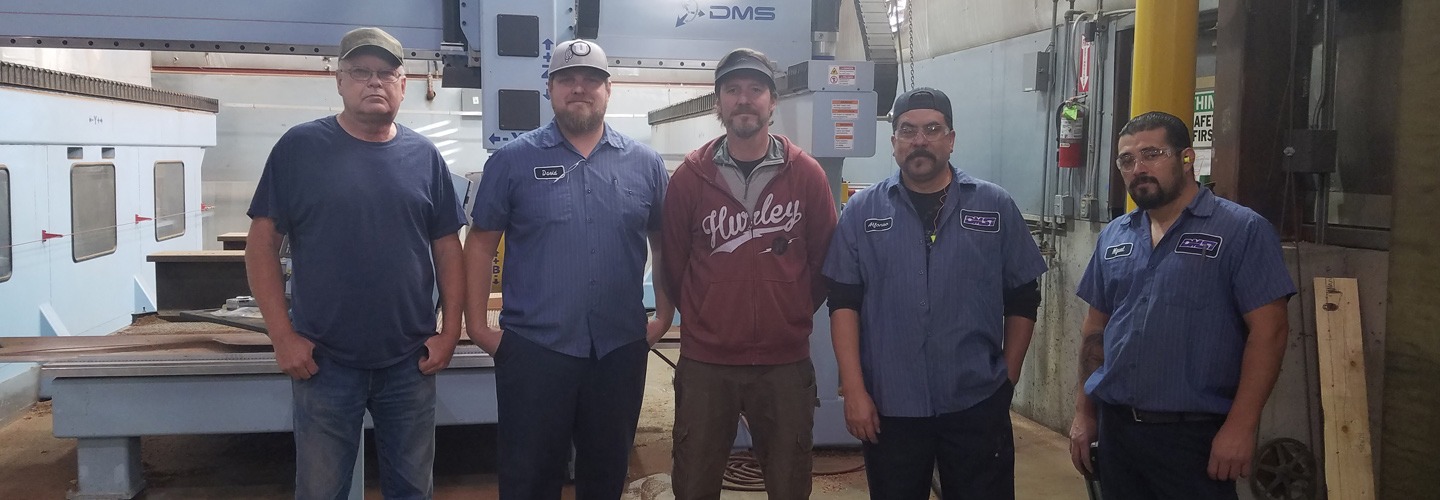
Job Shop Empowered by 5-Axis Waterjet, Mastercam, and a Robotic Arm
By combining the flexibility provided by the addition of sixth and seventh axes with a router, Diversified Metals Services, Inc. (DMSI) in Salt Lake City, Utah has been able to expand its water jet and router cutting capabilities to accommodate a wide range of sizes and materials, cutting faster than ever before, and saving significant time.
Quick Facts
- Product Used: Mill, Design, Multiaxis
- Industry: Aerospace, Heavy Industry, Job Shop, Medical
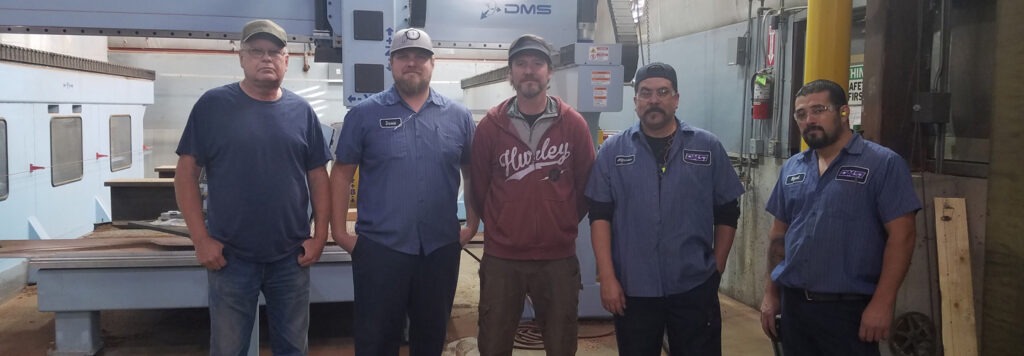
Project Details
- The Challenge: Find technology solutions to expand waterjet and router capabilities for complex machining.
- The Solution: Mastercam to prepare part files and flexible, precise control of CNC machines.
- Benefits:
- Gain the maximum benefit of the robot’s versatile range of motion.
- Power and precision to produce parts from art pieces to parts for aerospace.
- CAD/CAM power and efficiency for rapid prototyping working with varied stock materials.
DMSI works with customers ranging from the aerospace to medical to architectural to signage industries, machining 3-dimensional components on one of five water jet machines—one 7-axis (a robotic arm), three 5-axis, and one 3-axis— as well as two 5-axis routers and one 3-axis router when necessary. The fastest 5-axis machine operates up to 87,000 psi.
While one machine cuts 3D shaped components to customer specifications out of ¾” thick carbon composite, another cuts similar components from glass for artistic or architectural applications. According to Mike Long, DMSI President, programmers need to be well-trained in building programming for the different industries the company serves. With tight lead times, there is no room for error. Machining processes need to be verified prior to actually running.
