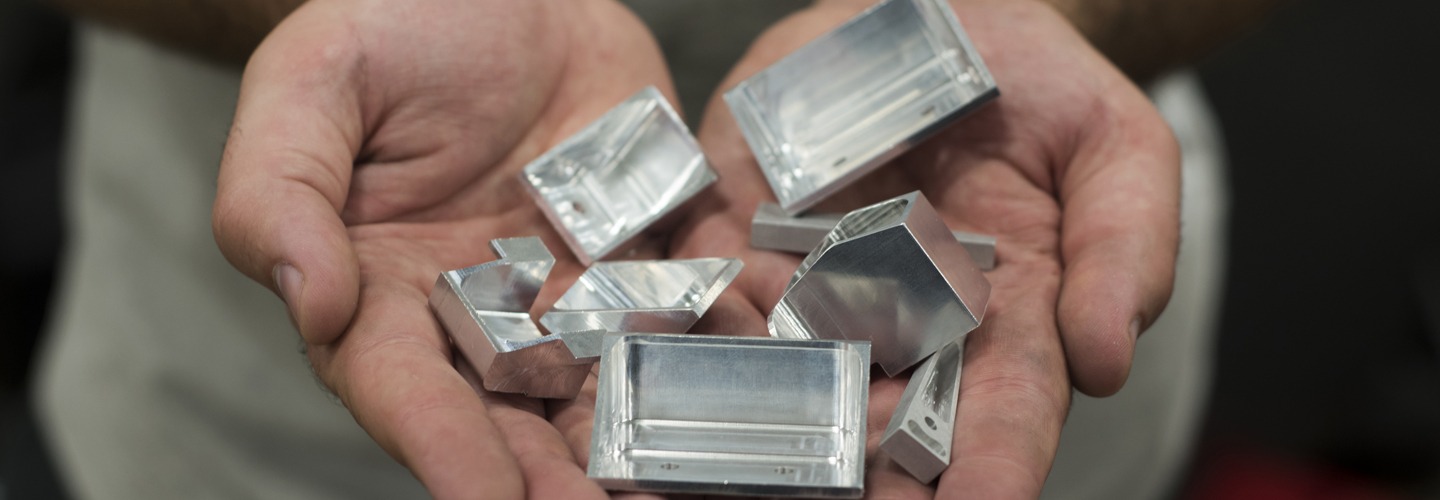
Cultivating Aerospace Competitiveness with CAD/CAM
Founded in 2001 by husband-wife team David and Penny Shaw, Flying S, Inc., sits just down the street from the farm that has been in the Shaw family since the 1700s. Having gained valuable work experience at Cessna, Scaled Composites, and Adam Aircraft, the Shaws returned home to Crawford County, Illinois, in 2001 to start their own aerospace engineering consulting firm, Flying S, Inc. It wasn’t long before David Shaw concluded that he needed the ability to fabricate his own designs to maintain tighter control over quality and lead times. With this approach, Flying S was able to secure a steady stream of new projects, including some from NASA.
Quick Facts:
Product Used: Mill, Mill 3D, Lathe, Multiaxis, Design, Art, Dynamic Motion
Industry: Job Shop, Aerospace & Defense
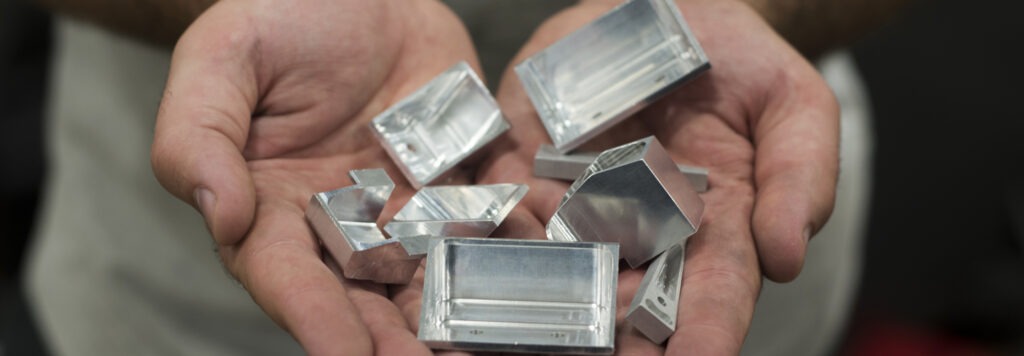
Project Details:
- The Challenge: Fabricating a wide range of products including carbon-fiber composite aircraft wings, intricate molds, and machined parts in aluminum and aerospace alloys, in an unattended environment.
