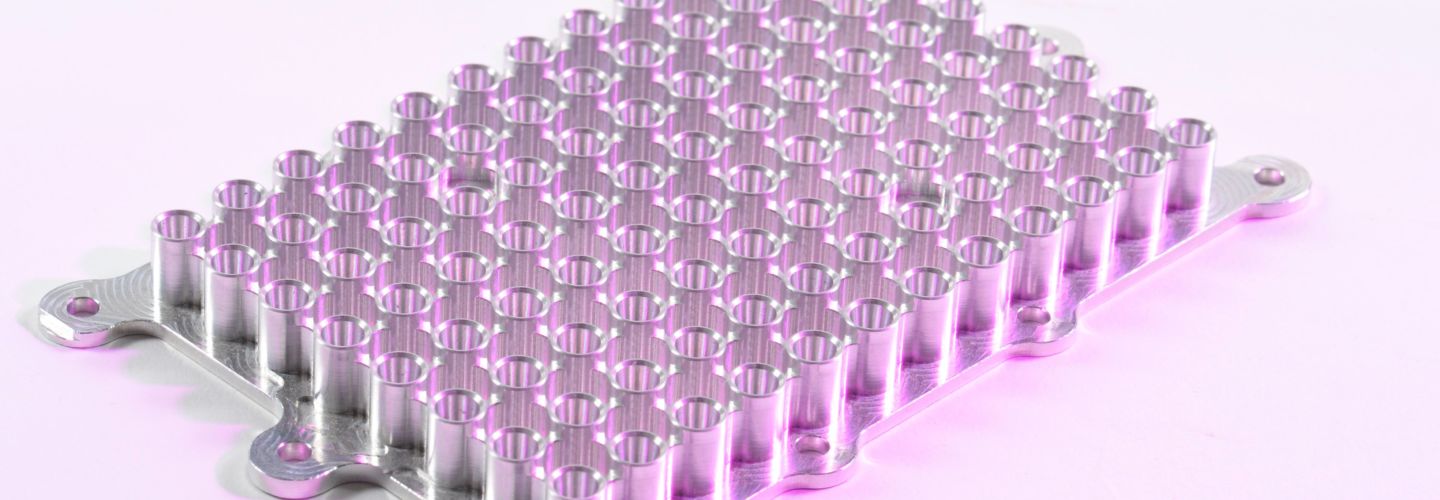
Design House Fabricates Innovative Prototypes with Mastercam
NOVO Engineering in Vista, California, provides the engineering behind a variety of medical devices, life science automation, digital imaging equipment, and commercial products from clients such as Medtronic, Synthetic Genomics, Hewlett-Packard, and TaylorMade. Its start-to-finish contract design service offerings include concept development, engineering, prototyping, fabrication, testing, and transition to manufacturing.
Quick Facts
- Product Used: Multiaxis, Mill, Lathe, Mastercam for SOLIDWORKS®
- Industry: Medical, Consumer Goods, Energy
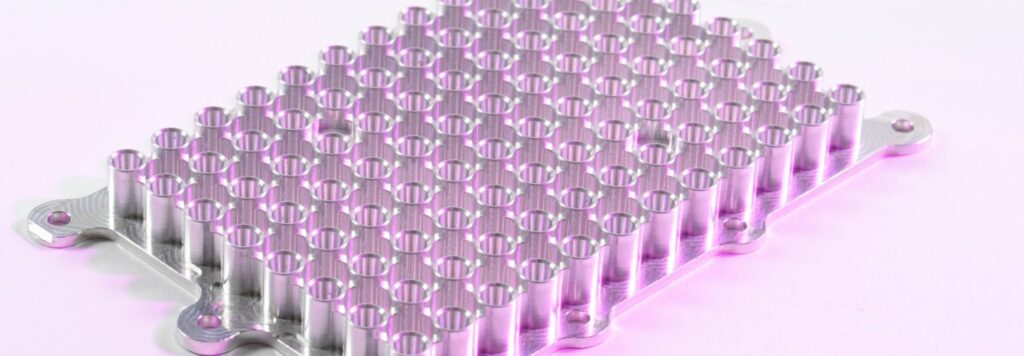
Project Details
- The Challenge: A focus on research and development requires that a team of engineers and machinists must take a methodical approach to tackling projects. Unusual parts with complex geometries and tight tolerances makes careful planning of the machining activity necessary to get it all right.
