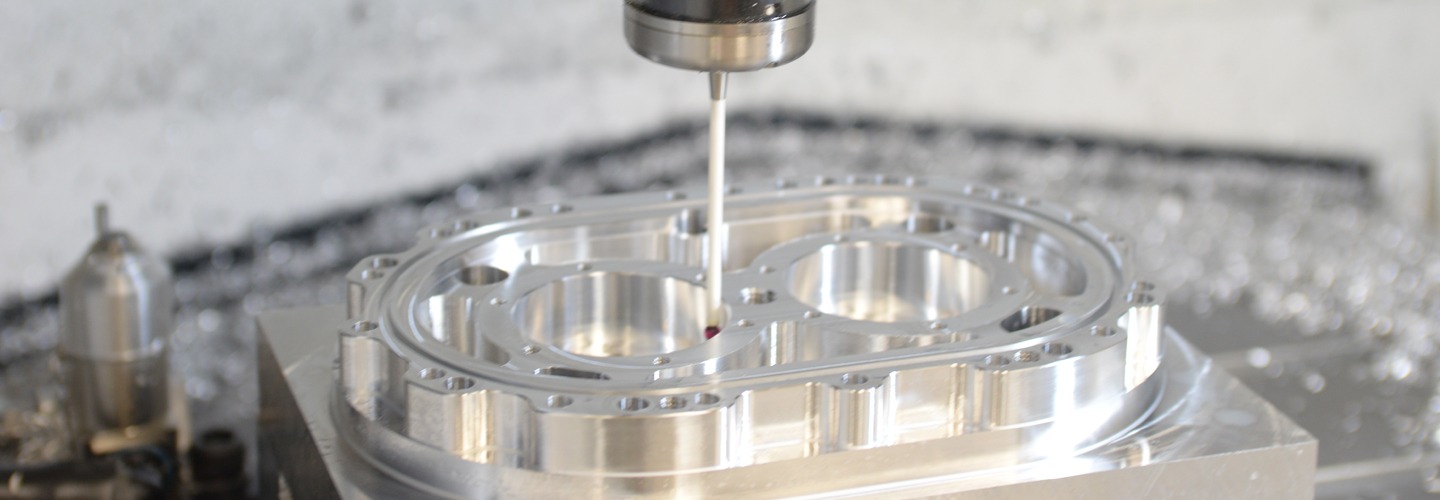
Advanced Machining Technology Gives Don Schumacher Racing an Edge
Don Schumacher Racing maintains their competitive edge by manufacturing almost any racecar part in-house. To do this, they need to be able to machine parts that will hold up against the stress of high-speed racing without adding too much weight to the car.
Quick Facts:
Product Used: Mill, Multiaxis, Lathe
Industry: Transportation
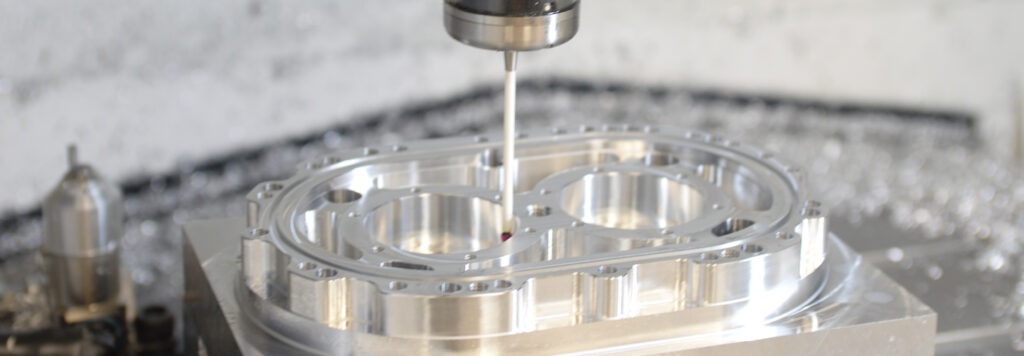
Project Details:
- The Challenge: Designing and manufacturing automotive parts with extremely tight tolerances to be durable yet lightweight.
- The Solution: CAD/CAM support from Mastercam Resellers and the advanced machining technology of Mastercam.
- Benefits:
- Expert advice and consulting from certified Resellers with industry experience.
- Tool Libraries house valuable information on cutting tools and solid models to reduce programming time and ensure accuracy.
- Dynamic Motion Technology dramatically reduces roughing cycles by removing large quantities of material.