- The Solution: Mastercam, industry-leading CNC software for CAD/CAM operations.
- Benefits:
- 5-axis Dynamic Milling toolpaths for complex geometries and roughing: the toolpaths run fast and minimize handwork after machining.
- Verify function allows programmers to review toolpaths prior to machining, protecting the tools and mitigating risk to the tool, material, and shop.
- Productivity+™ allows the incorporation of in-process gaging and tool breakage detection using Renishaw probes on machines.
- Carbon Fiber Trimming ability allows hundreds of parts to be trimmed mechanically, saving hours of time.
In 2012, Flying S moved its design and manufacturing team of 15 to a new facility across the road. One of the people who made that move was Peter Bowman, a graduate of the manufacturing program at nearby Vincennes University and the Masters Apprenticeship Program at the Haas Automation factory in California. Bowman brought with him a familiarity with a broad range of Haas CNC equipment; a connection to Vincennes; and proficiency with Mastercam, which is used extensively both at VU and Flying S.
In the summer of 2016, a new building expansion was completed to give the team more room to develop and grow—it had grown by more than 300 percent to about 50 people in just five years.
Bowman leads a team of programmer/machinists who all write programs and operate equipment, so they are intimately familiar with how changes in programming strategies affect manufacturing outcomes. Successful strategies are standardized and shared with other programmers via the shop’s manufacturing database, which contains thousands of programs.
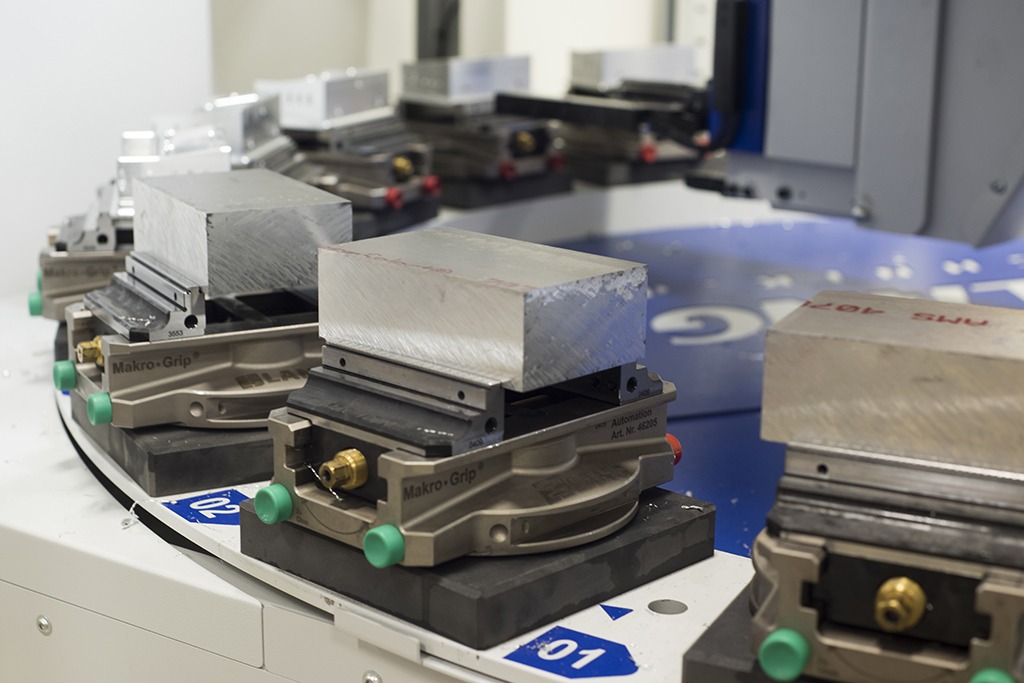
The shop team spends a great deal of time programming and cutting molds used for making composite Unmanned Aerial Vehicle (UAV) airframe structures from carbon fiber for commercial and military customers. These freeform shapes can be intricate, with up to three to four million lines of code, and they can run unattended on their CNC equipment for up to a week at a time. Oftentimes the team is tasked with producing one of these molds every other day, requiring efficient programming capabilities, along with manufacturing strategies, that optimize material removal on the machine.