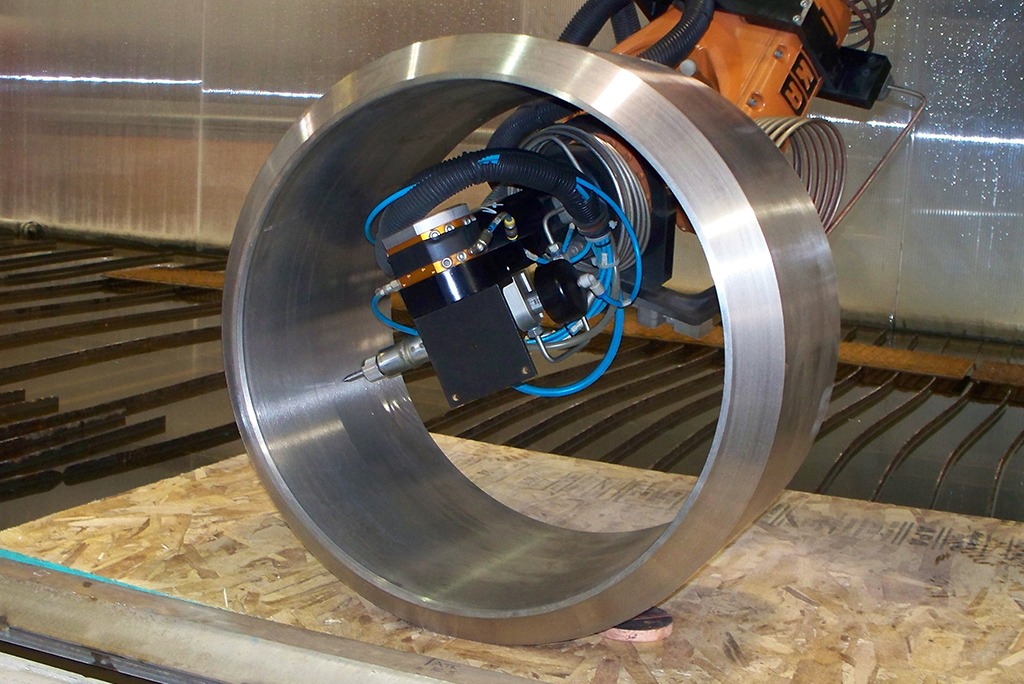
“The protocol of managing a small operation and serving very large customers can be a challenge in that there is zero acceptance of any component that is not to the drawing. If we have one-offs, there is no room for error. We have one billet, we make one part,” said Long. Composites need to be handled in a certain way, otherwise, micro fractures can occur—tiny cracks that can only be seen with a special machine, usually discovered after the part has left the shop. In order for the whole operation to work smoothly, the team of programmers and machinists need to be able to mitigate errors and downtime. Their Mastercam software is instrumental in verifying that not only the program is airtight, but that the actual machining is done right the first time.”
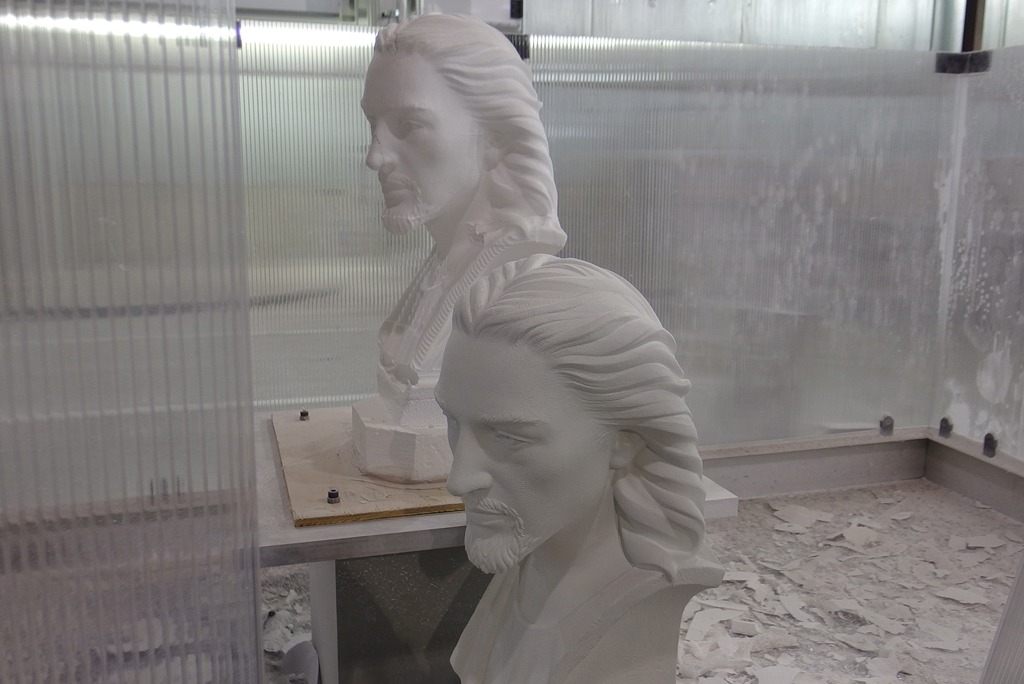
Dry runs are completed to ensure that the toolpaths are in place and in line with the fixturing, which poses an additional challenge when working with a 5-axis machine. “With 5-axis waterjet cutting, the tool is infinite. It’s lethal in 50 feet, so anything below the fixtures can be destroyed. We need to path around or build a fixture that allows us not to have any interference with the fixture itself, and that’s quite a challenge in some cases,” Long shared.
