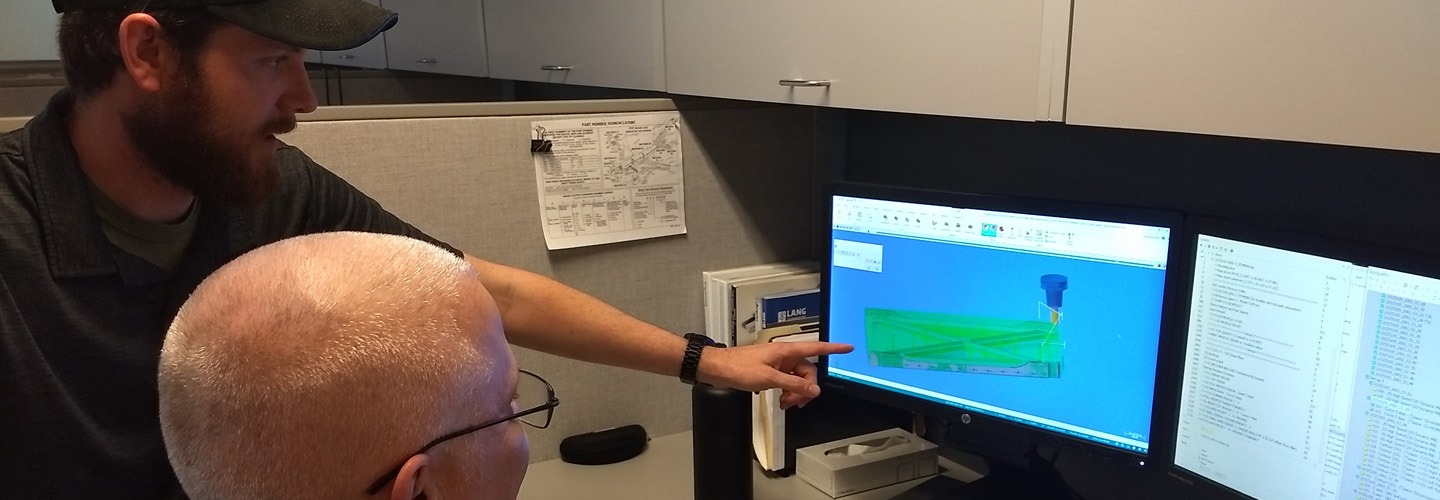
Evolving for the Needs of Aerospace
Royell Manufacturing has been able to grow its business as a Tier 1 manufacturer of structural components, kits, and assemblies to the commercial aerospace industry. The company invests in powerful CNC mills, lathes, and mill-turn machines powered by an equally powerful and flexible CAD/CAM software.
Quick Facts:
Product Used: Mill, Lathe, Multiaxis
Industry: Aerospace, Job Shop
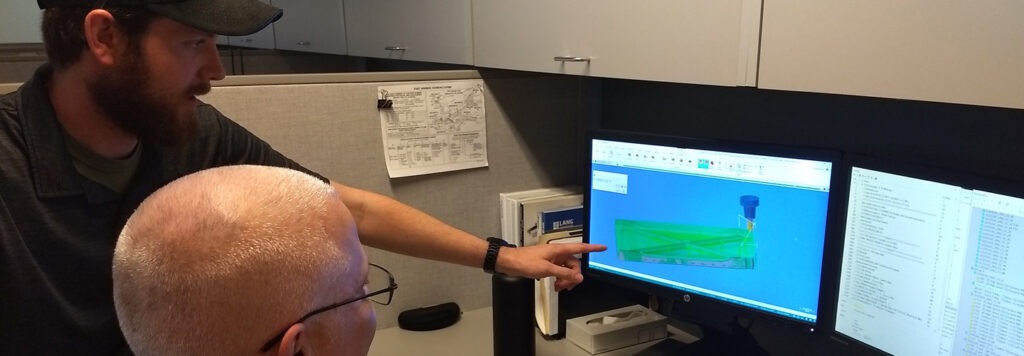
Project Details:
- The Challenge: From the beginning, Royell has been committed to evolving its business to keep up with the demands of their customers, many of whom require tough-to-machine components in two-week lead times. Their investment in expensive high-tech machinery required a flexible and powerful CAD/CAM program to make it all work in keeping with the company’s best machining practices.