Optimization begins with a solid model. The software’s Model Prep function allows programmers to manipulate solids directly, without having to go back to the design team. “It eliminates waiting, duplication of effort, and keeps the work moving forward,” said Bowman.
The team at Flying S relies heavily on toolpaths incorporating Dynamic Motion technology which constantly maintains the tool vendor’s chip load recommendations for safe optimal removal rates. Bowman noted that these toolpaths are easy to program, and link to one another with smooth transitions minimizing handwork after machining. The toolpaths are so stable they can be used with confidence for days on end in unattended operation. He also credited his Mastercam Reseller ShopWare, Inc., with careful editing of posts to ensure that outputs to each of the 5-axis machines are in precise alignment with the intent of the programs.
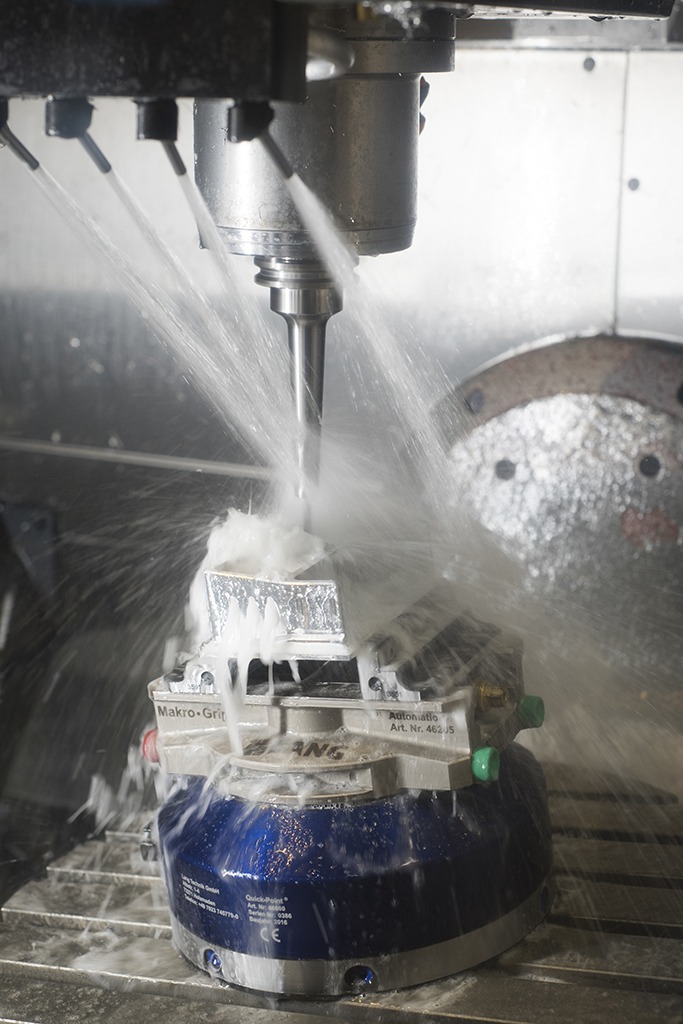
Bowman shared, “Whenever we go to do a large mold, for example, we always use the same tools to rough, and we always use the same feeds and speeds. Despite the fact that we might have up to 12 different guys who would be able to program that particular part, we are always using the same process. We use Mastercam’s tool libraries very extensively. They have been a great risk mitigator.”
