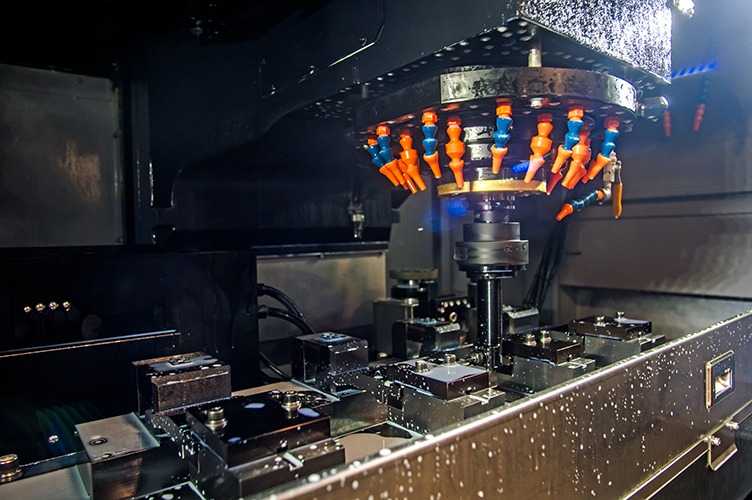
CAD/CAM Software Cuts Combined Cycle and Deburring Time in Half
AMADA TOOL AMERICA, INC. unlocked the potential of its CAM software through employee-led process improvements. As a result, combined production cycle and deburring time was cut in half and the tooling manufacturer now has the agility to quickly adapt to product changeovers.
Quick Facts:
- Product Used: Mill, Lathe, Mill 3D
- Industry: Tooling Manufacturer
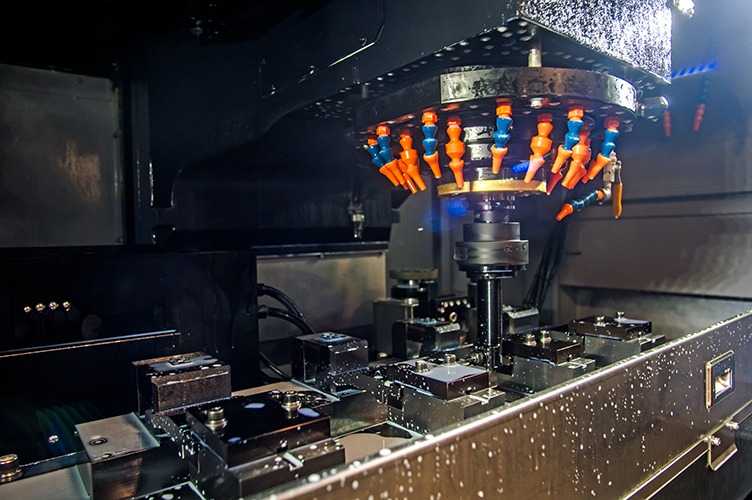
Project Details
- The Challenge: Streamline programming for high product diversity.
- The Solution: Mastercam, the most widely used CNC software for machining applications.
- Benefits:
- Standardized equipment setups.
- Improved surface finish quality; elimination of manual finishing.
- High Speed toolpaths increased productivity and improved surface finish quality.
AMADA TOOL AMERICA, INC. (Batavia, NY) operates as a flow shop, manufacturing all tooling for the turret punch press and press brake machines for its parent company AMADA Co., LTD. (Isehara-Shi, KNG, Japan). However, unlike in a typical flow shop process, each part can have a high number of variations that require different setups and timely changeovers.
The complexity translated into an opportunity to standardize programming, so AMADA TOOL AMERICA purchased Mastercam CAD/CAM software. Incorporating barcode scanners, operators scanned part numbers to easily access programming files for the machine and efficiently start production.
