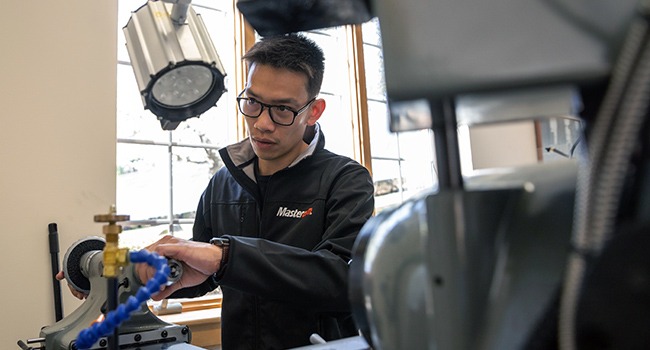
The irony in automation is that it takes a lot of creativity to automate any process, but at the same time any automated process has zero inherent creativity – it is just a mindless repetition of preselected steps. While it is good for the process itself to be uncreative (no one wants their machining to go off-script), programmers themselves must often stretch their imaginations when finding ways to automate and save time. Here are a few CAM automation tricks Mastercam users can put to work today.
Importing Families of Operations
Imagine working on a run of parts that have the exact same proportions but vary in size. This is a common occurrence in many automotive, mold, and job shops. Instead of programming each iteration completely from scratch, Mastercam gives you the ability to bring in a family of operations and then customize each for that specific part. Simply program the first part, save the library of operations, import that series of operations to the next part, and adjust parameters to fit. This trick works even if the two different parts are manufactured years apart. Users need only import operations from the old Mastercam file by selecting Operations Manager >> Import >> Browse >> and then the file you want to select from.
Organizing Geometries
Similar to importing families of operations, users can also keep standard part and toolpath geometries on hand for quick selection. Many shops are using the same roughing, semi-finishing, and finishing tools for every part made from the same material. Saving the tried-and-true cutting parameters from job-to-job will save time and ensure reliable repeatability. With Mastercam, its easy to drag and drop a geometry group from one 3D high speed toolpath to another.
Using Unified
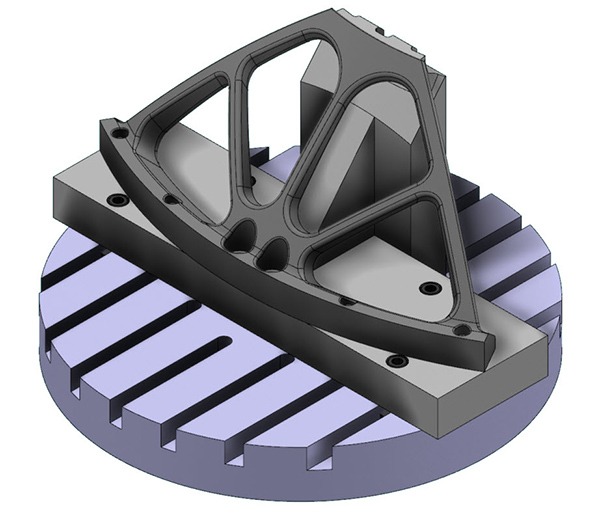
New with Mastercam 2022 is the Unified Multiaxis Toolpath. Previously, programmers had to find each multiaxis toolpath and apply it to the model iteratively. Users can now find Morph, Parallel, Along Curve, and Project Curve all in one easily-accessible place. This change saves programmers valuable mouse miles and time.
