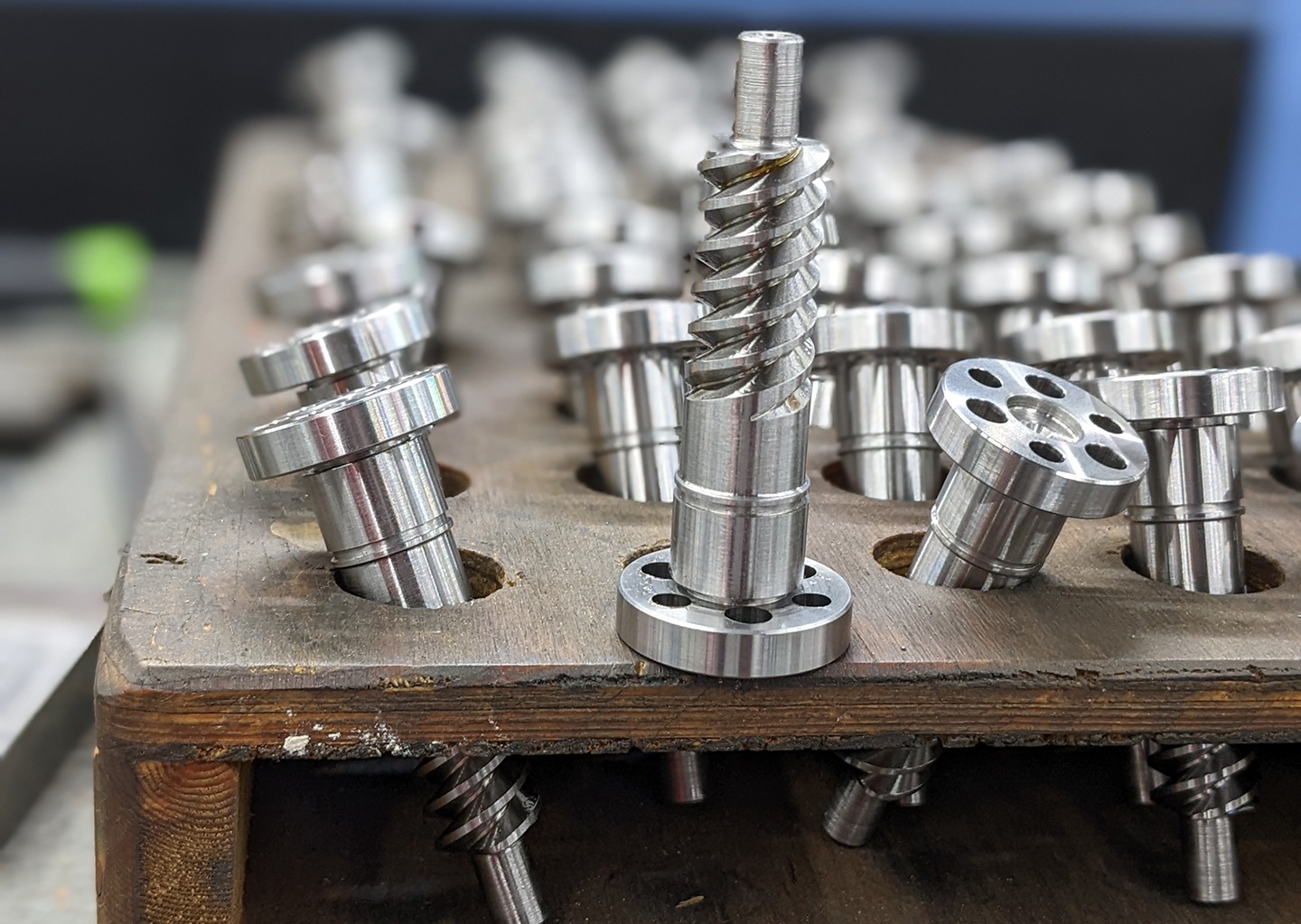
CAD/CAM Software Integration Streamlines Gear and Rack Manufacturing
When Avers Machine and Gear expanded through acquisition, it needed to bridge the gap between the two machine shops. Team members evaluated what was driving value at each facility and implemented best practices, leveraging Mastercam to provide a successful integration.