- The Solution: Multiaxis, Mill, Lathe, Mastercam for SOLIDWORKS®, Dynamic Motion
- Benefits:
- SOLIDWORKS® integration allows simple design changes to be made without extensive reprogramming.
- Proprietary algorithms allow tool to remain engaged in the material to achieve tight assembly tolerances.
- Many toolpath choices are available for applications where one toolpath can’t perform all necessary functions.
- Toolpaths can be programmed to machine tiny components of high-precision or unusual materials.
NOVO has 26,000 square feet of space in San Diego and 12,000 square feet in Minnesota devoted to design offices, testing labs, and a well-equipped prototype shop offering CNC turning and milling, FDM and PolyJet 3D printing technologies, and various other processes including surface grinding and welding. NOVO’s staff of 50-60 design engineers generate product designs using SOLIDWORKS® as their primary 3D MCAD platform. Completed designs are submitted electronically via the company’s network to the machine shop for prototyping and are directly imported to Mastercam® CAD/CAM software. Machinist Leo Castellon explains that each machinist in the shop notes the required tolerances and geometries, designs any workpiece fixtures, sets up the CNC machines, machines the part, inspects it, and then releases it for assembly and testing.
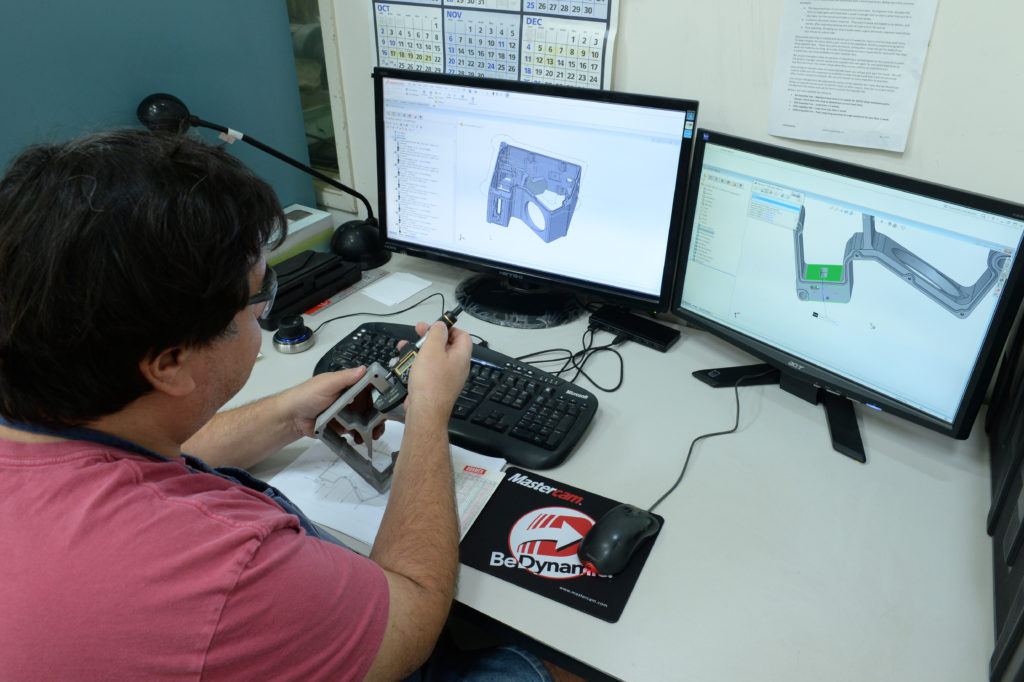
Each industry sector that NOVO is engaged in generates different challenges. Drug delivery systems, such as wearable injectors, routinely use tiny components; scientific instruments require high precision or unusual materials; and optical devices rely on tight assembly tolerances. Parts are designed in SOLIDWORKS and then seamlessly transferred to Mastercam. Design changes are simple to make and don’t trigger extensive reprogramming. “We do a lot of iterations of our parts, so if we make a change in SOLIDWORKS, we can quickly pick it up in Mastercam and regenerate the model to create the new geometry. Mastercam will pick up the right code,” said Castellon.
