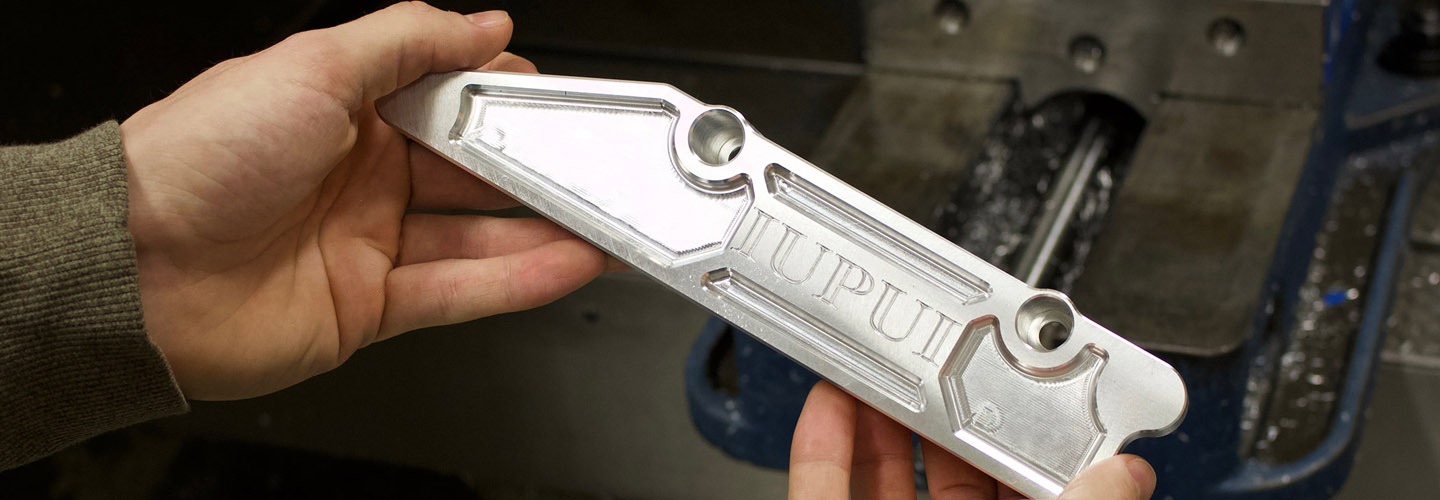
Students Excel in Mechanical Engineering Technology Program
The School of Engineering and Technology, located at a campus shared by Indiana University and Purdue University in Indianapolis (IUPUI), includes a prestigious program of Mechanical Engineering Technology. The students who elect to study mechanical engineering technology, as opposed to mechanical engineering, are exposed to more of what happens on the manufacturing floor, beyond design disciplines.
Quick Facts
- Product Used: Educational Suite, Mastercam for SOLIDWORKS, Mill, Dynamic Motion
- Industry: Education, Transportation
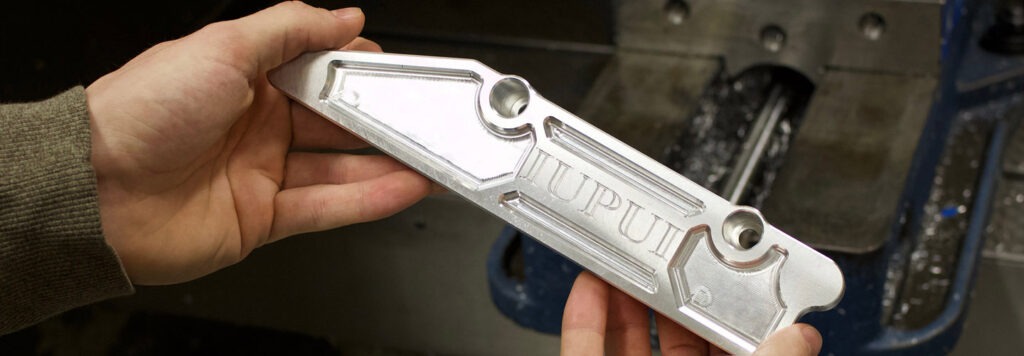
Project Details
- The Challenge: Encourage students to engage in the actual practice of CNC manufacturing operations through increasingly complex CAD/CAM applications.
- The Solution: Mastercam, the most widely used CNC software for CAD/CAM operations.
- Benefits:
- Easy to teach, easy to learn
- Clear, step-by-step tool path process
- Dynamic Milling feature optimizes cutting time
- Students become familiar with real-world operations
Until recently, the Mechanical Engineering Technology program at IUPUI used little online material and concentrated on a traditional curriculum of classroom lectures and practical projects. When it came to CAM software, they taught Mastercam for SOLIDWORKS® as an add-in to the program.
“The direction we wanted to go in,” said Ed Herger, Program Lecturer, “was to provide more CAM experience as well as online and external certificate opportunities. This meant concentrating on Mastercam and the online benefits of Mastercam University, which would give our students the option of receiving a proficiency certificate in addition to a Bachelor of Science degree, with online lessons both in our lab and on the students’ own laptops and home computers. I’ll take two or three units from Mastercam University and have them go through those units on their own and then give them an assignment based on the CAM operations or features shown in those materials.