The Challenge
Integrate two machine shops.
The Solution
Mastercam, the most robust CAD/CAM software for machining applications.
Benefits
- Standardized programming meets customer demands. Allowed team to increase rack’s output from 12 parts per hour to 40 to 45 parts per hour.
Project Details
Started in 1989, Avers Machine and Gear (Schiller Park, IL) is home to a 30,000-square-foot facility. President Chris Wellman and his partners decided to grow the operation and searched for two years before acquiring Innovative Rack and Gear (Wood Dale, IL), which consisted of a 20,000-square-foot facility.
Together, two facilities and 55 employees offer gear and rack manufacturing and machining services. To optimize their strengths, Avers and Innovative Rack and Gear employees—including 40 machinists, 14 of whom are programmers—used their expertise to integrate their systems, including Mastercam® CAD/CAM software.
The standardization of CAD and CAM software allowed operations to be streamlined throughout both facilities. Whether a part was initially run on the Doosan or Okuma machines, programmers now have the ability to change equipment as needed based on customer demand. With frequent schedule changes, workflow scheduling is distributed more efficiently for each department
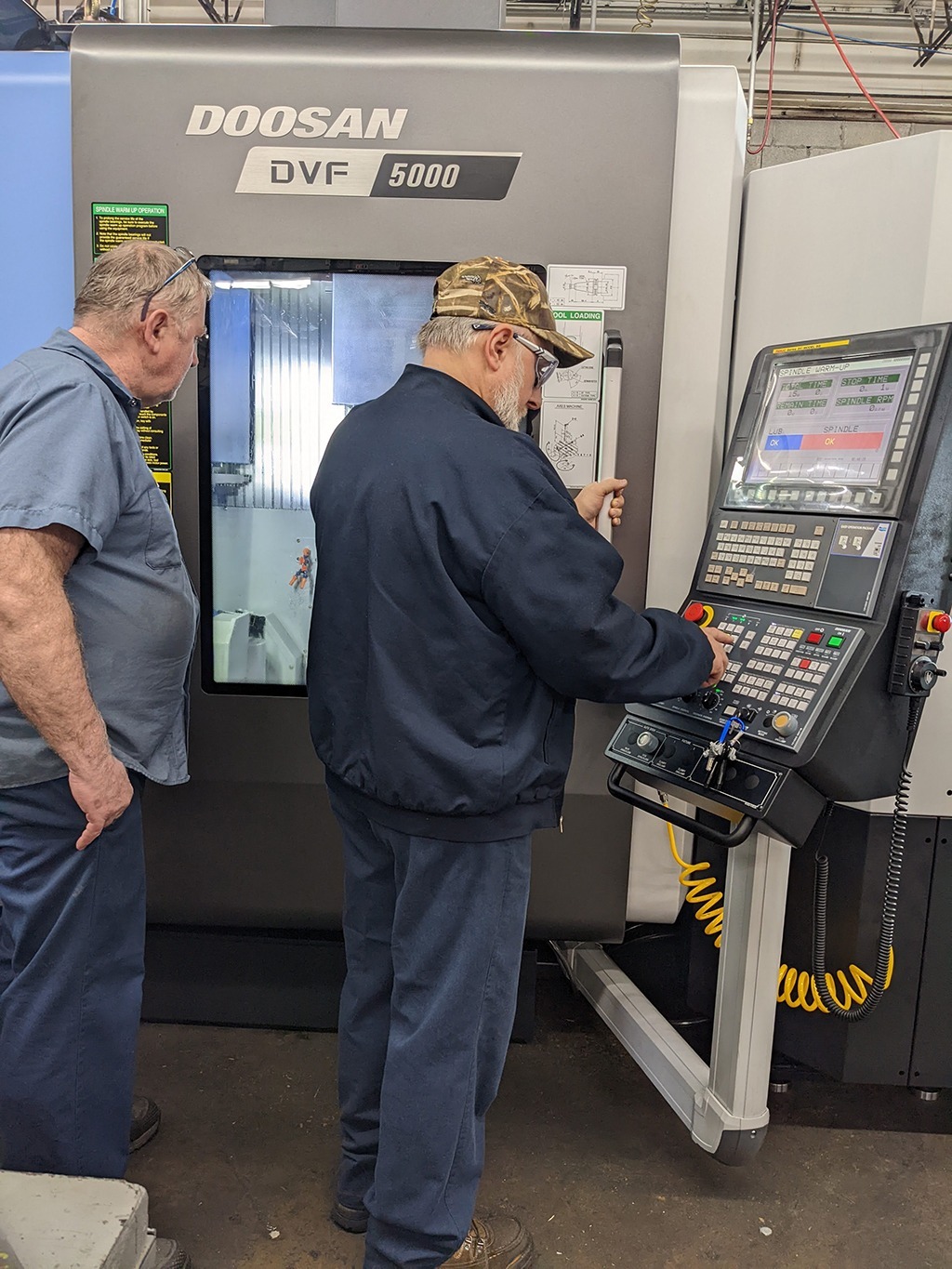
“Mastercam gives us tremendous flexibility to run repeat jobs in a multitude of work centers,” Wellman explained. “I think the key to any job shop is to be flexible.”
To maximize profitability, the new owners analyzed each product and discovered one rack was losing money. So, the Avers and Innovative Rack team had to figure out how to retain the customer and make the part at the contracted price.
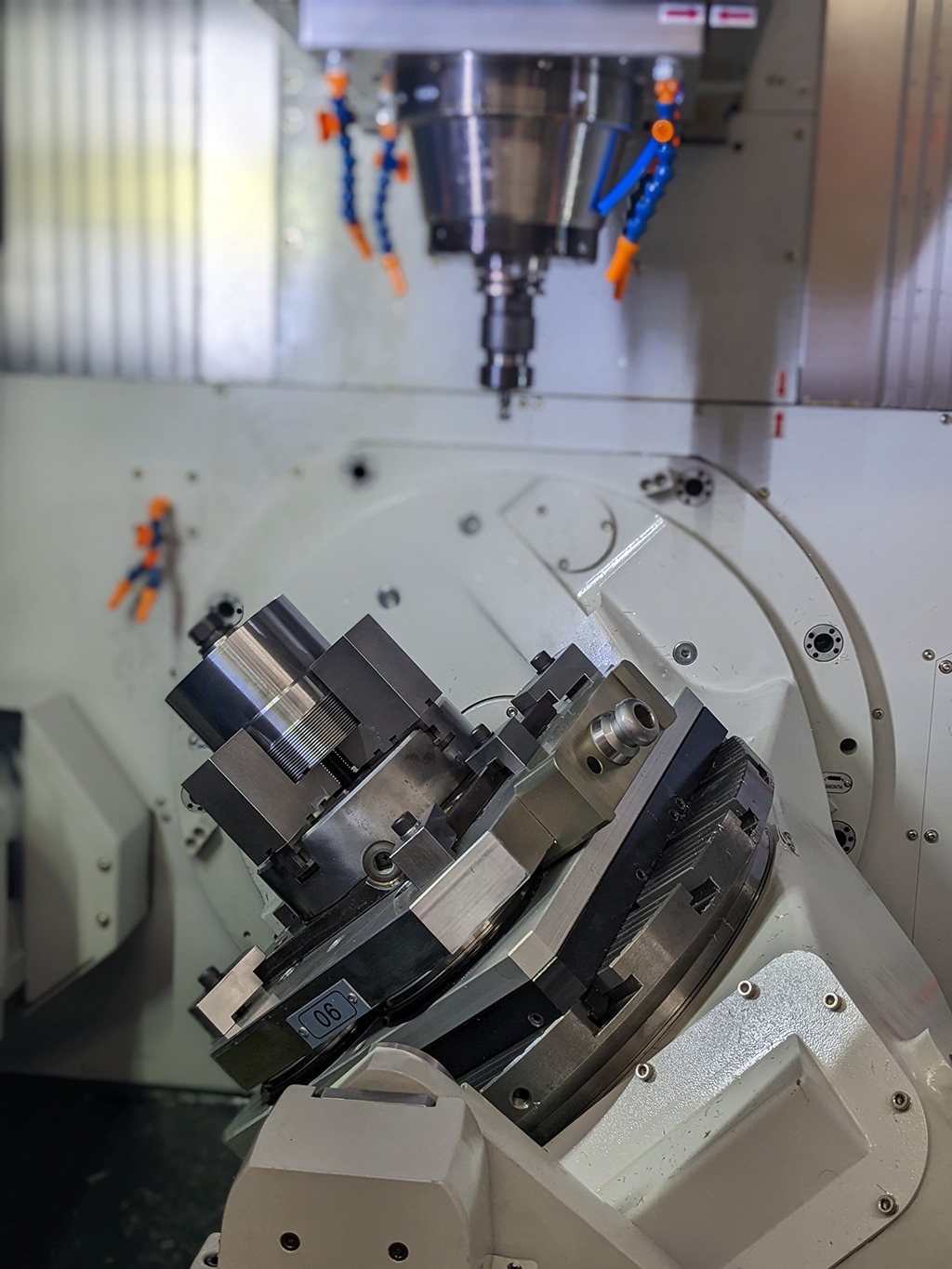
