. Sixteen of our machines are now CNC, and we have a good mix of machines from different manufacturers so our students can get used to the different CNC controls they’ll find out in the industry.”
Tuttle uses early CNC programming lessons as a tool to strengthen their ability to read blueprints. In order for them to write a program, they need to study the blueprint in depth. “Mastercam is also used for problem solving,” he says. “If they have a question regarding the interpretation of a print, we’ll recreate the geometry in Mastercam, look for intersection points, and verify that the math is correct.”
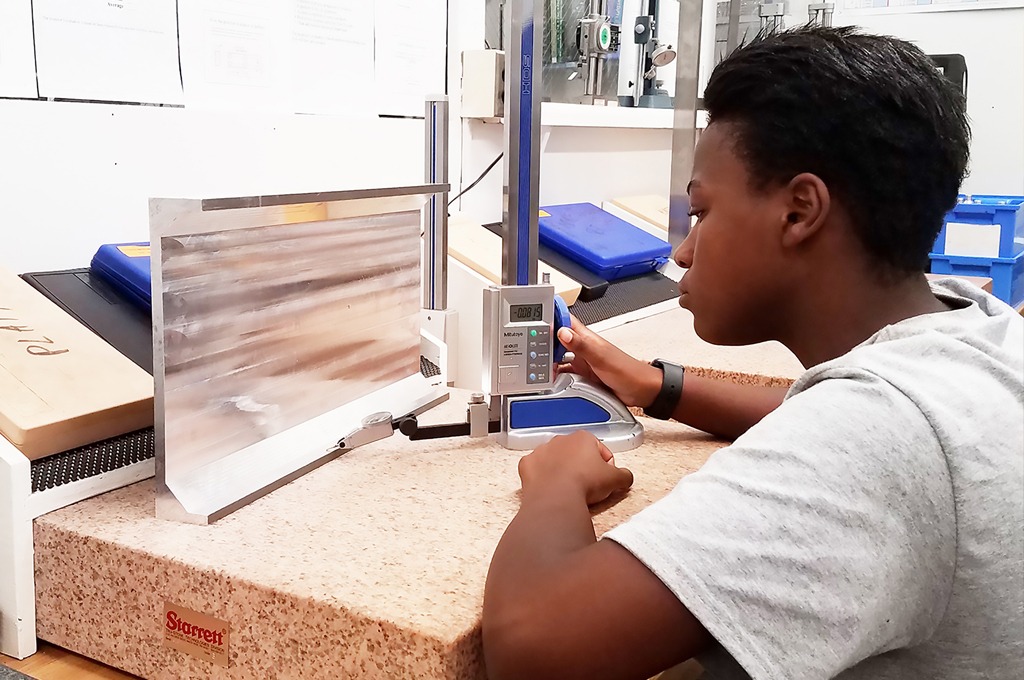
“By the time they reach their senior year,” says Tuttle, “they are getting into some pretty advanced operations such complex multi-tool jobs where they may have to set up ten tools on a machine and do some extensive programming operations in Mastercam that would require many tools for both turning and milling. Employers have been asking us for graduates who could walk up to a machine and set it up from scratch. That includes developing, designing, and making special tooling and fixtures to hold the parts.”
Not long ago, one of the school’s vendors saw a story about NASA working with high school students and thought Tuttle might be interested in a NASA program called HUNCH (High School Students United with NASA to Create Hardware). Tuttle sent off an email to NASA expressing interest. After some back and forth communication, a couple of representatives from NASA paid a visit to Platt Tech. “They told me that when it comes to shop facilities, we are the most heavily equipped high school they’ve ever seen,” says Tuttle. “The State of Connecticut has made a substantial investment in us and in the rest of the 17 technical schools in the state school system.”
To get them started with the HUNCH program, NASA shipped a 3,000-pound supply of aluminum to Platt Tech. “We make several of the larger parts that come together to fabricate storage lockers on the International Space Station that are used by the astronauts for a variety of experiments,” says Tuttle. “They look a lot like aluminum suitcases. The largest part starts out as a billet weighing about 60 pounds and after CNC machining, the final piece weighs about 18 ounces. The smaller parts for the final assembly are made at other schools in the HUNCH program. Our students program all of the toolpaths in Mastercam for machining to tolerances within 0.003 in. to 0.005 in. These are all precision components because, with parts coming together from different sources, accuracy cannot be taken for granted.”
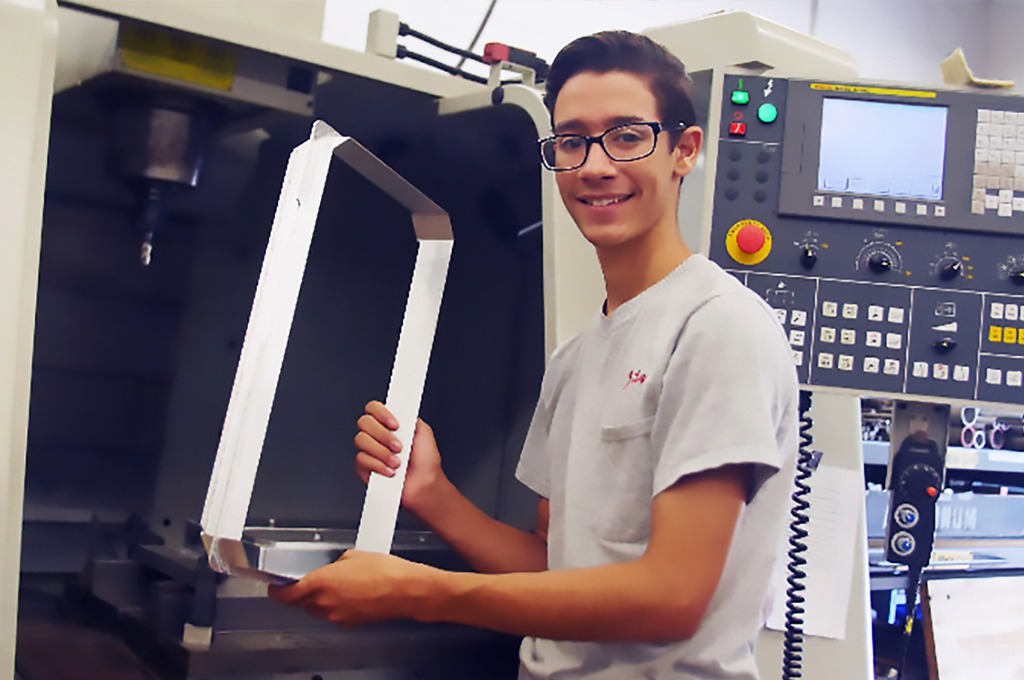
Whether it will be reaching out to space, or reaching for a nice paycheck, students graduating from the Precision Machining Technology program at Platt Technical High School are in the right orbit for success.
Customer Quote
“By the time they reach their senior year, they are getting into some pretty advanced operations such complex multi-tool jobs where they may have to set up ten tools on a machine and do some extensive programming operations in Mastercam that would require many tools for both turning and milling.”
– David Tuttle, Department Head, Platt Technical High School, Milford, CT