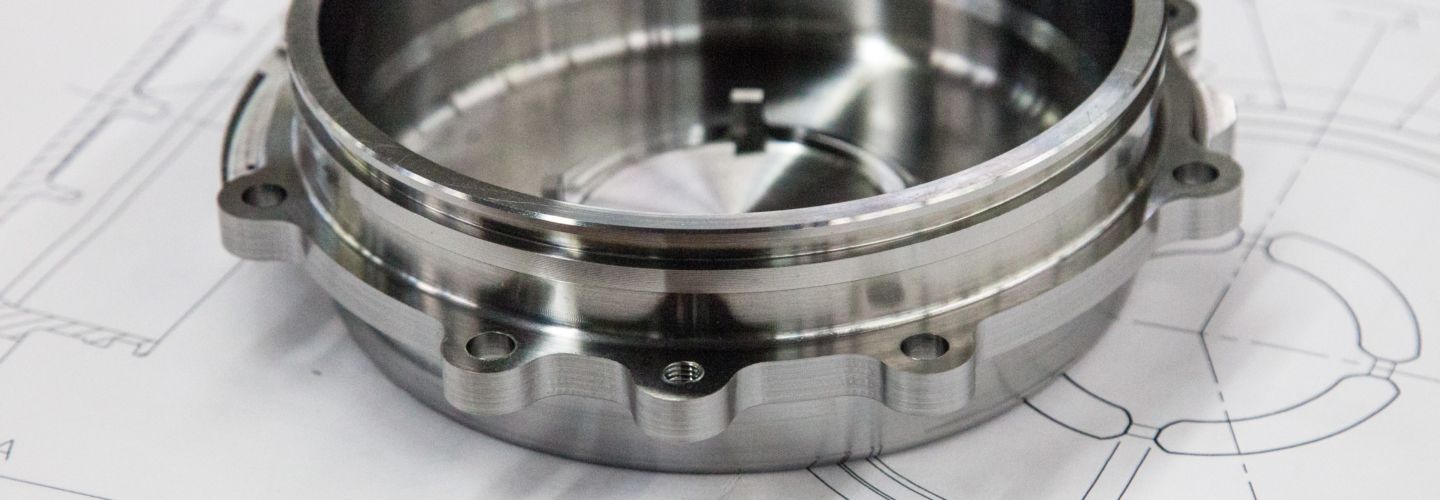
Verifying the Impossible
The folks at Mallory Industries took a calculated risk a few years ago when they decided to invest heavily in multiple CNC machining centers and a wire EDM machine. Their ability to verify the elimination or reduction of clashing, tool breakage, and damage to the machines themselves prior to running the job played a significant role in their decision. Since then, they have been able to manufacture large, more complex parts for the aerospace industry and take on jobs never before imaginable.
Quick Facts
- Product Used: Mill, Lathe, Multiaxis, Dynamic
- Industry: Aerospace
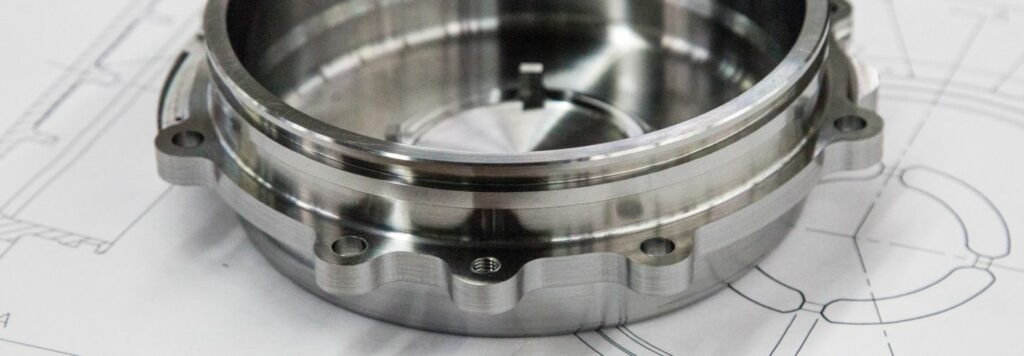
Project Details
- The Challenge: Fulfill the demands of aerospace customers and grow the business by investing in powerful machining centers but at the same time eliminating or minimizing additional costs associated with tool wear and breakage, machine breakdowns, and errors with final parts.