The engineers and programmers assessed the rack’s current production methods and found that the rack was being held in a simple plate fixture. The cycle time was roughly two minutes before it would be manually flipped by an operator, repeating two times. Including the time required for part changes, the operation had more downtime than uptime.
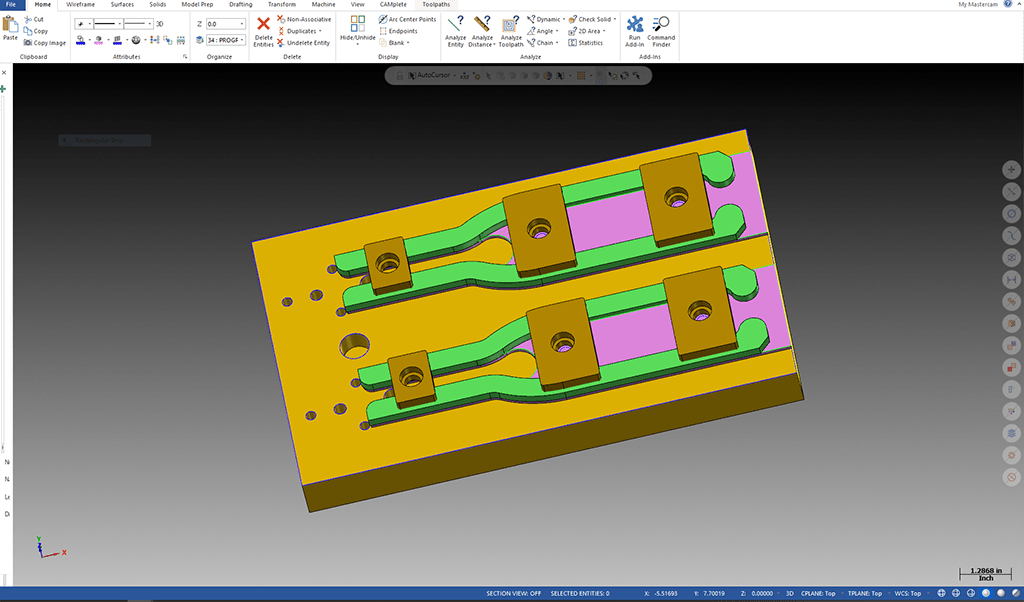
To make the rack cost effective, the team designed a fixture in SOLIDWORKS (Dassault Systèmes, Velizy-Villacoublay, France) that could hold eight workpieces at once. The part was clamped to an island with the ends overhanging, allowing the part to be suspended and machined on both the top and bottom sides, without having to be flipped. The solid model was imported into Mastercam where the 2D Dynamic Contour toolpath ensured the proper chip load. The whole fixture was machined on one end mill, with one tool completing the majority of the work.
