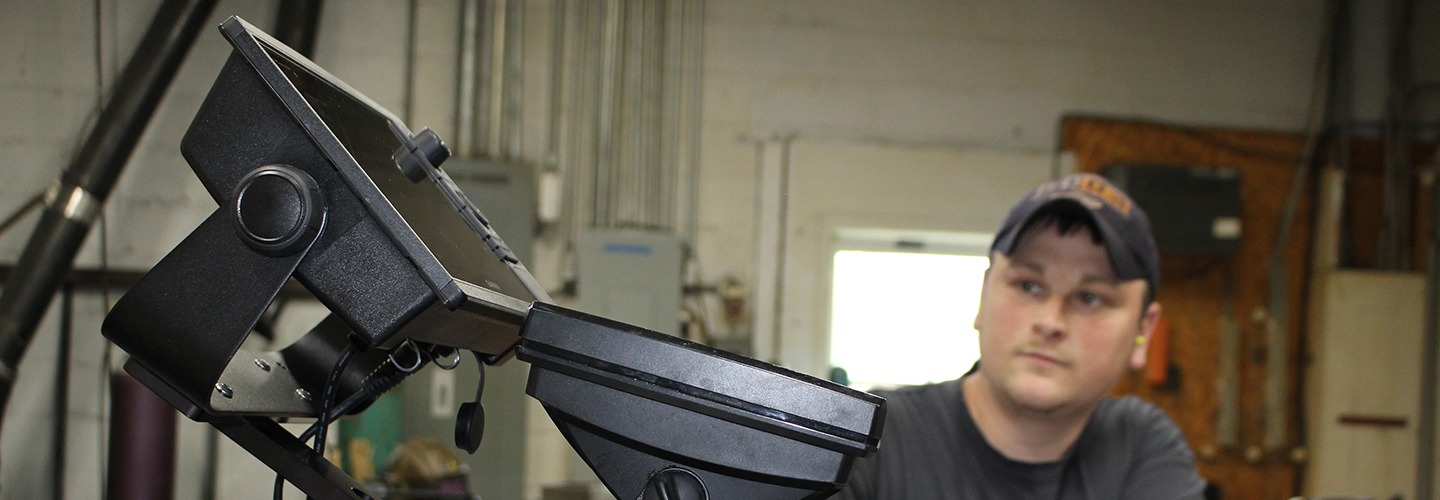
Production Tooling Makes Big Splash with Cornfield Crappie Gear
Production Tooling Automation expanded its machine shop to include faster more powerful machines and the software to run them when they landed a lucrative contract to produce crankshaft die blocks for an automotive supplier. After a few years of successful runs, reducing run time, and dramatically increasing the tool life of its endmills, the shop experienced a downturn. Founder Mark Ridl turned to his love of crappie fishing to expand his offerings into a whole new line of business.
Quick Facts
- Product Used: Mill, Lathe
- Industry: Consumer Goods, Tool & Die, Transportation, Job Shop
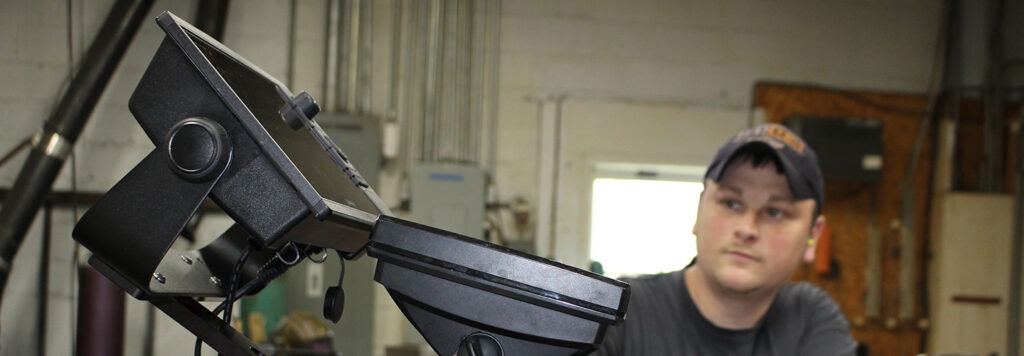
Project Details
- The Challenge: Improve efficiency, reduce production time, and minimize breakage to end mills while tapping holes in a hard, heavy, and proprietary composition material for a job forging crankshaft die blocks.