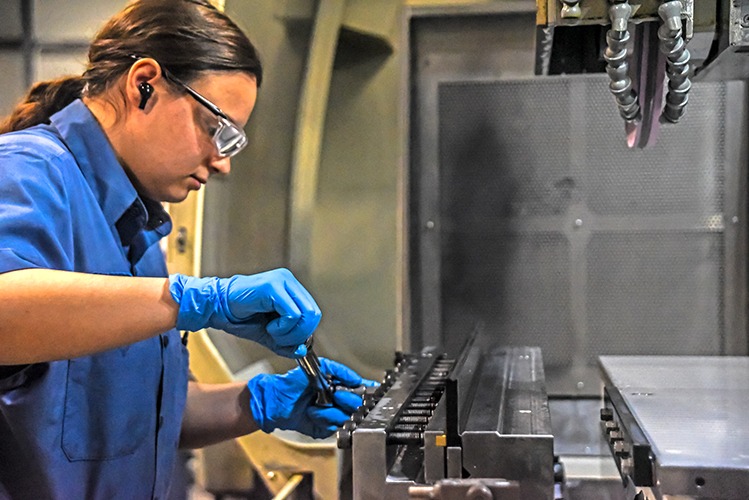
The most significant process improvement involved a tool manufactured for the AMADA HRB series Automatic Tool Changer (ATC). Using a 4-axis mill outfitted with a trunnion table, the parts were mounted on a fixture plate and machined on the top and back sides, with a slot providing access to the back. Initially, the part had a run time of 90 minutes plus manual deburring of 20 minutes. After programming updates, the total cycle time was substantially reduced to 35 minutes, with deburring occurring in the machine. Final savings totaled 34 percent reduction in cycle time alone; 50 percent reduction in cycle time and deburring combined; and 58.5 percent reduction in tooling cost per part.
To achieve these results, Programmer Ricky Streiff incorporated a Dynamic Milling toolpath followed by a 3D Contour toolpath, which enabled the same bull end mill to first rough out a slot and then ramp up at an angle, creating the desired chamfered edge. The 3D toolpaths also applied a radius to holes located on an incline of the part surface. In both examples, the need for manual finishing was eliminated and surface finish quality improved.
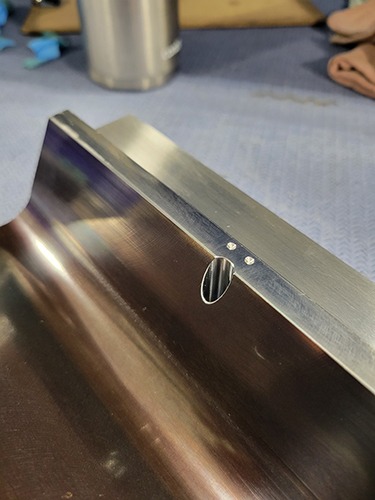
“The toolpaths were much more intuitive,” explained Streiff. “It was very easy to make new programs with less air-cutting and unnecessary tool engagement, like plunging and retract motions.”
Streiff said the tool life of most tools quadrupled due to reduced cycle time and force loads. Dynamic Motion technology continually adjusted the cutting motion of the tool to maintain constant chip thickness. Since cutting forces were controlled, the amount of generated heat and vibrations was reduced, despite some of the parts having lighter clamping methods with higher vibration potential. The entire tool length was engaged, yielding greater material removal with less tool wear.
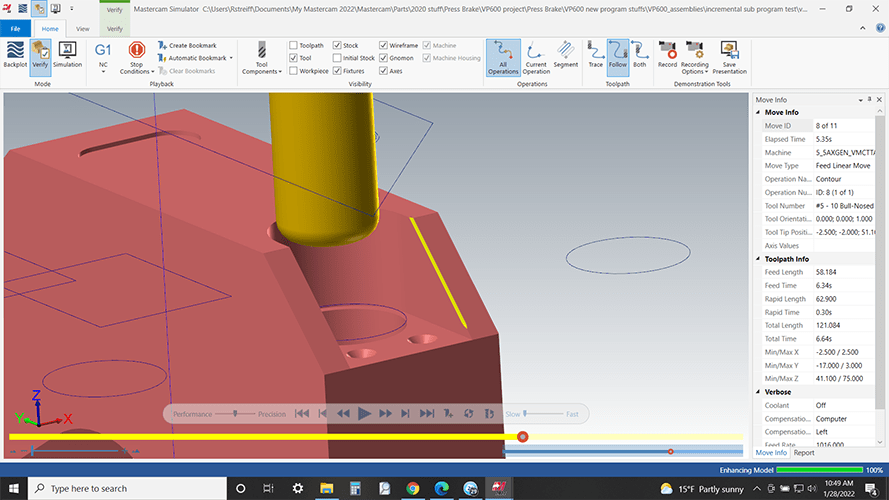
Customer Quote
“The toolpaths were much more intuitive. It was very easy to make new programs with less air-cutting and unnecessary tool engagement, like plunging and retract motions.”
—Ricky Streiff, Programmer, AMADA TOOL AMERICA, Batavia, NY