The setup time for the rack was successfully reduced to a single process, letting the machine run more effectively. The output changed substantially, increasing from 12 parts per hour to 40 to 45 parts per hour
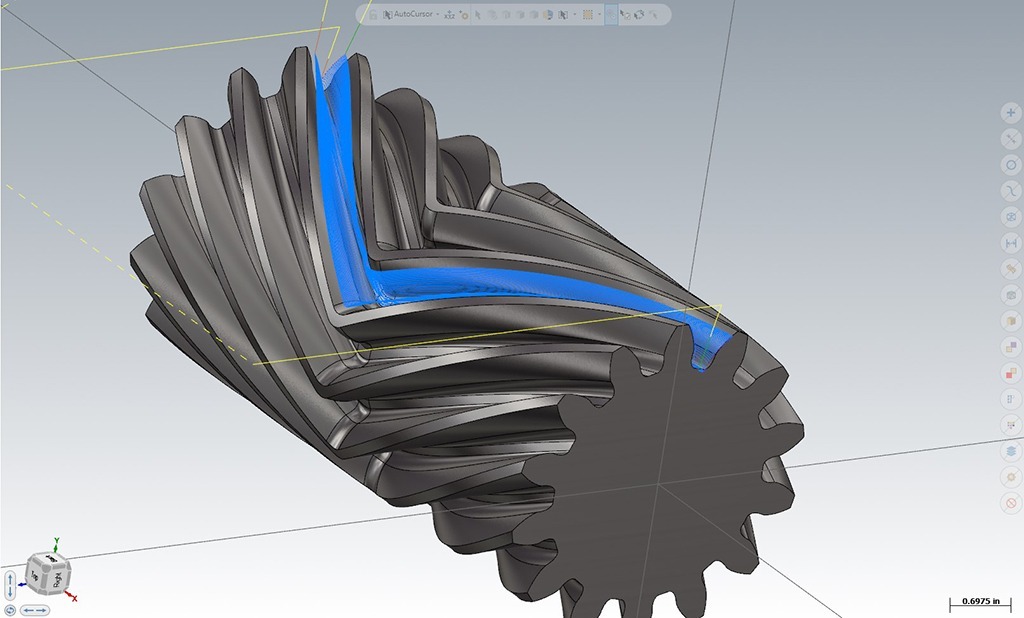
Looking forward to potential growth, Avers increased its capabilities to manufacture complicated geometries by upgrading to 5-axis machining. The company uses the Maintenance Program through its Mastercam Representative ShopWare Inc. (Elgin, IL) to help keep up with the latest technology. Employees have access to the most up-to-date software versions, as well as new features, and can call a ShopWare helpline if any assistance is required.
Like with any transition, there were bumps along the way. But, Avers Machine and Gear was able to overcome these challenges and integrate its acquisition successfully.