- The Solution: Milling and Lathe solutions from Mastercam
- Benefits:
- Using Dynamic Motion, the endmill is constantly engaged with the material, minimizing air cuts and allowing machines to be pushed to their full capacity.
- Reducing part runs from more than 60 minutes to 38 minutes.
- Constant tool engagement with even the toughest of materials results in runs yielding 16 parts per endmill when machining steels harder than 4140.
In 1997, Mark Ridl started Production Tooling & Automation (PTA), a small machine shop in the middle of the cornfields of Hoopeston, Illinois, with a couple of CNC machines. At the time, the company was writing programs by hand on a legal pad.
Over the next several years, his business grew steadily. In 2002, with goals to improve productivity and efficiency, and expand the jobs PTA could bid on, Ridl purchased a Haas milling machine and, at the same time, he obtained CAD/CAM software for the shop, choosing Mastercam Mill and Lathe.
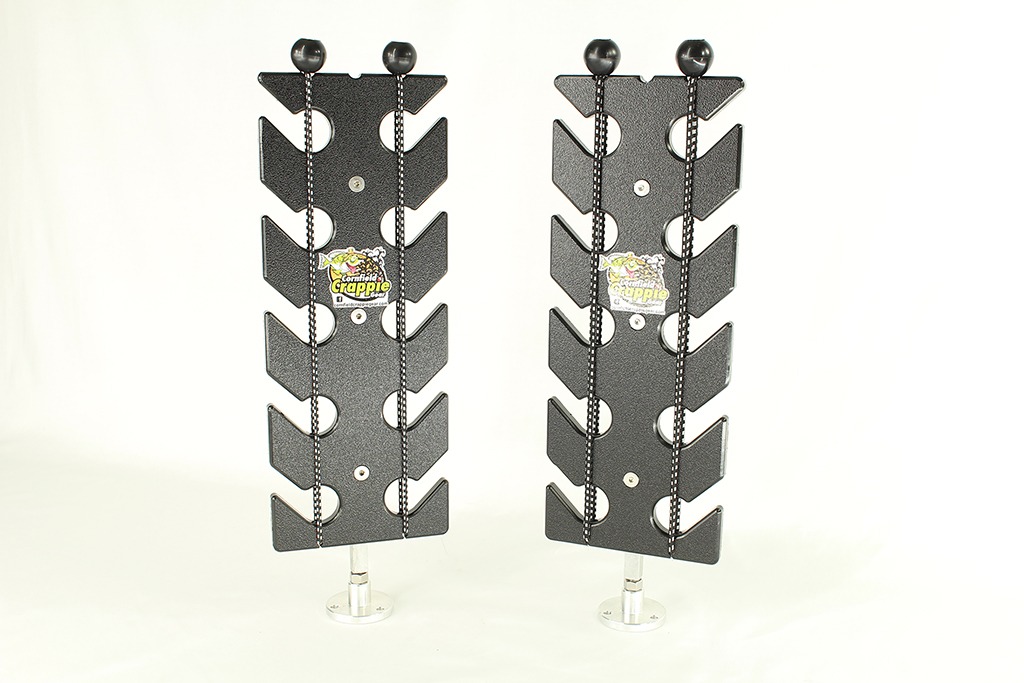
In 2011, the company landed a big job from a customer in the automotive industry (with contracts from Ford and General Motors) for forging dies for crankshafts. Immediately, PTA upgraded its Mastercam software to 3D and, with help from Mastercam Reseller, ShopWare, Inc., the company tackled the programming for the first die block job.