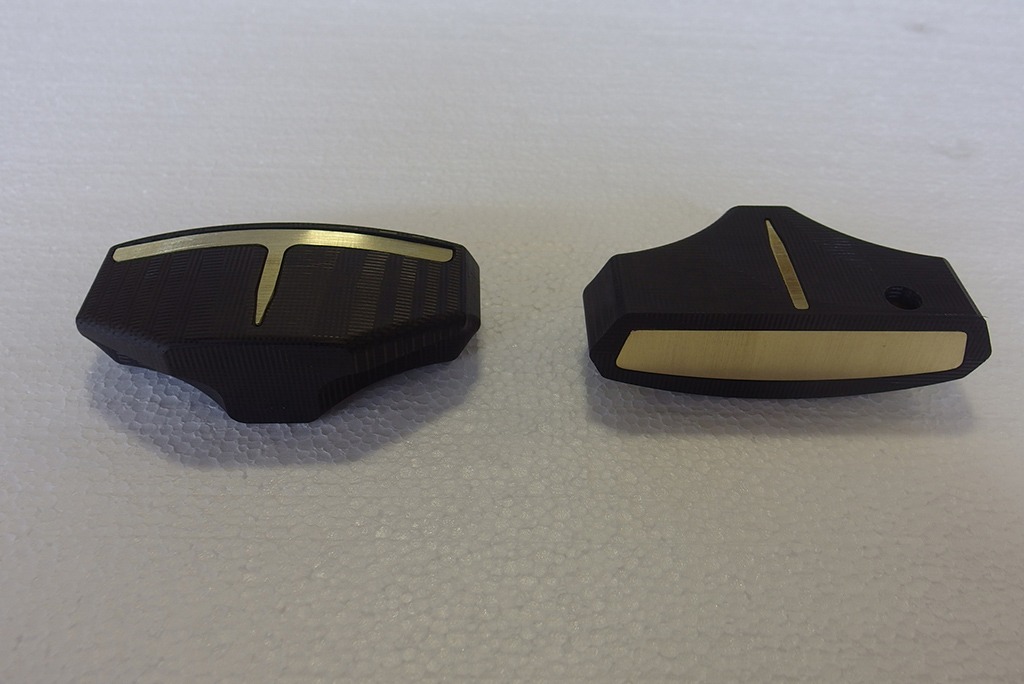
Using the software’s Verify function, the team can perform a pre-inspection of sorts, indicating where the toolpath might have exited, and when more material was removed than as specified in the code or in the toolpath. Once everything is verified, it’s time to manufacture the part. High-speed toolpaths are used for roughing operations for both parts and molds.
The water jet system can cut nearly any shape from materials ranging from 1/8” to 8” thick, with a radius as tight as 0.020”, and tolerances up to +/- 0.005”. The sixth and seventh axis robotic heads can cut in virtually any direction owing, in part, to their inverted position. The sixth and seventh axes allow the robot to move along a cut path of 24’ rather than perhaps 10’.
Nate Scoffield, head machine programmer pointed out that the longer cutting path allows more parts to be machined at one time. When combined with the router, the robot provides additional cutting and drilling functions.
The investment in so many powerful machines required a considerable upgrade to DMSI’s hardware infrastructure. The team relied on their Mastercam Representative, whom Long had known for more than 40 years. Long said they were supported in some areas of the software that they had not visited and in determining which toolpaths would work in a particular job. He was also introduced to SolidBox, also in Salt Lake City, which specializes in providing the hardware that can handle the shop’s demands.
By adding a 7-axis robotic head to their already impressive machining operation, DMSI has been able to perform multiple operations at one time. The key to doing it all faster is the equally powerful CAD/CAM software that now runs seamlessly on the right workstation.
Customer Quote
“One of the biggest challenges we had with a project was making sure the head of the router didn’t come close to, or collide with, the marble or fixtures. Mastercam’s Verify function allowed us to preview the cut path to make sure that those collisions between the head of the router and the marble would not take place. That would have been catastrophic.”
– Mike Long, President, Diversified Metal Services, Inc., Salt Lake City, Utah
“I think what Mastercam allows us to do is to get the support that we do from the Resellers. When we get into some difficult challenges, they’re there to support us. Mastercam is pretty complex so we’re learning daily the new processes that we’re able to do with it.”
– Mike Long, President, Diversified Metal Services, Inc., Salt Lake City, Utah