Bowman went on to say, “A lot of times we’ll actually run unattended, even on parts that we never ran before. We feel that confident in Mastercam to hit ‘cycle start’ and let the job go.” More than a third of the programs written incorporate in-process gaging and tool breakage detection and work in tandem with the machines’ Renishaw probes. Bowman said: “It’s another way our guys can do more with completely unattended machines.”
He indicated that the majority of carbon fiber parts manufactured for the aerospace and racing industries are trimmed manually. Bowman noted, “I almost laughed when our CAD/CAM Reseller told us we could create multiaxis edge trim programs with a few button clicks in Mastercam. I told him we have to have that and gave him my credit card on the spot. Today we can machine a complex UAV flight component out of carbon fiber and have it fit a part we made several years ago perfectly. It’s not uncommon for us to trim hundreds of parts a day using both 3-axis and 5-axis CNC and Mastercam.”
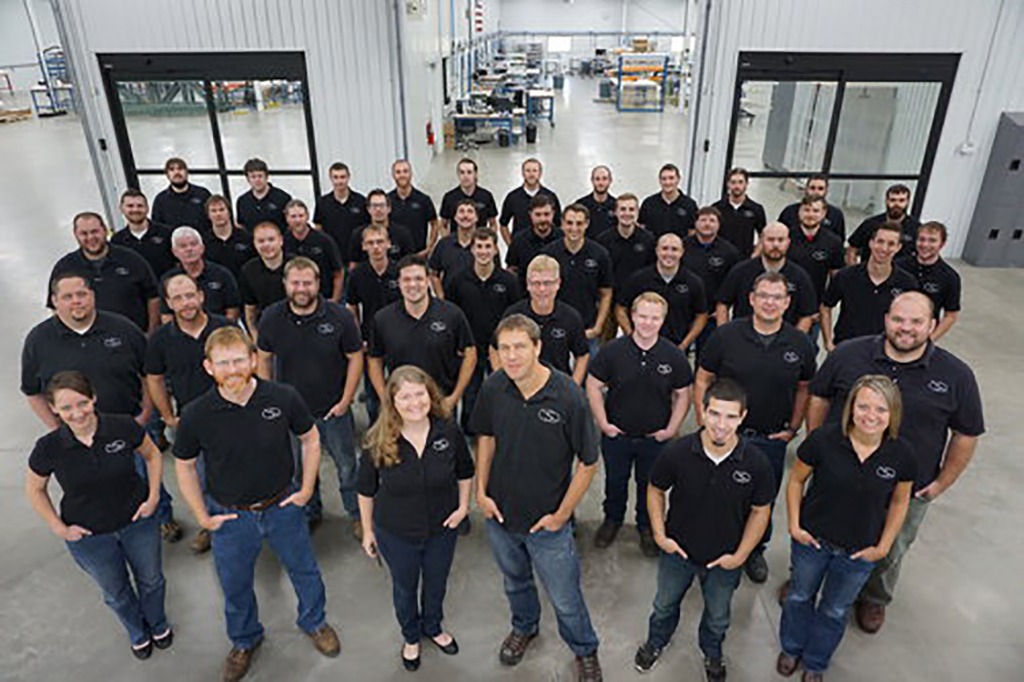
Customer Quote
“A lot of times we’ll actually run unattended, even on parts that we never ran before. We feel that confident in Mastercam to hit ‘cycle start’ and let the job go.”
– Peter Bowman, Manufacturing Engineer, Flying S, Inc., Crawford County, Illinois
Reseller Quote
“I almost laughed when our CAD/CAM Reseller told us we could create multiaxis edge trim programs with a few button clicks in Mastercam. I told him we have to have that and gave him my credit card on the spot. Today we can machine a complex UAV flight component out of carbon fiber and have it fit a part we made several years ago perfectly.”
—Peter Bowman, Manufacturing Engineer, Flying S, Inc., Crawford County, Illinois