Things went anything but smooth. Once up and running, Ridl encountered a colossal challenge with the material being provided for the die blocks by a company in Germany. It was an incredibly hard and heavy, proprietary composition called CR7V.
“We were tearing up tooling, tearing up inserts, and, sometimes, wrecking one of the face mill heads. We were ramping-down to remove as much material as we could, to get the shape we wanted. Then we’d come back with a ½” carbide end mill and go in and finish the rest of it. One day, we went through $500 worth of drills trying to figure out how to tap a hole in that stuff,” Ridl recalled. “Plus, it took us an hour to make one part.”
Ridl and his lead machinist explored using Mastercam’s Dynamic Motion toolpaths to run the part. Dynamic Motion uses proprietary algorithms programmed into the software to keep the tool constantly engaged with the material, allowing it to cut intricate geometries at higher speeds. They kept trying different speeds and feeds until they finally figured it out.
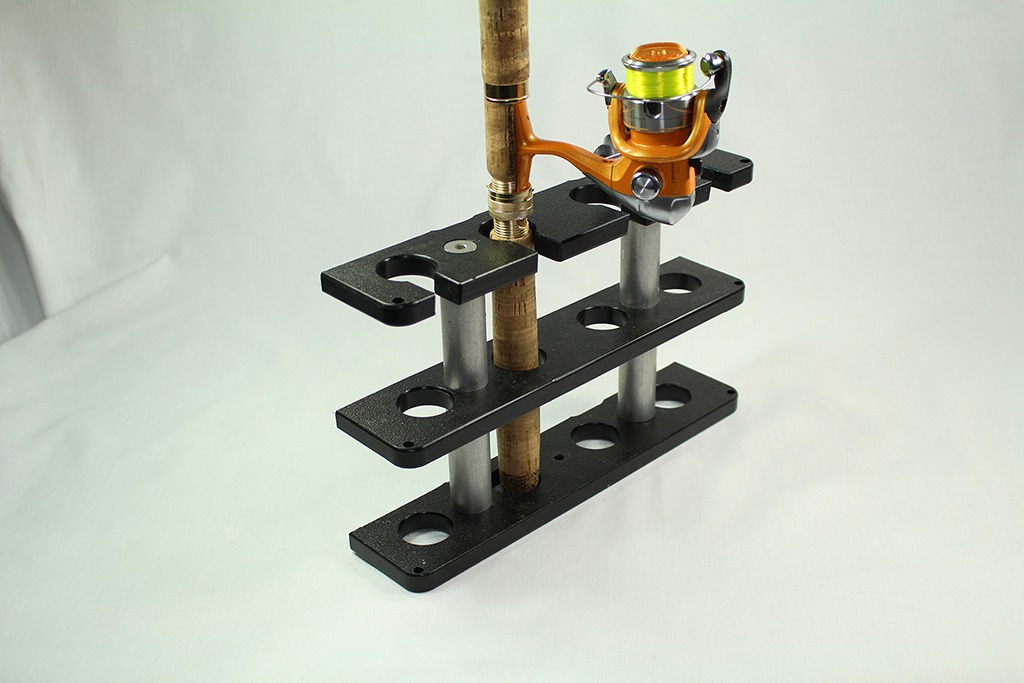
“Now we run the same part with a ½” carbide end mill. We went from just over an hour to 38 minutes to make a part. We run one end mill to do all of it, and we run multiple parts on that same end mill,” he noted.
“Before, we changed inserts for every part—sometimes, in the middle of the part. We maybe got one or two parts per end mill on the finishing. Now, we run 16 at a time. In fact, we now use the same end mill to rough and finish. We can run eight to 10 parts before changing an end mill and that’s using ordinary grit carbide.”
The story doesn’t end there. In 2014, with the lion’s share of its business coming from the automotive industry, one of PTA’s customers lost a big automotive contract. The shop began to struggle.
With his machines quieted down, a restless Ridl went back to something he knew: fishing for crappie, a type of freshwater fish native to North America. At his shop, he began making one-off boat accessories for himself and some of his friends.