- Advanced Simulation features detect possible machining errors before they occur.
Don Schumacher Racing is involved in every step of the automotive racing industry, from the design shop to the racetrack. The company tries to manufacture as many of their racing parts in-house as possible. “We manufacture engine components, chassis components, exhaust, widgets, and everything down to nuts and bolts,” said Scott Cutler, Senior Manufacturing Engineer.

DSR has found manufacturing success in a combination of advanced machines, expert technical support, and powerful software. The DSR shop holds 22 CNC machines, which include horizontal 4-axis milling centers, 5-axis milling centers, 7-axis mill-turn machines, 3-axis lathes, vertical milling centers, and a Swiss screw machine. A shop of this caliber requires technical support of the same quality. That’s why DSR relies on their official Mastercam Reseller, ShopWare, Inc. when they run into issues.
ShopWare not only introduced DSR to the power of Mastercam to make to company’s manufacturing goals possible, they provide continuing support in all aspects of CNC machining. DSR also receives assistance from Mastercam’s extensive support network, including applications engineers in the Mastercam Manufacturing Lab.
Cutler shared, “Chris Kozell and Chad Chmura, they’re great. Chris has helped us with post issues and with working through the bugs of a new option on one of our machines. Chad helps us with training, shows us how to properly use them, and physically helps us choose between the many different toolpaths that Mastercam offers. If we have a really tough, complex part here that maybe nobody in the world’s ever made before, if we get stumped, we have numerous people we can reach out to and get support and move forward.”
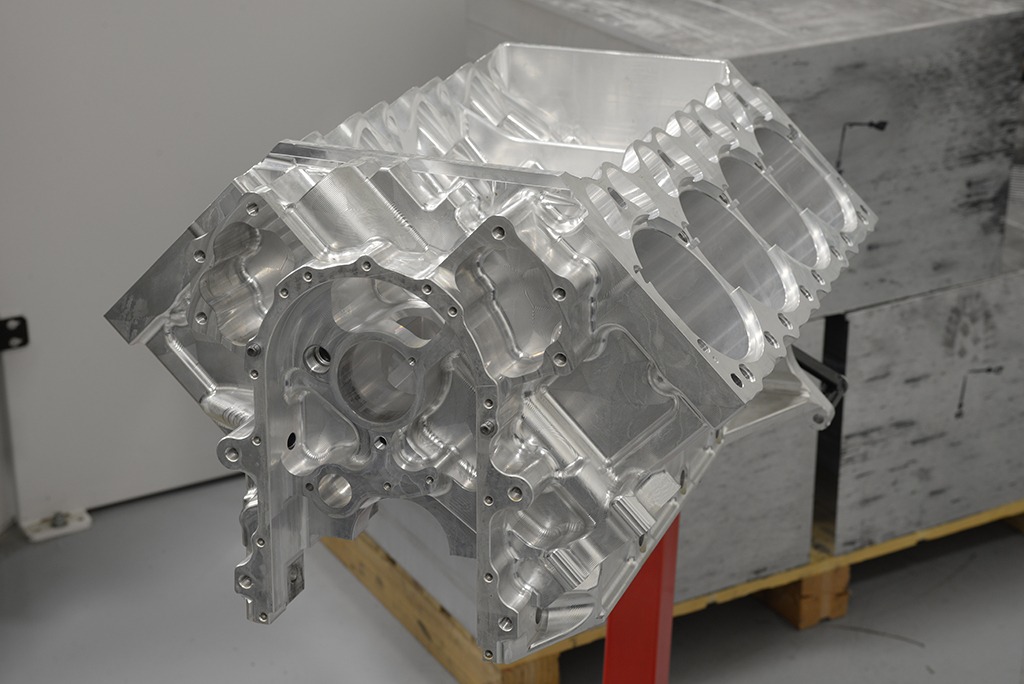
One such issue that DSR faces is that of part durability. “We need to make the parts light, but at the same time, we need to make the parts strong and durable. You know, these cars are going at high rates of speed, and a lot of things are happening, so safety’s a big concern. In top-fuel racing, we’re in the most extreme conditions. We make the most horsepower in any form of racing, and we run for the shortest amount of time; we’re basically building a controlled bomb,” Cutler explained.
When DSR sends out their racing team, they need to be sure that they can come as close to guaranteeing their safety as possible. “Mass will always help you in durability, but it doesn’t help you in increasing speed or reducing overall weight. It’s one of the hardest things to do because we can’t use heavy metals like we should, so we have to use a weaker metal but somehow we have to make it hang on to the most power.”
