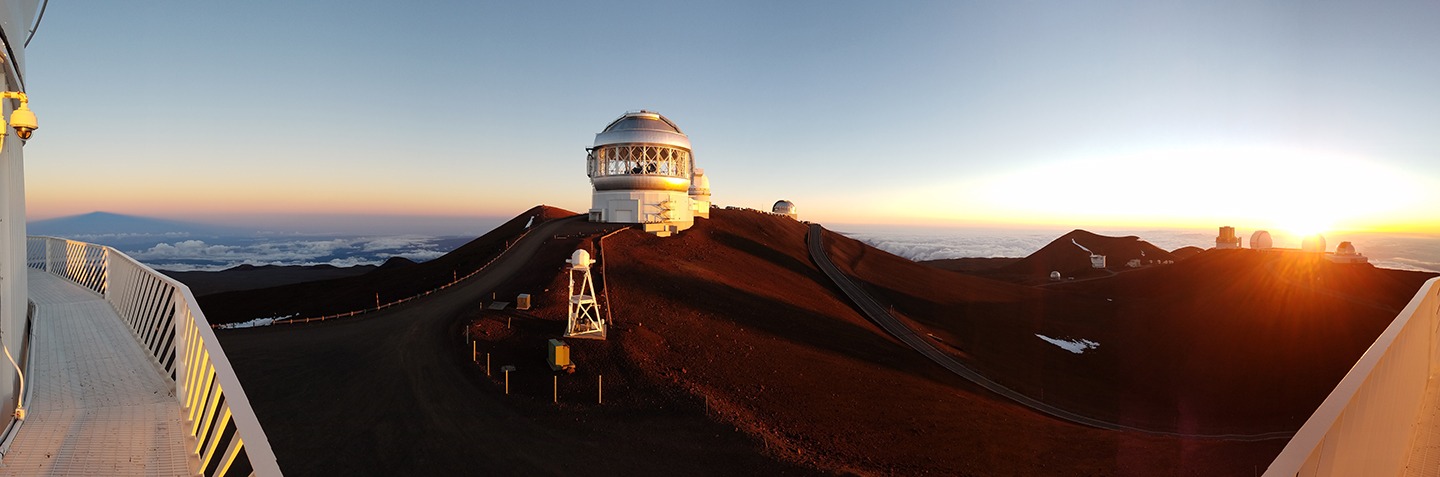
CAD/CAM Provides Precision for Stargazing
At the most scientifically productive site for astronomy in the world, Greg Green has the opportunity to machine parts that hold million-dollar chips, all with a 24-year-old machine, CAD/CAM software, and creative fixturing.
The Challenge
Flexible machining with high precision and a low budget.
The Solution
Mastercam, the most robust CAD/CAM software for machining applications.
Benefits
- Maintains tight tolerances.
- Provides reliable machining accuracy.
- Produces high quality finishes.
Project Details
Have you ever gazed at the vastness of the stars and wondered what else your CNC machine can create? Greg Green had the opportunity to find out when he joined the staff at the Canada-France-Hawaii Telescope (CFHT) in Waimea, Hawaii.
Green is the sole mechanical designer and instrument maker for the 3.6-meter telescope on the summit of Maunakea, a dormant volcano. He can be found in a back building of the headquarters in Kamula, where a machine shop houses one CNC vertical machining center and several manual tools, including Bridgeport Mills, lathes, and surface grinders.
For the past 10 years, Green has been responsible for machining parts to maintain and extend the capabilities of the facility’s five instruments.
CFHT is the oldest telescope in the Maunakea Observatories, a collaboration of 12 non-profit institutions that make up the most scientifically productive site for astronomy in the world. The location contains optimal conditions for high-quality viewing and date collection.
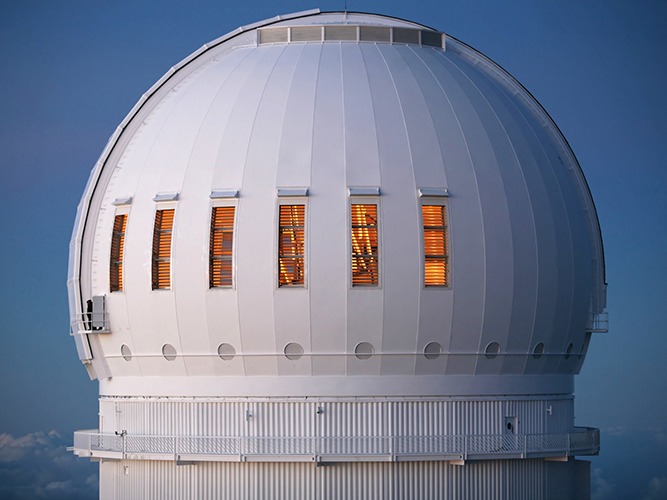
The machine shop houses one 3-axis 1999 Cincinnati Arrow 500 CNC vertical machining center. Green machines parts such as camera bodies and heat exchangers using mostly aluminum with some stainless steel, titanium, and Invar, an iron-nickel alloy.
CFHT instruments cost millions of dollars. If a part needs to be fixed or improved, Green is involved with the development process from design to production. He uses Mastercam to successfully meet strict processing requirements.

“Having in-house machining is a rarity,” he said. “Our engineers come up with very creative solutions to make our instruments better and, usually, I can implement them that same day. We go through this process of testing, redesigning, and making new components constantly and we eventually arrive at something that works very well.”
Instruments at the observatory are supercooled to 70 K, or -334°F, to improve the signal-to-noise ratio. Located 60 miles away, the machine shop is at a significantly lower altitude with warmer temperatures around 75°F. Components must effectively perform with large thermal variations, as well as maintain tight tolerances measured in angstroms, or a hundred-millionth of a centimeter.