An example of this streamlined approach was a prototype part for a beam splitter. The material was a soft plastic that would be exposed to direct light, and a smooth surface was required to avoid image distortion. Through systematic trial and error, the engineers and machinists came up with a prototype that had a surface smooth enough to meet the optical requirement, yet strong enough to withstand the impact of a drop onto concrete.
The team went through six iterations of that design, and while it sounds time-consuming, NOVO’s President and Chief Technology Officer Dr. Rajan Ramaswamy was quick to point out how Mastercam supports rapid iteration. “Regardless of the improvements made in computer simulation tools, prototype and test iterations remain an essential part of the development process for the types of products that NOVO develops,” he said. This is especially important when developing medical products that require extensive FDA testing, often necessitating the fabrication of dozens of prototypes to support all the required verification and validation tests.
Many of the parts NOVO works on require tight tolerances, usually within 0.002”, on small features. For example, drilling 0.008” diameter holes through stainless steel or plastics. “With medical devices, you’re working with parts where the hole diameter is frequently well below 0.040”. Orders for some of the parts have us going through 0.120” of material with an 0.008” diameter hole,” said Ramaswamy.

Mastercam’s range of toolpath selections offer more options to machinists on challenging parts. “We use the Dynamic toolpaths because they’re so efficient in removing a large volume of material in a timely fashion,” said Castellon. This is the result of proprietary algorithms programmed into the software that intelligently detect changes in the geometry, allowing the tool to have greater engagement with the material, resulting in higher material removal rates.
The machinists also find Mastercam’s twelve plus surfacing toolpaths particularly useful because on complex parts, any one toolpath often can’t perform all the functions needed. For parts below 0.020”. thickness, the team does not use Dynamic toolpaths. “This is because the controller can’t keep up with the processing speeds and that’s a limitation with our CNC machine – it can’t process enough blocks per second to do it efficiently,” said Castellon. “The machine has to catch up. So, when I use the Dynamic toolpath at the smallest, I am using maybe a 0.0625” diameter end mill. Anything less and there are problems with not being able to process the code fast enough to keep up.” Instead, Castellon uses 3D legacy toolpaths for the smaller parts. When machining plastic, the Dynamic toolpaths have often taken the machining time down from 10 minutes to 30 seconds.

The machinists use the tool library to create their own tools. For one project, they needed a 4-inch diameter end mill and created it easily in the tool library, imported the tool to ensure that all clearances were right, and found that it worked well in that application. Although the company rarely does repeat jobs, if an application is akin to something they have done before, they locate a similar tool in the library, regenerate the geometry, and Mastercam will pick it up. “This is such a fast-paced environment. When we bring in a solid model, we need to have a finished part the next day. It has to be really efficient and Mastercam helps us with that,” said Castellon.
Castellon has found the Mastercam Forum to be invaluable when seeking advice on how to work with unconventional specifications. “There is such a huge user base, and they are cooperative as far as sharing information,” he said. When even the most unusual of parts comes through, he can find advice from the Mastercam user community. “It’s hard to find other software or CAD/CAM program companies that have such a large user base with sharable knowledge,” said Castellon who also noted that he talks to the software’s developers on the forum.