- The Solution: Mastercam, the most widely used CNC software for CAD/CAM operations.
- Benefits:
- Easy to learn
- Dynamic toolpaths allow machines to run at optimal speeds for faster throughput
- Ability to verify toolpaths, machine speeds, collision potential, and part tolerances prior to machining
Founded in 1956, Mallory Industries, Inc. (Farmington, CT) specializes in grinding, high-speed vertical milling, CNC turning, and wire EDM machining of stainless steel, aluminum, titanium, and high-temperature alloys. Its 22,000 square foot shop has two sides to its business: Aerospace and Commercial. Over the past few years, the company has invested heavily in its machinery, adding three high-speed vertical mills with full rotary tables that can handle parts up to 20-in. diameter, a twin-pallet horizontal machining center, two multiaxis lathes, and a wire EDM machine. The folks at Mallory looked at it as a calculated risk because they could verify a part’s ability to be machined, prior to it actually being put through to the machine due to the Verify utility of its CAD/CAM software, Mastercam®. “When we quote jobs, we look at how we’re going to machine it, the process to do so, and then program it to go through these machines,” said Operations Manager Ken Fogler. Whether the part goes through the multiaxis lathe area of the shop (there are two which combine milling and turning), the 3- or 4-axis machining center area, or the 2-axis cell area, depends on the constraints of the machine itself. Jobs are modeled in SOLIDWORKS® and imported into Mastercam, where the wireframe geometry is created. “We verify the final program in Mastercam so that we’ll see exactly what will be produced with no surprises. The Verify feature allows us to detect any discrepancies, measure and analyze, as well as provide collision detection. With the cost of today’s equipment, I wouldn’t do it any other way. Once we know it all looks good on the computer, we’ll post it and send it out to the floor,” said Fogler.
Fogler and his team use Mastercam 2017, which not only includes the software’s Dynamic Motion technology, but also radial chipping which they were doing manually on the side via spreadsheet. The team programs the part and then cuts it on the screen in one form via two modules – one for programming and one for verifying that the toolpaths will, in fact, work in real life. “It helps us on our end to know that what we see on the computer, we will see out on the floor so there are no mysteries,” said Fogler. “We use that daily.”
One of their favorite jobs involved the dashboard frame for the Blackhawk helicopter, an exceptionally large piece that was machined in several steps. “We had a couple of programmers working on it,” said Fogler, “and, because it was so massive, we worked on one side and then the other, creating a program, verifying it, using the Dynamic toolpaths.”
Fogler noted that while the process was tedious, it was flawless and was not possible without the Verify and Dynamic Motion toolpaths available within the software. The part was machined using one 3-axis machine. They started with a 6’x2’x1” thick piece of aluminum weighing 275 lbs, and implemented the Dynamic toolpaths for the very first time. The toolpaths removed the material quickly, due to proprietary algorithms in the software that intelligently sense changes in the material, allowing the tool to remain in constant contact with the material with little or no stepovers. Because the tool is constantly engaged with the material, there are fewer tool breakages as well. The team was able to whittle that piece down to 9 lbs. “You don’t have to go old school. With stock recognition, Mastercam knows where the material is, which allows the software to make good decisions relative to toolpaths. It certainly makes it easier,” said Fogler.
The team was also able to accept jobs they otherwise would never have considered because the risks to the machines were minimized. “Because this is a very capital-intense business, you have to take care of the equipment by managing the software. So, the more we know about the software, the better our results are on the floor,” Fogler said. They rely on their Mastercam Reseller, MACDAC Engineering, Inc. (Somers, CT), for training and support. He finds MACDAC’s expertise especially helpful when working with 3D models.
Mallory uses the same carbide end mills, carbide drills, and other carbide tooling they have always used because the tools simply do not break. By taking advantage of the productivity utilities in their CAD/CAM software, Mallory continues to save costs on consumable items, scrap, and even human resources, while realizing better throughputs and cycle times.
“At times, we have complex projects to program and that’s where the software comes in. We’ll model it, program it, and then verify it to determine whether it’s really what we want before we take that next step and put it out to production.”