- The Solution: Mastercam
- The Benefits
- Easy to learn and use.
- Supports 3-, 4-, and 5-axis vertical and horizontal milling machines, lathes, and mill-turn machining centers.
- Allows programmers to create template files to allow operation and tool libraries for quick precision machining.
- Software flexibility allows competitive pricing and reduced cycle times.
Started more than forty years ago, Royell Manufacturing is a contraction of founder Ron Yelle’s name. Still going strong, Royell rose from a small business to a Tier 1 manufacturer of structural components, kits, and assemblies to the commercial aerospace industry. In its state-of-the-art facility in Everett, Washington, the product is machined and fabricated from aluminum, titanium, and specialty alloys for large commercial, regional, and business aircraft programs. They also work Second Tier for major aerostructure businesses that are supporting the Airbus A350 nacelles and other key 787 programs.
The Royell business plan is to innovate and evolve, operating on the leading edge of manufacturing technology using lean methodologies to streamline production and link the shop floor with administrative offices. Beginning with vertical equipment, eventually transitioning to 5-axis machinery, Royell requires operating systems that can match demand.
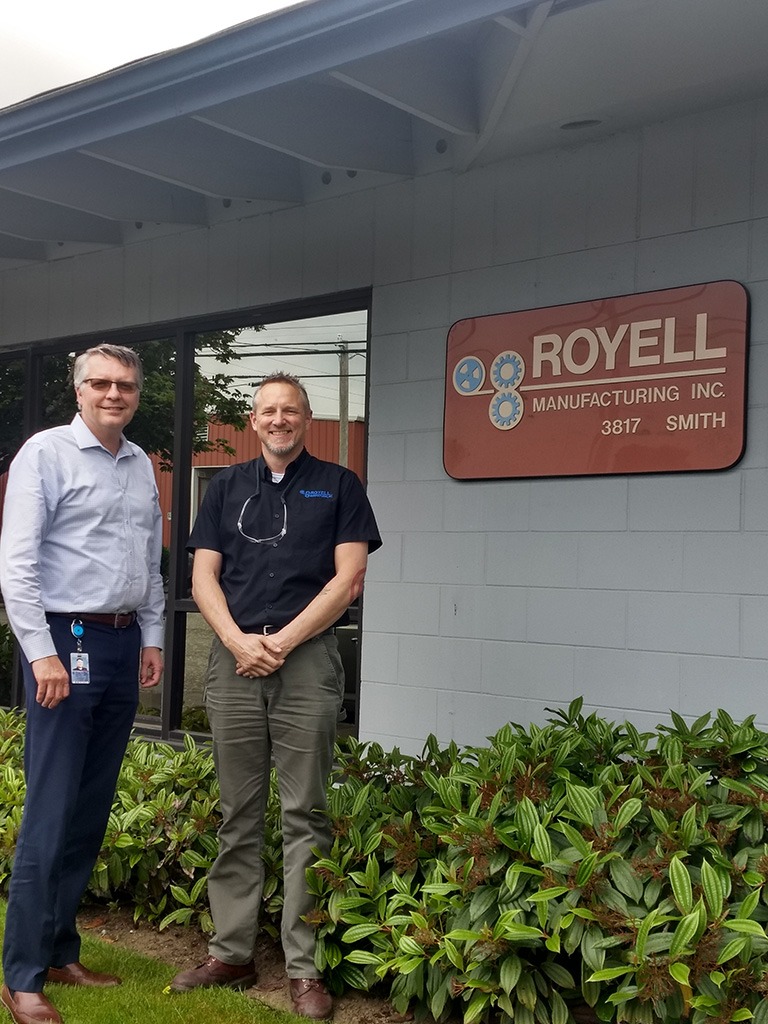
“Royell was working on a really complex part that should have been machined as a 4-axis or a 5-axis part. Our programmers couldn’t get the motion they needed using the CAM software we had at the time,” Methods Engineer, David Parkhurst recalled. “We purchased Mastercam in 2007 and developed live rotary toolpaths on a 4-axis machine for the first time. From there we cut our teeth with our first Matsuura MAM72-63V vertical 5-axis machine.”
