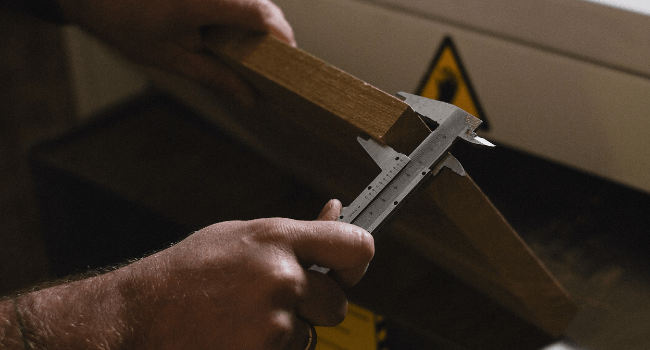
Ask the average American to estimate how long something is, and they will probably answer in inches, feet, or yards. If you ask someone anywhere else in the world, though, the answer will probably be in millimeters, centimeters, or meters.
Today, only three countries use the British Imperial System almost exclusively—the United States of America, Myanmar, and Liberia.
The imperial system dates to the seventeenth century and is comprised of units like pounds, feet, and acres. It was based on using ones own body to measure. An inch was meant to be the width of the thumb, a mile was meant to be one thousand paces, and a cubic inch was meant to be one mouthful. Naturally, measurements vary widely among people and there is no intuitive way to convert among most units. While it was useful hundreds of years ago, the system is less so now.
The metric system, or the Système International (SI), is nearly as old. It was invented in France in 1795 to deal with confusing conversions. The meter was initially based on the length of 1/10,000,000 of a quadrant of Earth’s circumference, or one ten millionth of the shortest distance from the North Pole to the equator passing through Paris. All units in the system were then derived from the meter. For example, a meter is 100 centimeters (centi means 100), and a gram is one cubic centimeter of water at its maximum density. With such a system, conversions are simple.
So why hasn’t America made the switch to metric if it is so much more logical?
To answer that, we can look at the U.S.’s northern neighbors. In the late 1960s, Canadian legislators began to understand the need for the metric system for international trade, especially in manufacturing. They introduced the “White Paper on Metric Conversion in Canada” and began incrementally switching Canada from the imperial way of measuring. Now, metric is used for large distances like kilometers in Canada. This change alone took years and substantial government money. Not only did automotive manufacturers have to start making odometers and speedometers that measured in kilometers, but the government also had to rewrite any legislature regarding speed and distance, and every speed limit sign had to be replaced.
Although much energy was put into the conversion, many Canadian citizens still use inches and feet for shorter measurements. They use metric for temperature (degrees Celsius) but imperial for weight (pounds and ounces). The same trend can be found in America, too. Many high schools—trade schools especially—teach their students to measure with the metric system or teach a mix of both, depending on the age of their textbooks. However, when those trade school graduates enter the workforce, they often find that their older coworkers are more comfortable with the imperial system and naturally adopt it themselves.
For many small job shops, this will not present much of a problem. However, for other manufacturers it will mean the difference between growth and stagnation. Consider a CNC machine’s smallest programmable value. In many centers, that value is 0.001 millimeter in metric and 0.0001 inch. If you convert those values, you will find that 0.001 millimeter is about equal to 0.00004 inch (less than half of the smallest programmable imperial value) and that 0.001 inch is about equal to 0.0003 millimeter (three times larger than the smallest programmable metric value). The bottom line is that programming in metric will often allow a machinist to meet tighter tolerances.
For those American companies wanting to expand into the international market, metric is a necessity.
Orders from overseas are almost guaranteed to be in millimeters and not inches. And while it is possible to use metric for international orders and imperial for domestic, switching back in forth in this manner introduces more chances for wasted time, inaccurate conversions, and inexact rounding.
Consider the Mars Orbiter catastrophe of September 1999. After ten months of travelling from Earth to Mars, the $125 million NASA probe that was meant to provide valuable data about the red planet suddenly burned up and broke apart. A review panel found the problem within the software that controlled the orbiter’s thrusters. Lockheed Martin Astronautics, which designed and built the probe, had used the imperial system to do so and had provided the orbiter’s force data in imperial measurements: pounds of force. NASA’s Jet Propulsion Lab assumed that the data had already been converted to metric, because using metric is standard practice in the aerospace industry. As a result, the orbiter’s thruster software first calculated in imperial measurements while another piece of code interpreted the calculations in metric. The miscommunication pushed the orbiter too close to Mars’s atmosphere, where it was quickly destroyed. The mistake caused NASA and Lockheed Martin millions of dollars and months of time. Manufacturing businesses are just as likely to be brought low by conversion mistakes if they use both imperial and metric.
For the sake of accuracy and international business, more manufacturing companies like IBM, Xerox, Caterpillar, GM, and Black & Decker are using metric.
But how difficult is this switch? Let us look at Ford Motor Company. According to the May/June 2017 issue of USMA Metric Today, Ford’s first metric-only production engine was the 2.4 L engine in the 1974 Pinto. This was the first noticeable step the company took toward its policy of using the metric system to reach more international customers, specifically in Great Britain and Germany. Starting with 1978 models, the North American Ford plants—including tractor and equipment plants—all joined a coordinated effort to formally convert under the justification that metrification would result in long-term profits. Their policy says, “All industrial nations are using or are converting to the metric system; continued use of two measurement systems in worldwide multi-national operations is incompatible with Ford’s basic objectives.”
According to spokespeople from Ford, the problems that they had originally anticipated with metrication never arose. Training skilled workers happened on the job and much faster than expected. Conversion costs never rose more than expected. The biggest issue, they said, was educating suppliers, but that was easily fixed by providing a manual of tool specifications. This indicates that, while daunting, switching an individual business from imperial to metric may not be as costly and time intensive as feared.
While most Americans will not likely see speed limit signs posted in kilometers or hear meteorologists give the daily forecast in Celsius anytime soon, it is reasonable to assume that most successful manufacturing companies will be using the metric system or making the switch in the coming years.