Word spread, and before long, it became a side business for Ridl. He called the fishing gear products Cornfield Crappie Gear [https://www.cornfieldcrappiegear.com/], a nod to the company’s location in the cornfields of east central Illinois. The company’s premier product was a specialized monitor mount, an arm/bracket that holds an electronic monitoring unit (like a GPS) in place.
Over the next few years, demand for the fishing gear increased and orders came rolling in. Ridl moved his family, his business, and his lead machinist to Gilbertsville, Kentucky.
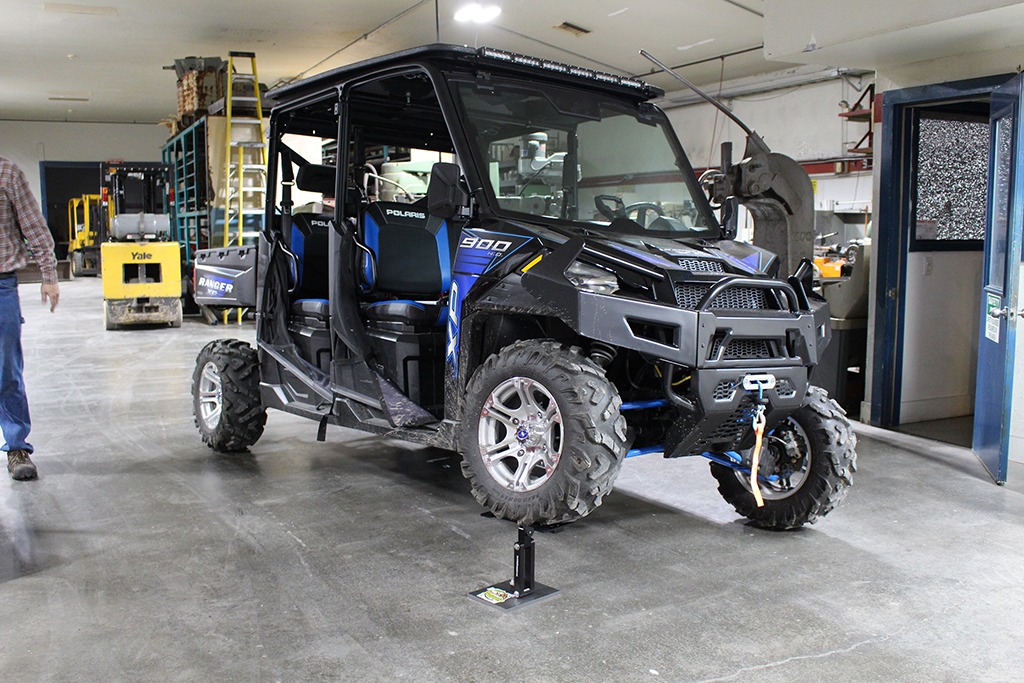
In addition to the monitor mount, Cornfield Crappie Gear makes the patented Cable-Save’R, an accessory that Ridl designed to solve a problem he had running the wires from the electronics box in the boat to the transducer, along with drift paddles, rod racks, and trolling racks.
Today, PTA has five 3-axis vertical mills, one with extra travel (60 inches in X), and all with fourth axis available; an indexing head, and a trunnion table. They have use Mastercam to program them all. Ridl reported that PTA is now using the software’s Dynamic Milling feature for much of their work.
“It’s just unbelievable how fast you can run hard materials, soft materials—it doesn’t matter. Whatever you have,” Ridl said, “Mastercam makes it easy. If I’m honest, Mastercam is a big part of our success in accomplishing basic 3D machining,” Ridl said.
Customer Quote
“Once again, ShopWare helped with the upgrade and gave us some of the best technical support you could ask for. With their help, we tackled the programming for the first die block job for forging dies for an automotive supplier to General Motors and Ford.”
– Mark Ridl, Owner and President, Production Tooling & Automation and Cornfield Crappie Gear