Royell was one of the first aerospace manufacturers to employ the Swiss-made STC800X—serial number 001—by Starrag Machine Tools, a horizontal head table 5-axis machine with a 30,000 rpm, 160 horsepower spindle. Royell also incorporated the Grob G551 and later the G751, evolving its operation from vertical 5-axis to horizontal 5-axis machines. They now have many more 5-axis machines in service.
“The Grob machines’ two rotary axes are on the table, but the table can machine upside down. So, you can have the part upside down while you’re machining, and chips will fall just like rain. I believe Royell was one of the first of two companies to own a G751 on the west coast.”
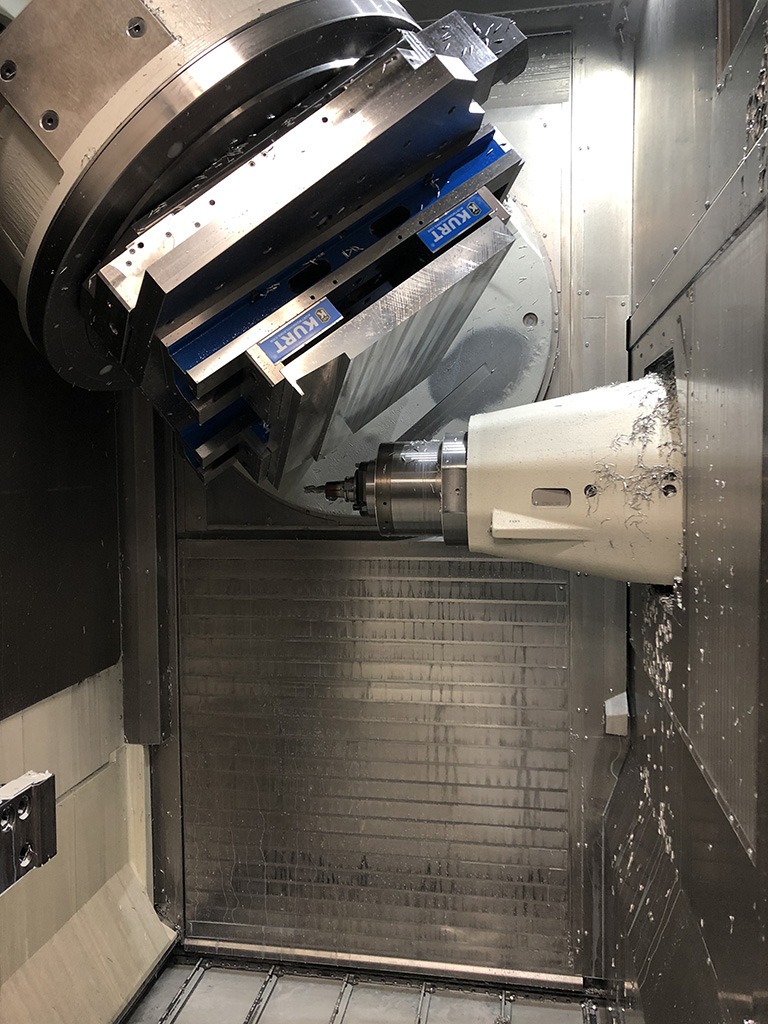
When it came time to develop the 5-axis post, Parkhurst turned to Mastercam Reseller MCAM Northwest in Oregon City, Oregon, who worked closely with Grob’s U.S. team, allowing the company to keep production rolling continuously.
Royell engineers can create template files that include operation libraries for dedicated equipment or cutting tool libraries for different materials and machines.