“When tracking something that moves across the sky—an asteroid flying past the Earth or a whole other galaxy—our telescope moves at the rate that the object moves across the sky,” Green said. “You can imagine that things get a little fussy.”
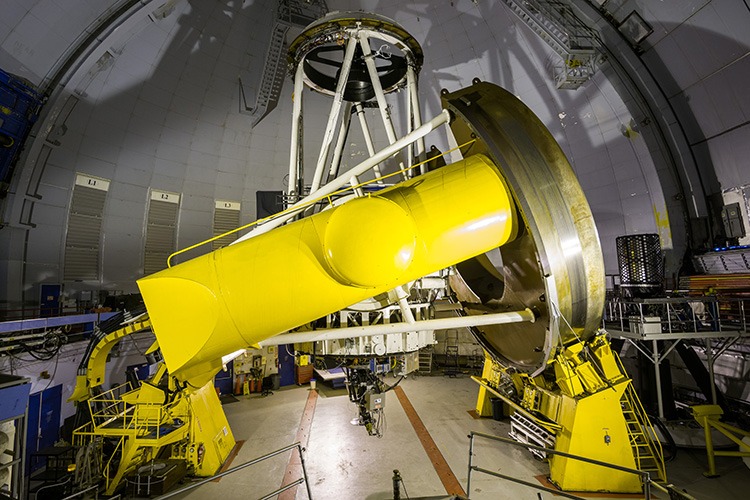
One of the more challenging projects for Green was creating the structural components for a small astrometric camera that drives the big telescope, similar to a sight on a gun.
Some components were so large, they required four different machine setups.
Green added holes to the design, allowing him to connect the part to a surface plate with dowel pins. He then indexed the part on the fixture to access the different areas for machining.
The finished structure included carbon fiber tubes bonded to an aluminum end and bolted to a semi-sphere joint.
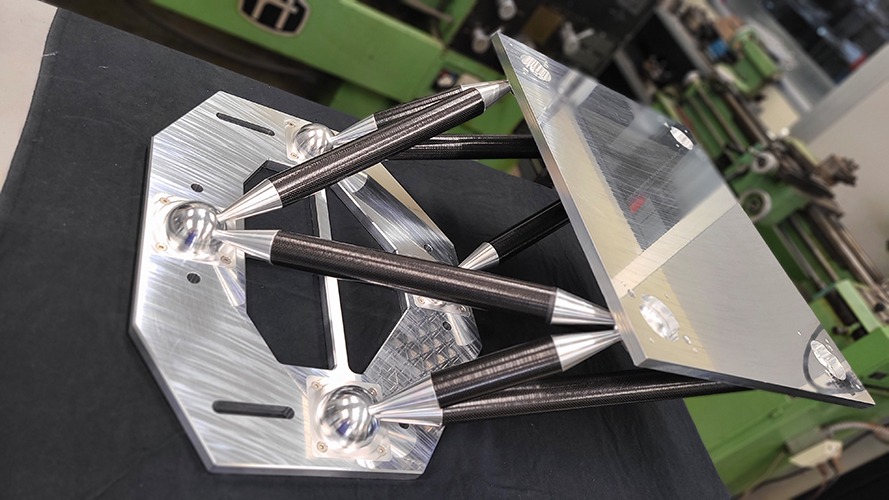
Machining accuracy is critical. Any mistakes would be costly, requiring additional materials and shipping time. Most resources are only available from the mainland, including repair services.
Since each part is unique, Green uses simulation to prove programming accuracy. “The Verify feature in the software is priceless,” he said. “I know my post that spits out the G-code is reliable and what I see on the screen is what’s going to happen on my machine, so I don’t have to scrap something that I’ve been working on for a month.”
Green enjoys the variety at CFHT. At the most scientifically productive site for astronomy on the planet, he has the opportunity to machine parts that hold million-dollar chips, all with a 23-year old machine, CAD/CAM software, and creative fixturing.
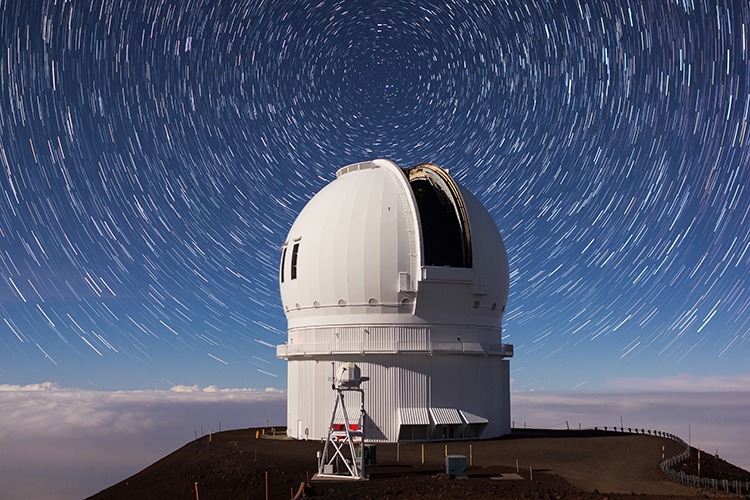
““This is the best job that I’ve ever had,” said Green. “The benefits and location are amazing, and I never make two of the same thing.”
Quick Facts
- Product Used: Mastercam
- Industry: Aerospace, Education
“The Verify feature in the software is priceless. I know my post that spits out the G-code is reliable and what I see on the screen is what’s going to happen on my machine, so I don’t have to scrap something that I’ve been working on for a month.”
Greg Green, Mechanical Designer & Instrument Maker, CFH Telescope, Waimea, Hawaii