DSR often uses aluminum and mild steel. Each part is contoured, which adds ribbing to areas that will be under higher stress while removing excess weight from other spots. To strike the perfect balance between safety and speed, DSR’s design and modeling process need to be extremely precise.
OptiRough uses Dynamic Motion Technology’s proprietary algorithms to optimize the cutting path and motion of a tool. DSR can remove large quantities of stock material in a very short amount of time, reducing the overall cycle time and freeing up time that can be spent in other areas.
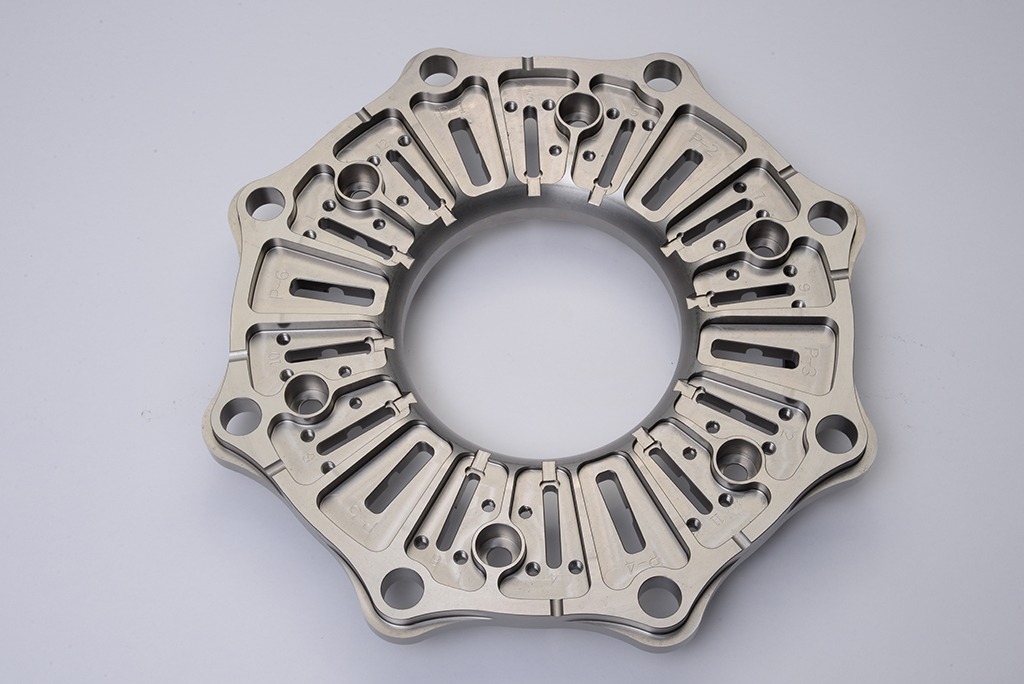
Parts often start as 800-pound blocks of stock material. “In order to remove that much material on a part at a good rate, we take advantage of Mastercam’s Dynamic Motion OptiRoughing. With the combination of the software and our range of Sandvik Coromant tools, combined with our Okuma machining centers, we’re able to remove material at feed rates of 300-inches-per-minute with full depths of cut at about 3/8 of an inch on average,” said Cutler.
The average tolerance of a part in the DSR shop is plus or minus two and one half thousandths, with many parts having much tighter tolerances. Achieving these tolerances requires reliable information and advanced simulation.
“We have a Tool Library created for basically each category of machine. We constantly import Sandvik’s tooling models. It helps us in simulation, and we can look at the actual tool holder to look for interference there and not just on the cutter.”
Cutler then turns to the Compare feature within the Simulation tool to compare solid models, visualize the accuracy of the cuts, and check for any collisions. “It’s given us a lot more flexibility in working with solids when we get into a lot of our complex parts because everything is 3D. We can now go and write in through the software and manipulate it to get us the result we need.”
Customer Quote
“In order to remove that much material on a part at a good rate, we take advantage of the Mastercam’s Dynamic Motion OptiRoughing. With the combination of the software and our range of Sandvik Coromant tools, combined with our Okuma machining centers, we’re able to remove material at feed rates of 300-inches-per-minute with full depths of cut at about 3/8 of an inch on average.”
—Scott Cutler, Senior Manufacturing Engineer at Don Schumacher Racing