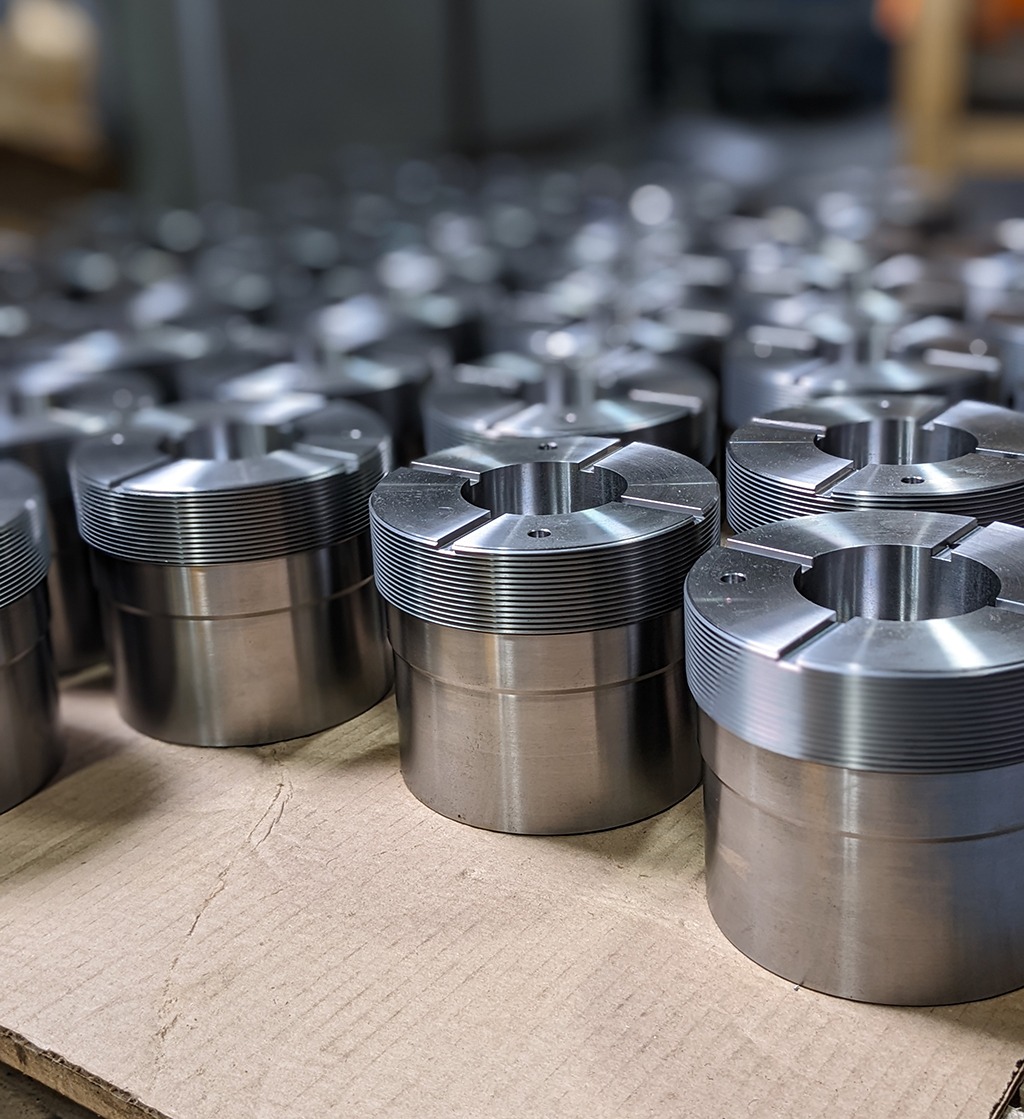
“Systems are extremely important,” concluded Wellman. “Whatever system you choose, everybody needs to be fully trained and integrated, and everybody needs to use it.”
Quick Facts
- Product Used: Mastercam Mill, Mill 3D, Multiaxis, Lathe, Maintenance
- Industry: Manufacturing, Gear and Rack
“Mastercam gives us tremendous flexibility to run repeat jobs in a multitude of work centers. I think the key to any job shop is to be flexible.”
Chris Wellman, Owner and President, Avers Machine and Gear, Schiller Park, IL