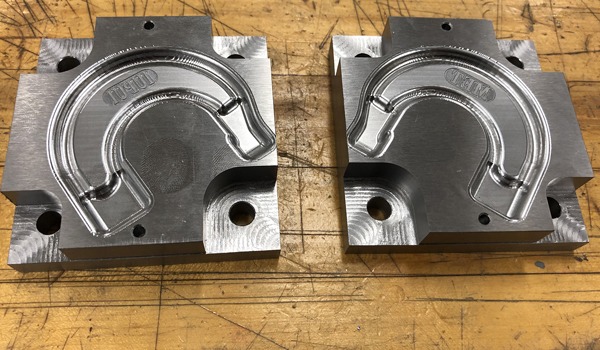
I believe they’ve been pretty successful completing the Mastercam University assignments and my own assignments. In my class, students simply follow the online course from start to finish. When it comes to projects, my overall approach is to give them a more all-encompassing type of project as opposed to several small, specific exercises that have little in the way of practical application.
For example, I recently had them reverse-engineer a micrometer, a precision measuring device. They designed several programs for tooling to make parts for the micrometer. They then figured out how to use some advanced features of Mastercam to program the machine operations in our computer lab. I guess what I’m saying is that I try to give them a project with real-world application, and I try not to give them too many hard guidelines on how to do it. They also learn more effectively when they try to figure things out for themselves before I jump in.”
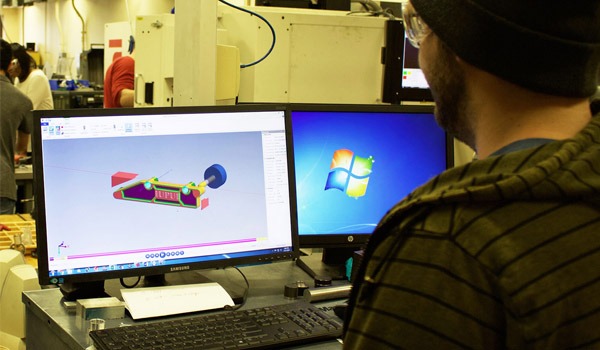
Mr. Herger said that he uses quite a few features of Mastercam to get the most out of their CNC machines’ capabilities, pointing to the benefits of Dynamic Milling. He is especially enthusiastic when it comes to a big capstone project for his students.
“Because we’re in Indianapolis.” he said, “it’s only natural that we’re in touch with the automotive racing scene and even have our own motor sports program. The Indianapolis Motor Speedway has a demonstration transmission from an Indy car on display at their museum, and it’s cut away in a number of places so you can see what’s going on inside. Up until last fall it was a static display. We were fortunate to get the project from the museum where we would animate and automate the transmission so that it would be an interactive display that would rotate at a slow speed and visitors would be able to shift it with a model of the steering wheel from the same car. All of the brackets that connected the small electric motor to turn the transmission, as well as many smaller components and a linear actuator to actually shift the linkage, were machined using Mastercam.”
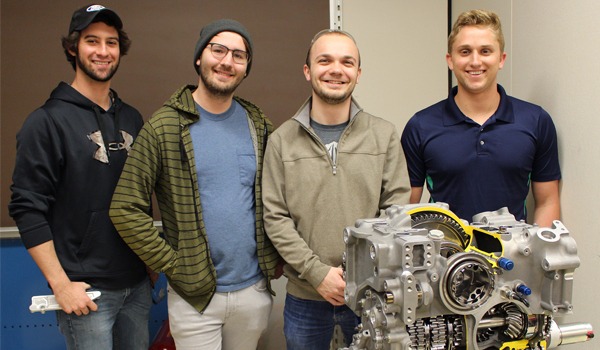
Using the Dynamic Milling feature of Mastercam, students are able to push machines pretty fast. “For example, when it came to the brackets,” Mr. Herger said. “We started off with a 2” x 2” x 2” block of aluminum for a component that wound up as a 5/8” thick plate with a couple of cylindrical bosses on the back that extended out somewhere between ½” and ¾”, depending on location. These bosses allowed the plate to be bolted up to the transmission while still giving it some standoff clearance.
Using the Dynamic Milling program, we used a ½” endmill and full depth of cut to get rid of most of the material. Essentially, we were removing all the material down to about an inch-and-a-quarter with the exception of the three cylindrical bosses. We used a ½” ball endmill to leave a fillet at the bottom of the bosses. We let Mastercam come up with the tool paths and Dynamic Milling optimized cutting operations.
The Verify simulation feature of Mastercam is something we use for every single program right before we run it. We go back through all the different steps of each program that need to be checked out to make sure there’s no potential issue sitting there. I’d have to say, this capstone project, as well as many other projects, have been fantastic for our students and our program.”
CUSTOMER QUOTE
“The direction we wanted to go in, was to provide more CAM experience as well as online and external certificate opportunities. This meant concentrating on Mastercam and the online benefits of Mastercam University…”
Ed Herger, Program Lecturer, Mechanical Engineering Technology Program, IUPUI