Automating Toolpath Execution
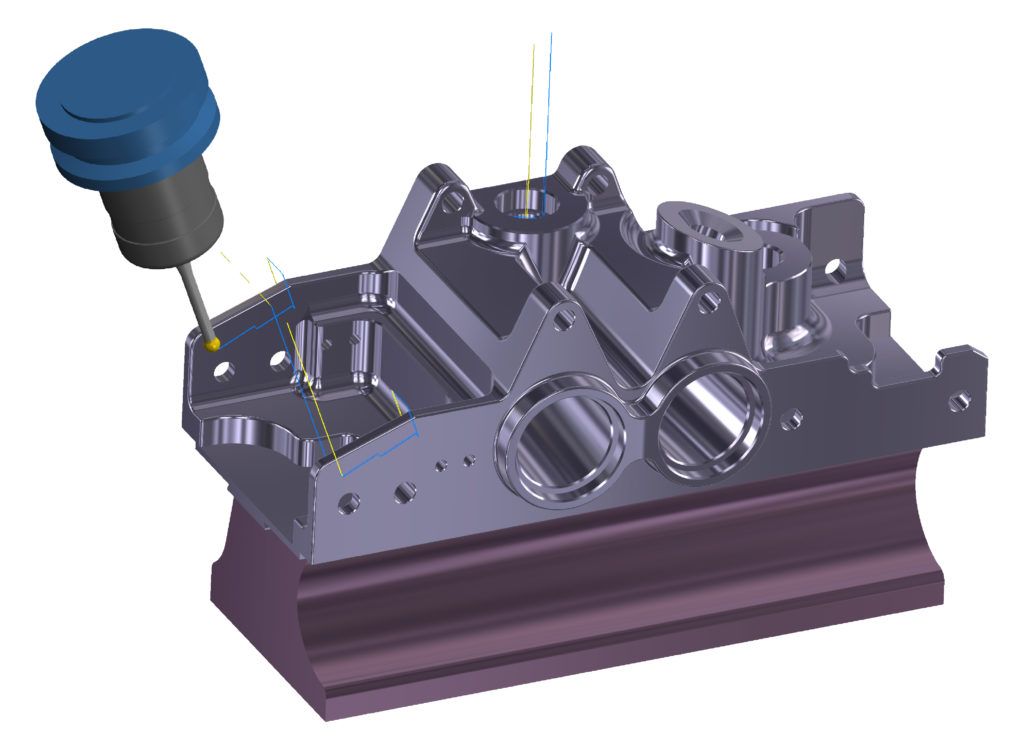
Renishaw Productivity+ is an add-on designed to consolidate measurement and probing into the Mastercam interface. Productivity+ supports the CAM process before (with set-up and tool identification), during (with tool motion monitoring and adaptive machining), and after machining (with post-process reports). With it, users can take advantage of iterative probing and branching/looping logic to adapt to changing in-process conditions. The metrics provided by Productivity+ will prompt users to take appropriate action right then and there.
Using Batch Mode
Batch processing makes it possible to create multiple operation flows at once. Mastercam’s Batch mode runs large, reoccurring toolpath generation sessions – as well as machine simulations – and saves them together for future use. For example, a user could run a set of Mastercam Lathe operations, save the in-process stock model, load that model into a Mastercam Mill session, run a pre-selected set of Mill operations, save the final stock model, compare it to the intended design model, and save the report out – all in the background of Batch mode.
Want to Learn More about CAM Automation?
The irony in automation is that it takes a lot of creativity to automate any process, but at the same time any automated process has zero inherent creativity – it is just a mindless repetition of preselected steps. While it is good for the process itself to be uncreative (no one wants their machining to go off-script), programmers themselves must often stretch their imaginations when finding ways to automate and save time. Here are a few CAM automation tricks Mastercam users can put to work today.
Importing Families of Operations
Imagine working on a run of parts that have the exact same proportions but vary in size. This is a common occurrence in many automotive, mold, and job shops. Instead of programming each iteration completely from scratch, Mastercam gives you the ability to bring in a family of operations and then customize each for that specific part. Simply program the first part, save the library of operations, import that series of operations to the next part, and adjust parameters to fit. This trick works even if the two different parts are manufactured years apart. Users need only import operations from the old Mastercam file by selecting Operations Manager >> Import >> Browse >> and then the file you want to select from.
Organizing Geometries
Similar to importing families of operations, users can also keep standard part and toolpath geometries on hand for quick selection. Many shops are using the same roughing, semi-finishing, and finishing tools for every part made from the same material. Saving the tried-and-true cutting parameters from job-to-job will save time and ensure reliable repeatability. With Mastercam, its easy to drag and drop a geometry group from one 3D high speed toolpath to another.
Using Unified
New with Mastercam 2022 is the Unified Multiaxis Toolpath. Previously, programmers had to find each multiaxis toolpath and apply it to the model iteratively. Users can now find Morph, Parallel, Along Curve, and Project Curve all in one easily-accessible place. This change saves programmers valuable mouse miles and time.
Automating Toolpath Execution
Renishaw Productivity+ is an add-on designed to consolidate measurement and probing into the Mastercam interface. Productivity+ supports the CAM process before (with set-up and tool identification), during (with tool motion monitoring and adaptive machining), and after machining (with post-process reports). With it, users can take advantage of iterative probing and branching/looping logic to adapt to changing in-process conditions. The metrics provided by Productivity+ will prompt users to take appropriate action right then and there.
Using Batch Mode
Batch processing makes it possible to create multiple operation flows at once. Mastercam’s Batch mode runs large, reoccurring toolpath generation sessions – as well as machine simulations – and saves them together for future use. For example, a user could run a set of Mastercam Lathe operations, save the in-process stock model, load that model into a Mastercam Mill session, run a pre-selected set of Mill operations, save the final stock model, compare it to the intended design model, and save the report out – all in the background of Batch mode.
Want to Learn More about CAM Automation?
Get in touch with your local Mastercam Reseller today to start learning about how Mastercam can help you with CAM automation. Simply fill out the form to start the conversation.
Get in touch with your local Mastercam Reseller today to start learning about how Mastercam can help you with CAM automation. Simply fill out the form to start the conversation.