“We build those up front and have those files ready to go for the programmer, so it’s kind of a process of really just importing the model and applying prudent methods that we have. We like to think that we can both engineer and release new parts to production within two weeks. It’s incredible with regards to high speed machine motion.”
Mastercam tool libraries help Royell push their Dynamic Motion toolpaths for quick precision milling in hard to reach pockets and achieve tight tolerances measured in microns in sensitive and expensive materials like titanium.
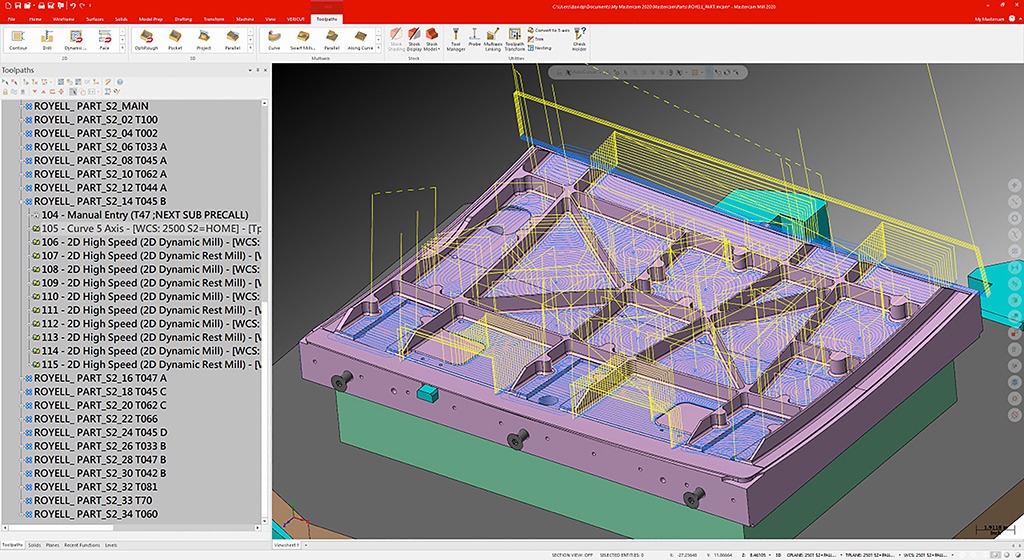
“What’s great is our programmers understand that you want to have a consistent angle of engagement on the tool,” Parkhurst explained. “So when it comes to cleaning out corners, we can go to our operations library, look at feeds and speeds and cut parameters that we use—for say a ¼-inch ball nose end mill that is extended out two inches out of the holder—and we know that when we use that same rest mill toolpath, it’s going to maintain the angle of engagement no matter what geometry we throw at it. With the 2D high speed toolpath libraries, we know that if our boundaries are correct and our stock is accurate, when we import a model and want to rough it down to size, we can quickly create the geometry we need then point and click. That toolpath is going to be successful, and the spindle load is going to be maintained throughout the cut.”
For Parkhurst and his colleagues at Royell Manufacturing, the combination of technology, innovation, and precision has helped them become a leader in their industry.
Customer Quote
“Mastercam represents our senior leadership’s investment in taking this company to the next level in the machining industry. Not only does it support the visions, goals, and aspirations I had and the accomplishments I wanted to achieve in machining, but it also supported this company’s drive to have a rapid implementation, first part success, and competitive cycle times for our customers. I just can’t stress enough how Mastercam is an effective tool for our Royell Manufacturing goals.”
—David Parkhurst, Methods Engineer, Royell Manufacturing, Inc., Everett, Washington
“At the time of our rapid implementation of multiple 5-axis machines, we contacted MCAM Northwest to help develop posts. They were up for the challenge of creating posts for an older piece of equipment that we were modifying from 4-axis to 5-axis. They have a great reputation for developing post processors.”
—David Parkhurst, Methods Engineer, Royell Manufacturing, Inc., Everett, Washington